By Bruce Geiselman
Software developer Diversys is offering a cloud-based Software as a Service (SaaS) that can help users comply with companies’ sustainability goals and new Extended Producer Responsibility (EPR) policies and recycling mandates.
EPR laws are well-established in Europe, and in recent years local governments in the United States and Canada have increasingly been adopting and considering similar legislation. Diversys’ solution can help plastics recyclers and processors overcome the burden of accurately tracking and reporting details of their recycling operations.
“Diversys was founded in 2019 in Toronto, Canada, and this is a province that's heavily focused on EPR legislation,” which pushes responsibility for recycling onto producers, said Roger Barlow, CEO and co-founder of Diversys.
“I saw that recycling companies, specifically around tires at that time, were paying a fortune to run their IT systems, and I thought there had to be a better way. So, I built a better way with a solution that allows companies in the recycling industry to easily, simply and cost-effectively improve their reporting and operational efficiencies. In a nutshell, we capture lots and lots of data at every stage of the plastics reverse supply chain, allowing a phenomenal level of detail associated with the tracking and tracing of that plastic so that companies can prove their recycling claims, as well as improve their operational efficiencies.”
Though initially focused on tire recyclers, Diversys’ software is material-agnostic, meaning it can be used for tracking plastics, aluminum cans, or any material that can be recycled.
For the plastics industry, the software can track recycling of post-industrial or post-consumer waste within a single plant, companywide or across the entire reverse supply chain from one party to another.
“We capture information about all the parties that are involved from the party that is transferring the materials to the receiving party,” Barlow said. “We geotag it, which means we know where the transaction took place. We timestamp it. We can associate dollar values with the plastic. We could track as many types of plastics as needed, in any form as required, and so much more. And then, based on this information we capture, we can generate reports and dashboards and other data visualizations that can help plastics producers know ... how much recycled materials they're using.”
On our podcast
On the PMM Insight podcast produced by Plastics Machinery & Manufacturing, Barlow described how Diversys software functions and its benefits.
This data drives real-time decisions, visualizations, insights and compliance reporting, according to the company. Diversys can replace or seamlessly integrate with existing systems without requiring a full overhaul.
The phone apps are simple to use, Barlow said, comparing them to using an app like Facebook.
“Almost all the information is automatically captured by the application because we don't want people entering information, as it slows things down, and errors and omissions and other issues can occur,” Barlow said. “When a customer signs up with Diversys, we configure the software to match their business workflow so that when the data is captured, we know so much about their business that we can automatically capture most of the details without human input, and the capture is done either on a smartphone, a tablet, or even just a computer terminal that's sitting in the facility. We've really made it so simple to use that a transaction can be performed in seconds, whereas it normally used to take minutes if not longer.”
Customers don’t need to buy any special hardware, and since it is an SaaS, there is no big upfront investment. Customers can be reassured that their data is backed up and they don’t need to worry about losing data in the event of a computer crash, fire or other disaster. At the same time, Diversys takes steps to ensure data security.
“It's built on all modern software architecture that is extremely robust and designed around user privacy,” Barlow said. “Everything on our site sits in the cloud as encrypted [data]. It's triple backed up for redundancy, and we can store the information in any location that a customer requests. If there is a need to keep it within a certain jurisdiction, we can accommodate that. Our reputation and success are contingent on our ability to meet our customers’ privacy needs, so we take it extremely seriously.”
Contact:
Diversys, Toronto, 877-909-2783, www.diversys.com
Bruce Geiselman
Senior Staff Reporter Bruce Geiselman covers extrusion, blow molding, additive manufacturing, automation and end markets including automotive and packaging. He also writes features, including In Other Words and Problem Solved, for Plastics Machinery & Manufacturing, Plastics Recycling and The Journal of Blow Molding. He has extensive experience in daily and magazine journalism.
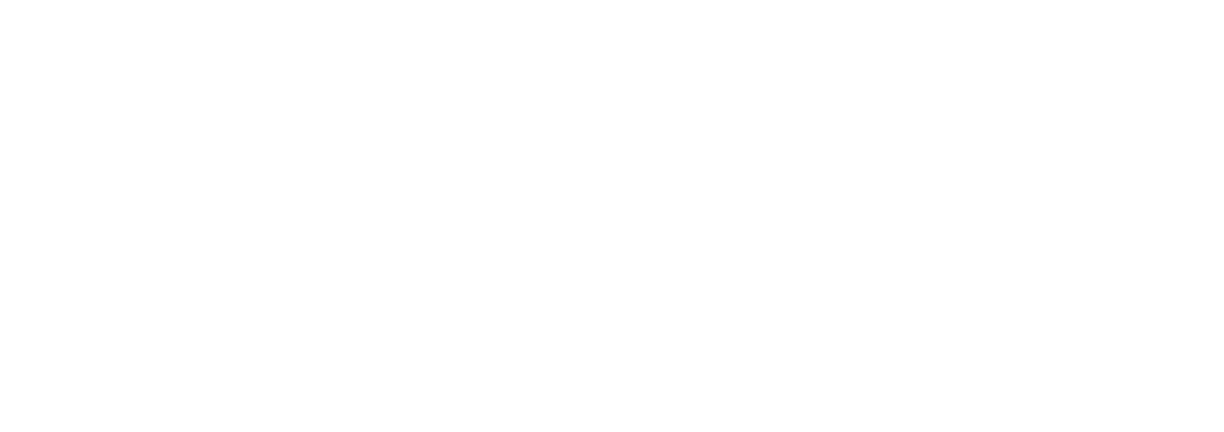