From scrap to spools: Axjo prospers through vertical integration
By Ron Shinn
Injection molding is a tough business and market vagaries can make recycling even worse. But to put them together under the same roof and prosper is a rare success story that shows a quality product, strong management, technical expertise and — in the case of Axjo America — an overriding commitment to green manufacturing.
Axjo America, in Conover, N.C., scours the country for post-industrial scrap, primarily from OEMs that use large amounts of plastic in their products. Scrap from products like milk crates, gas tanks and garbage cans are reprocessed in the Axjo plant, then injection molded into spools and reels used to hold a wide range of products, such as wire and cable in the energy and telecommunications industries. A small amount of post-consumer material is also recycled.
“Our spools are made from 100 percent of our own regrind,” said Tony Panozzo, managing director of Axjo America. “We do our own blending here as well and we have our own mixing machines.”
By investing in recycling equipment, Axjo controls more of its manufacturing process. Most processors are beholden to recyclers to supply reprocessed resin, so recyclers exert control over availability, quality and price of the material. With in-house reprocessing, Axjo can control the resin’s melt flow, viscosity index and material variations, as well as supply, much more closely.
Axjo America’s parent company is Axjo Plastic AB, a 77-year-old private company in Gislaved, Sweden. It operates under a sustainability principle it calls Greenology that aims to lower the carbon footprint of its manufacturing plants around the world.
The formula is working. Business is booming for Axjo in North America. The company has 19 Wittmann Battenfeld injection molding machines, including two that went into operation in late 2021, and three more scheduled to arrive later this year. It is shopping for a new recycling line that can increase capacity to more than double the current 1,000 pounds per hour.
Spools in North America have traditionally been made mostly from wood, but there are also metal and plastic versions. Panozzo estimates the mix is shifting and about 60 percent are now made from plastic. Axjo makes only plastic spools and is either No. 1 or No. 2 in the market. It makes spools in standard sizes as well as custom sizes.
Weight, recyclability and sustainability are all selling points for the Axjo spools. A 4-foot-diameter wood spool might weigh 88 pounds empty; the Axjo 4-foot spool weighs just 40 pounds.
Panozzo said users also like being able to throw used spools into a single-stream recycling system when empty. “It is a big selling point,” Panozzo said. “You can take an Axjo spool as it is and throw it into a recycling bin or back into a process. You don’t have to take it apart. There is no wood, steel rod or cardboard to take apart.”
He also said that for customers with sustainability goals, buying spools made from 100 percent recycled plastic that can be recycled again is a benefit.
Panozzo said he is exploring a direct buyback program where empty spools could be returned to Axjo.
Barry Carson, director of operations, said obtaining a good, consistent stream of material is his biggest challenge. Finding and acquiring the material is a full-time job for one Axjo employee. One point in Axjo’s favor: “Every pound of scrap we get, our supplier is trying to eliminate it,” Panozzo said.
The North Carolina plant currently manufactures spools in diameters measuring from 3.5 inches to 1.65 feet. Later this year it plans to add a 2-foot version. Larger spools are manufactured in Sweden.
The three additional molding machines this year will fill Axjo’s 143,200-square-foot building, a former textile manufacturing facility, and continued growth will likely dictate moving to a larger plant within two years, according to Carson.
“We grew 41 percent in sales last year and we are trying to control that growth,” Carson said. “We see good growth for the next three to five years.”
Axjo started manufacturing in the U.S. 11 years ago and moved into the Conover plant seven years ago.
Carson said some polyolefins can be reprocessed up to 10 times without physical or mechanical degradation. “The more times we recycle, the better it is for the environment,” Carson said. “It keeps the cost of the products as low as possible for our customers, so it is a win-win-win. It is a win for the company, win for the customer and win for the environment.”
Axjo’s 19 Wittmann Battenfeld presses range from 180 to 650 tons of clamping force. The oldest was delivered in 2006. The two new presses are an 180-ton model and a 500-tonner. The presses to be added later this year will push the size range to 1,100 tons of clamping force.
Each press is equipped with either an ABB six-axis floor-mounted robot or a Wittmann Battenfeld crossbeam robot. Auxiliaries such as dryers and temperature control units are also from Wittmann Group.
Axjo plants worldwide use Wittmann Battenfeld presses. Carson said having a single brand in his plant makes operator training and maintenance easier. “The operators get very comfortable with how the machines operate,” he said. Standardizing on Battenfeld presses also improves machine uptime, he said.
Operators and technicians find the company’s Unilog control system easy to use, he said.
Approximately 730,000 pounds of resin is reprocessed and used for spools each month. Some 95 percent is PP or PE. The remaining 5 percent is ABS, PS and high-impact PS.
