Dedication to purging protocols saves processor time, money, resin
Captive molder CH3 Solutions uses more than 20-plus colors for the PP tiles it creates for spaces such as basketball courts and garages.
But, when it comes to color changes, the company can’t abide either lost time or wasted resin. Instead, it adheres to a strict protocol, using purging compounds to maintain product quality and equipment performance. The company and the maker of the purging compounds it uses, say the products go a long way toward saving resin.
“We [have] pretty much built a culture around using purge for every color change, no skipping. Even if we go from a lighter color to a darker color, we still use it because we don’t want any kind of buildup in our barrels, and we want to keep our screws nice and clean. And when we have pulled screws, they’ve come out in really good shape,” said Rodney Davenport, VP of CH3, a subsidiary of the Recreational Group, based in Dalton, Ga.
With just six Wintec injection molding machines with clamping forces ranging from 730 tons to 1,500 tons, CH3 probably pours in purging compound about 10 times a week, Davenport said, using the product before plant shutdowns and for every color change.
It’s a practice that’s paid off.
“It’s worked out really well for us to keep our scrap percentages well below 1 percent, sometimes even half a percent, based off of about 6 million pounds of material run per year,” he said.
Interest in purging compounds is increasing, said Thomas Hanvey, senior marketing manager for Asahi Kasei Asaclean Americas, which sells most of the purging compounds CH3 uses.
“It’s a combination of the resin prices and, I think, inflation in general,” said Hanvey, who added that environmental concerns, too, play a role in some processors’ interest in the products.
With Asaclean’s introduction last year of a heat-activated purging concentrate, called Plus Grade, CH3 has found a solution that works for most of its applications, Davenport said. Users of the concentrate need much less of the compound than they would when using purging material in other forms.
For instance, Davenport estimated CH3 will use only about 1,000 pounds of the concentrate in a year — a fraction of the amount it needs when it’s used purging material in other forms.
“We're not having to use a ton where, like with … normal purge, you’re filling up the barrel, you’re using all of that purge compound. So, obviously, we’re using more polypro[pylene] but at a cheaper cost. And, so, that’s where that Plus Grade kind of offsets the cost to buy just regular purge. Because before we would have to purge, run the barrel out, put the purge in and then follow up with resin, where now we don’t have to do that. We just drop a few pellets of the Plus Grade in there, and we’re good to go,” Davenport said.
Hanvey conceded that, by weight, purging compounds are more expensive than some commodity-grade resins, like PE or the PP CH3 runs, but over the long term, relying on resin alone to clear out IMMs — as some processors still do — is significantly more wasteful and less efficient.
Using the next resin to drive out the last resin ultimately is time-consuming and costly, said Hanvey, who recommends that molders consider the cost-per-purge breakdown, rather than simply the cost per pound of material.
"Because the 'next resin up' isn’t designed to clean, the production resin layers on the flights of the screw, on the barrel, and in other low flow areas in the machine. Eventually, those layers of previous resin burn, and the processor will start noticing carbon/black specks, or chunks of color from a previous run will start working their way out into parts," Hanvey said. "Sometimes these colors won’t come up for several changeovers, but either way, contamination is occurring."
A color change that might take 10 minutes with a purging compound can take two hours for processors that opt to just switch colorants and continue producing parts till the contamination is no longer noticeable, he said.
Screw changes can take four or five hours, and contamination sometimes can force molders to undergo unplanned maintenance to pull their screws — a situation Hanvey calls an "unforced error."
At CH3, those kinds of especially costly shutdowns aren’t necessary.
With Asaclean’s Plus Grade, CH3 has an easy — and familiar — process to follow. Because they need so little of the compound, the company’s 17 employees keep it at the machines and don’t have to wander the plant for different formulations. It’s easy to use, so they know the procedure: Run parts till there’s a color change, purge, repeat.
To Davenport, the benefits of the routine are obvious.
“We actually had bought some companies and inherited some molds and they didn’t use purge compounds,” he said. “So, we found out the first few times that we were doing color changes, it was taking us an hour, lots of scrap and stuff, but now that we’ve implemented our purge program, the tools have been run through our stuff, now the color changes are ... less than 15 minutes.”
Karen Hanna, senior staff reporter
Contact:
Asahi Kasei Asaclean Americas, Parsippany, N.J., 973-257-1999, www.asaclean.com
Karen Hanna | Senior Staff Reporter
Senior Staff Reporter Karen Hanna covers injection molding, molds and tooling, processors, workforce and other topics, and writes features including In Other Words and Problem Solved for Plastics Machinery & Manufacturing, Plastics Recycling and The Journal of Blow Molding. She has more than 15 years of experience in daily and magazine journalism.
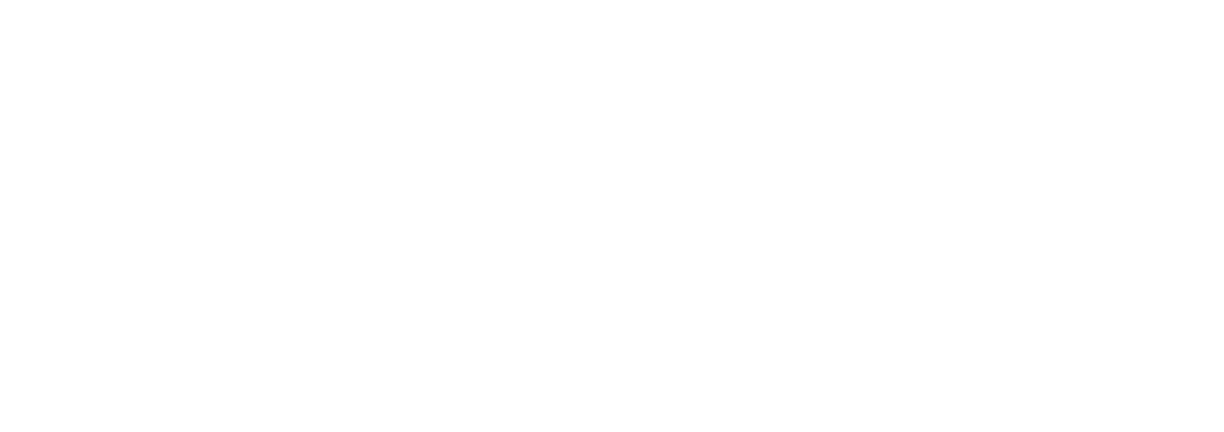