Arburg, Wittmann Battenfeld, Nissei meet challenges of recycled resins, bioplastics
Part 3 of a series on injection molding machinery that tackles recycled materials and new resins.
Processors aren't on their own when they decide to tackle tricky new bioplastics or recycled resins; increasingly, machinery OEMs have their backs.
Arburg
It takes a village to achieve a true circular economy, according to Bertram Stern, circular economy manager at Arburg.
“The circular economy will only work with the full cooperation of all players throughout the process chain — from the material suppliers to the mold construction companies and injection molding machine manufacturers, right through to the recyclers,” Stern said. “Recyclates present new challenges when it comes to injection molding, as even high-grade, homogeneous post-industrial recyclate can vary significantly in terms of quality.”
Related: Engel adapts to circular economy; Wilmington's specialty machinery adds value to recycled materials
Injection molders are not willing to sacrifice product quality to use recycled materials.
“The solution is to use better recyclates and injection molding machines which can compensate for fluctuations in quality,” Stern said. “This can be done by providing the operator with digital support — for example, with the Arburg assistance systems — so they can manage the injection molding process quickly, safely and efficiently.”
Part of the circular economy is designing parts that can easily be reused or recycled. Arburg used post-consumer resin (PCR) from household waste to make parts for its injection molding machines.
“An electric dual-component Allrounder 630 A was used to turn post-consumer recyclate based on PP and TPE into handles for the safety door of Allrounder injection molding machines,” Stern said. “The post-consumer recyclate was processed using the ProFoam foaming process and the two foamed handle halves were assembled in the mold complete with inserts. To improve the feel of the lightweight PCR part, it was partially overmolded with a soft TPE component.”
Allrounder injection molding machines are designed to process virtually all polymers, he said.
“Alongside the quality fluctuations, further challenges when working with recyclates and bioplastics include the process-specific material data and small processing windows,” Stern said. “Inline quality management plays a key role here. By measuring and regulating process parameters such as pressure, feed rate and temperature, the quality of components containing recyclate can be improved considerably.”
Arburg offers its assistance system, 4.monitoring, which monitors the system status and identifies and documents process deviations at an early stage.
Some new materials available for processing include biodegradable plastics, which can be used when the plastic is expected to end up in the environment or the human body. Examples include absorbable implants, compostable organic waste bags and mulch films that can be plowed into the soil after use.
Arburg partnered with the Institute of Plastics and Circular Economy at Leibniz University Hannover in Germany, which is using Allrounders for its research in recycled resins and biomaterials. The institute uses an electric Allrounder 470 A to examine the materials’ processing behavior and to produce test specimens for material analysis, Stern said. It also uses a hydraulic dual-component Allrounder 920 S with combinations of recycled and virgin materials to focus on processes and materials and how they impact product properties.
“The more effectively and homogeneously plastics are separated, the less fluctuation there is between batches,” Stern said. “Arburg is involved in projects where, for example, the sorting equipment is able to detect the plastic — using solutions such as HolyGrail 2.0 technology or fluorescent material markers. Or where products are coded using structures on the tool surface. The HolyGrail 2.0 technology is an innovative solution for homogeneous separation. Digital watermarks are used to store the required information invisibly on a label. This provides the product with a digital passport containing relevant information about recycling. The label is covered with watermarks, which means even a fragment of an [in-mold labeled] tub is enough to call up information about its material and previous use, such as whether or not it is suitable for food.”
The company’s research to develop products to process recycled materials is ongoing.
“One of the areas Arburg is looking at is combining the mechanical properties of the injection molding machine — primarily the injection unit — with software and digitalization,” Stern said. “The new filling assistant for Allrounder machines with the Gestica control system is an example of how component simulation can be integrated into the machine controller. In this case, simulation becomes part of the injection molding process. The machine operator sees how the filling process proceeds under real conditions. Further development work is currently ongoing in this area.”
Wittmann Battenfeld
Wittmann Battenfeld has made changes to its plasticizing unit, its process control equipment and its auxiliary equipment to make processing of newly developed and recycled materials easier for injection molders.
At K 2019, Wittmann Battenfeld partnered with Zeroplast to introduce Zeroplast free, a plastic-free natural material developed for injection molding of cosmetic packaging. It is made of organic and mineral raw materials, Zeroplast said. There are no chemical additives, so it breaks down into its natural components when composted.
“The main requirements to process this are on the injection unit and the process control,” said Wolfgang Roth, Wittmann Battenfeld’s head of applications engineering and exhibitions in Austria. “This new material is processed at much lower temperatures than conventional thermoplastics. For that, new controller algorithms had to be developed for process control. The temperature control on the cylinder was developed as a variant between liquid temperature control and ceramic heater bands.”