The plant has about 50 team members and runs 24/7. There are now just three job openings.
Carson said Axjo is investing in health, safety and security improvements for employees as well as modern processing equipment. “The No. 1 thing for me is the employees,” he said. “I am big on training, particularly safety training.
“We are trying to become a company of choice in this community,” Carson said. “We are trying to create a work-life balance that actually becomes an attraction within itself.”
All technical staff will complete scientific molding training this year, Carson said. And some 16 employees have recently been certified as safety first responders.
Carson, who came to Axjo in late 2021 after 25 years in medical and pharmaceutical molding plants, has a two-year plan to turn the molding operation into a lights-out or at least lights-dimmed facility.
“We have a massive automation program in the budget,” Carson said. “Battenfeld presses have a wonderful array of tools that support that.” He said the goal is to have each operator increase productivity by three times over the next 24 months.
In the reprocessing area, there is a system that shreds, granulates and recycles the material into usable pellets. The extruder is a single-screw unit.
“We are continually looking at new technology to reprocess the material,” Carson said. “Depending on the equipment we have in here, it opens us up to more variations.”
Because the plastic scrap comes from many different sources, Carson said Axjo typically processes a 1,000-pound sample. “We are looking for processability,” he said. “We need a clean, consistent stream of reprocessed resin.”
Axjo’s manufacturing plant in Sweden sources a big part of its material from post-consumer fiber and film products that contain a lot of PP. While the North Carolina plant looks more for rigid plastic scrap, it also reprocesses things like potato chip bags, which contain a high percentage of biaxially oriented PP.
The success of Axjo’s spools is based on more than just substituting recycled plastic products for wood and steel versions. The company continues to innovate the seemingly simple product. For example, it designed a two-piece version of its popular 1.65-foot-diameter spool that easily snaps together. Shipping spool halves means Axjo can increase the density of spools on a truck by 2.5 to 2.8 times, Panozzo said.
“We send one truck, but the customer is getting almost three truckloads worth of spools,” Panozzo said. The savings in shipping costs can be passed along to the customer and sending one truck instead of three is another win for the environment.
Contact:
Axjo America, Conover, N.C., 828-322-6046, www.axjo.com
Just the facts:
COMPANY: Axjo America
ESTABLISHED: 2011
HEADQUARTERS: Conover, N.C.
PARENT: Axjo Plastic AB in Sweden
TOP OFFICIAL: Tony Panozzo, managing director
Employees: 50
Ron Shinn | Editor
Editor Ron Shinn is a co-founder of Plastics Machinery & Manufacturing and has been covering the plastics industry for more than 35 years. He leads the editorial team, directs coverage and sets the editorial calendar. He also writes features, including the Talking Points column and On the Factory Floor, and covers recycling and sustainability for PMM and Plastics Recycling.
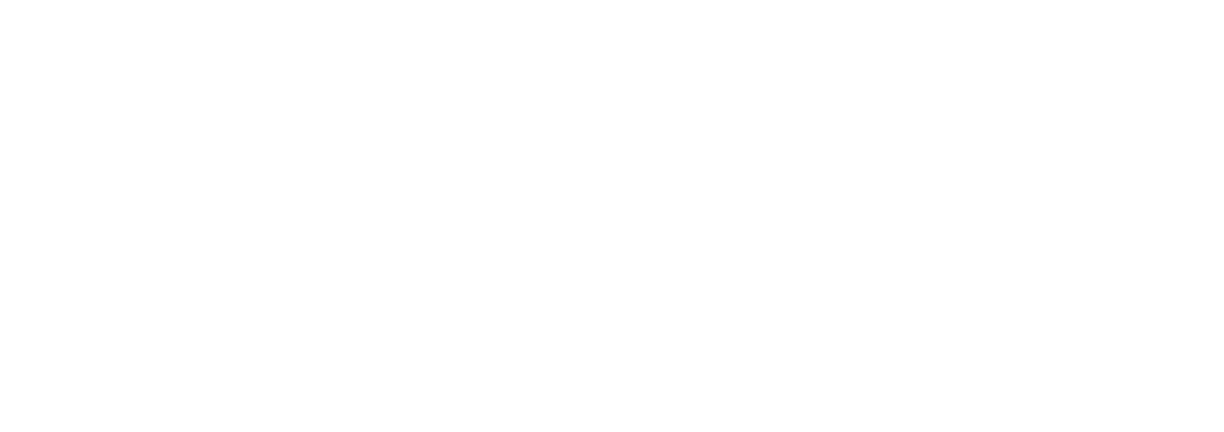