Automotive injection molder tries out IIoT platform Snap Signal
By Bruce Geiselman
Snap Signal, an IIoT product line launched in April, makes it easier for plastics processors and other manufacturers to upgrade to Industry 4.0 and boost productivity, according to industrial automation manufacturer Banner Engineering.
Snap Signal captures data from nearly any industrial machine without tying into the PLC and converts it into a common protocol, which eliminates complexity from monitoring industrial equipment. Adding IIoT can significantly reduce downtime and improve overall equipment effectiveness, said Sean Foley, business development manager at Banner Engineering.
The product line can be used to build a brand-agnostic IIoT platform that’s composed of modular hardware and software. It can capture and convert machine signals and protocols including Modbus, analog, discrete, serial and IO-Link.
The platform can collect condition- and process-monitoring data from existing devices including sensors, motor controllers and lights by using a splitter connection to monitor the signals in what is called an “overlay network.” This network captures the signals without requiring changes to the existing control infrastructure, reducing the potential of damaging the infrastructure, as well as the time of installation, according to the company.
Data can be sent to various locations including a cloud dashboard or supervisory control and data acquisition system for remote monitoring or to other PLCs and HMIs. Customers can start small with an IIoT pilot project using Snap Signal to manage costs. After running the project long enough to determine return on investment, they can easily scale up the scope of monitoring.
The platform includes signal converters, wireless networking, IO-Link masters and hubs, and an industrial controller, all of which use industry-standard M12 connectors for simple installation. An optional cloud platform, Banner Cloud Data Services, is available for users without a dashboard solution already in place.
The Snap Signal platform can be added to existing equipment, particularly legacy equipment. It can tap into data collected by existing sensors on a machine, or users can add new sensors.
Some people think that since IIoT is cutting-edge technology, it can only be applied to new machines and new equipment, Foley said.
"What we've found is the opposite in most cases,” Foley said. “Most of IIoT's value we find is in retrofitting existing machines and legacy equipment. ... The average age of manufacturing assets in the United States is around 20 years old; so, there are a lot of machines out there that have been running for decades, and they're working fine, but they could be working even better by adding IIoT technology to them.”
The ability to collect data from existing sensors without disturbing the existing control system or from installing new sensors is attractive for many reasons, Foley said.
“For one, it minimizes the risk,” he said. “We’re not diving into their control cabinet. A lot of end users are not allowed to dive into the OEM’s PLC. They’re not even allowed to dive into the code. We’re giving them the ability to gather and unlock the data that’s there.”
Parameters that are typically monitored include machine vibration. As vibration increases, so can damage to the machine.
Banner Engineering can help plastics processors add sensors to monitor the humidity and temperature in drying and conveyance systems to ensure resin pellets are processed without excessive moisture, said Luke Karnas, director of global business development.
Processors can monitor when an injection molding machine is running low on pellets and use sensors and probes to monitor the temperature and humidity in resin drying systems. Temperature sensors on other critical equipment also can alert processors when system temperatures are too high or too low for optimal performance.
Optimizing older machines
In a pilot project, SRG Global, Troy, Mich., is using the Snap Signal platform with temperature and humidity sensors on dryer hoppers and pneumatic conveyance systems feeding pellets to older injection molding machines in two of 13 plants. The company makes grills for trucks and appliques such as side molding for vehicles.
The company is measuring the temperature and humidity of the air in which the resins are stored and conveyed to try to predict and eliminate conditions that might lead to splay, a cosmetic defect involving streaking along the surface of a molded part.
The data from those sensors is sent to Banner Cloud Data Services, where it is analyzed, and the results are available to company employees on tablets or smart devices remotely or on monitors in the factory.
While the sensors measure the temperature and humidity in conveyance systems and hoppers, SRG Global cannot determine the moisture level inside the pellets. It is trying to determine the atmospheric conditions that might indicate excessive moisture is present in the pellets, with the goal of recognizing when a sample of pellets should be checked with a moisture analyzer.
“When we run resins like ASA [acrylonitrile styrene acrylate], ABS, and PC/ABS [blends] — all these manufacturers will have a recommended moisture content,” said James Barber, a reliability engineer with SRG Global. “We’ll get an alert [when the atmospheric temperature and moisture conditions are outside of a preset range] and then we can go get that sample checkup with the moisture analyzer and see if our specifications have been compromised.”
Banner Cloud Data Services, using information collected by the Snap Signal system, can send out alerts via email, text message or a Microsoft Teams message, Barber said.