Processing recycled materials presents similar challenges, especially if a processor is regrinding sprues and bad parts and feeding the material back into the process, he said. This presents challenges for homogeneity and coloring.
“Screws with special geometries are required for this,” Roth said. “For better mixing, screws with mixing sections or nozzles with mixing elements are designed. To reach a good/better homogeneity of the material, different barrier screw geometries were developed.”
Auxiliary equipment also is needed to process newly developed and recycled materials.
“With Zeroplast free, due to its low melting point this material is processed at lower temperatures,” Roth said. “For the dryer, this means that there must be a possibility to set low pre-drying temperatures, lower than normally used for thermoplastics. For the dryer, a condensate separator is needed. This is to prevent deposits in the molecular sieve, which impair the function of the dryer.”
Regrinding sprues and bad parts creates dust that can impair the injection molding process. A dust collector is needed to avoid feeding too much dust into the dryer, Roth said.
Nissei
As a part of Nissei’s ongoing effort to establish sustainable, zero-waste products and to reduce carbon footprints, the company developed a polylactic acid (PLA) injection molding machine system that it displayed at K 2019. PLA is a biodegradable plastic made from corn and sugar cane. Parts made from PLA can be composted and biodegraded so they can return to nature.
PLA is difficult to process into deep or thin-walled parts in an injection molding machine because it has low heat resistance (approximately 140 degrees Fahrenheit), low shock resistance, poor fluidity and poor mold-release characteristics.
Nissei said it was prompted to develop thin-wall product molding using PLA by a new French law that will require all disposable tableware to be made from 50 percent or more biologically sourced materials that can be composted by 2020. Similar regulations to reduce the petroleum-based content of plastic bags and disposable containers have been enacted in many countries.
The fluidity of PLA is poor, so in standard PLA molding it is customary to have short shots when molding thin-wall parts. This prevents the material from solidifying before the flow paths have been filled.
Working with Michio Komatsu, president of Komatsu and Associates and a PLA molding expert, Nissei developed a new technology to mix supercritical carbon dioxide into molten PLA to improve the fluidity of the injected material. This allowed the company to injection mold an ultra-thin-wall (0.65mm) champagne flute that features very high transparency, which it showed at K 2019. A second Nissei injection molding machine manufactured the stem of the champagne flute out of PLA.
“The only machine modification was on the machine that was making the fluted part,” said Joe Kendzulak, senior technical adviser and instructor at Nissei’s New Jersey Tech Center. “It had a system added on to the barrel to inject the supercritical gas into the melt stream. The gas is introduced to stretch the material and make the thin wall.”
The machine making the stem didn’t need the gas-assist system because the stem had a heavier wall than the champagne flute.
For more information
Arburg Inc., Rocky Hill, Conn., 860-667-6500, www.arburg.com
Wittmann Battenfeld Inc., Torrington, Conn., 860-496-9603, www.wittmann-group.com
Nissei America Inc., Anaheim, Calif., 714-693-3000, www.nisseiamerica.com
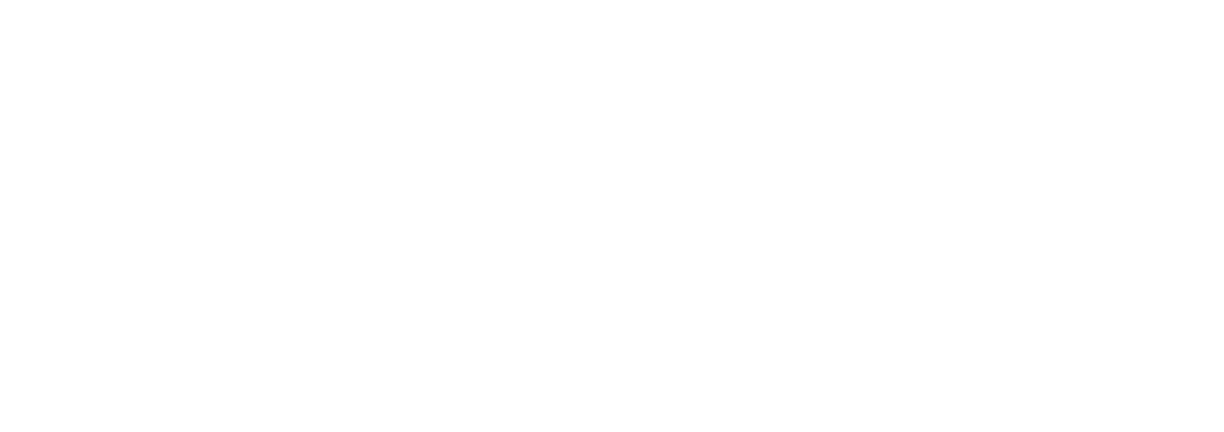