“What we found very attractive about this technology is that it’s very affordable and easy to install,” Barber said. “I can’t speak enough about the ease of installation. We can take a wireless node and a sensor — we can put it online and get [the data] to the cloud. The installation is quick, within five to 10 minutes. After installation, we’re already reading data.”
Color icons indicate the temperature and humidity conditions. If an icon is green, everything is operating within normal parameters. If the icon turns yellow, conditions are approaching a critical threshold, and if the icon turns red, conditions are out of specification. When icons turn yellow or red, alerts are sent to employees.
Barber said he expects using the Snap Signal platform will reduce the amount of scrap.
Room for growth
SRG Global already is looking to expand its use of Snap Signal to injection molding machines (IMMs) and additional conveyance systems and hoppers, and to measure additional parameters, including temperatures on cylinders to identify possible seal failures and the amperage draw on heater bands. Additional condition monitoring also is a possibility, Barber said.
“What we think that's going to help us do is be able to predict failures before they occur,” Barber said. “We're going to get that advanced warning when we need to. Now, with supply chain issues, getting a seal kit for a tonnage cylinder or getting a cylinder rebuilt — the lead times are catastrophic. So, being able to get that advance notice and being able to get that critical spare part ordered and on the shelf before failure happens is going to be a great value-add for us.”
While it’s employed the Snap Signal platform in only two of its plants, the automotive-parts supplier is using various process monitoring technologies, including vibration, temperature and humidity sensors, across 12 of its 13 plants to monitor IMMs, auxiliary equipment and cooling systems, as well as equipment unrelated to plastics processing, Barber said.
Condition monitoring allows the company to proactively order spare parts and schedule maintenance to reduce unplanned downtime due to equipment failures. It’s “a maintenance transformation,” Barber said. “Oftentimes, you do preventive maintenance, and it's ineffective. What we're doing now is moving from time-based to condition-based maintenance.”
Maintenance technicians of yesterday were equipped primarily with a toolbox stocked with wrenches, sockets and ratchets. However, in the future, maintenance technicians’ most valuable tool could be a tablet that allows them to look at cloud-based software to determine when and where maintenance is required, Barber said.
Bruce Geiselman, senior staff reporter
Contact information:
Banner Engineering, Minneapolis, 888-373-6767, www.bannerengineering.com
Bruce Geiselman | Senior Staff Reporter
Senior Staff Reporter Bruce Geiselman covers extrusion, blow molding, additive manufacturing, automation and end markets including automotive and packaging. He also writes features, including In Other Words and Problem Solved, for Plastics Machinery & Manufacturing, Plastics Recycling and The Journal of Blow Molding. He has extensive experience in daily and magazine journalism.
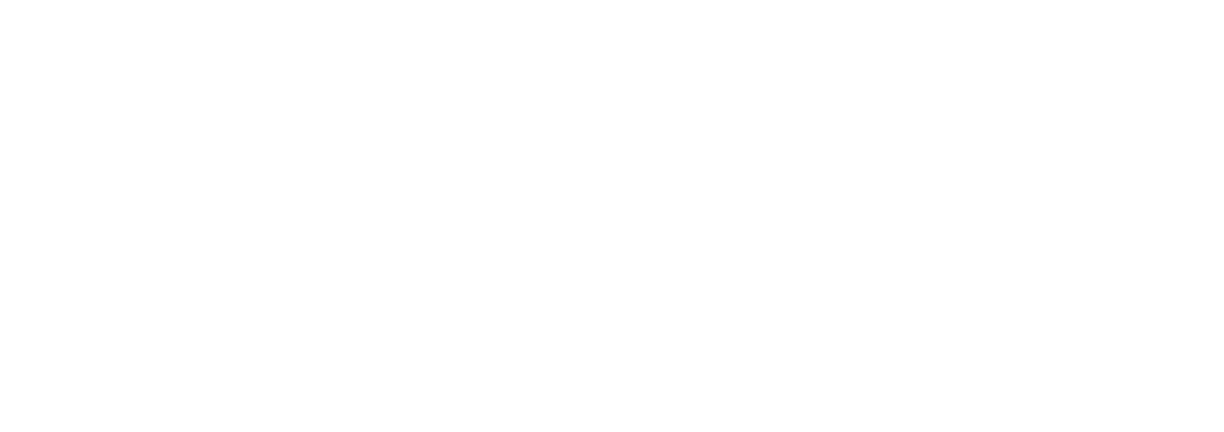