By Bruce Adams
Problem: An injection molder needed to make parts for face shields as quickly as possible to help medical professionals combating the novel coronavirus.
Solution: After the molder scrambled to begin production, its robot OEM designed a program to shave a full second off the cycle time.
The rapid spread of the novel coronavirus across the world has created shortages of much-needed protective gear to keep medical professionals safe as they do their life-saving work. Manufacturers worldwide have retooled to meet the growing demand for face masks, face shields, protective gowns and other critical supplies.
It’s unlikely that many of them moved more quickly than Pragmatic Manufacturing in Brunswick, Ohio, which received a new mold, set it up and was making approved parts in less than 24 hours. The company’s fast response was due to a combination of extreme need in the medical community, effective long-range planning, the close coordination of multiple companies and favorable logistics.
Pragmatic Manufacturing is a 3-year-old injection molding, custom tooling and machining company that also does low-pressure injection of waxes for the investment casting industry.
Earlier this year, Pragmatic purchased two new Wittmann Battenfeld injection molding machine work cells, including two presses, two loaders, two robots, two temperature control units and a chiller.
"When we purchased the equipment, we did not have anything to run,” Klem said. “We got them because we are familiar with the industry and knew the opportunity would come to run products on them. We used to operate as a different company. We are tool makers and tool builders, as well, and knew we would be able to use the equipment eventually.”
That opportunity came sooner than expected, thanks to the global pandemic and the company’s relationship with MTD Products Co., a Grafton, Ohio, power-tool manufacturer with roots in mold making. MTD had been contacted by the Cleveland-based Manufacturing Advocacy and Growth Network (MAGNET) to build a mold that could produce and deliver more than 1 million headbands for face shields in five weeks for health-care workers in Ohio. MAGNET is an organization that provides consulting and design services to manufacturers. One of its projects involves 19 Ohio manufacturers that work with hospitals and the state government to address shortages in the medical industry supply chain.
Klem drove 13 miles out to Grafton to pick up the two-cavity mold at MTD on a Wednesday afternoon, drove back to Pragmatic Manufacturing, and set the mold up on the company’s new SmartPower 121-ton hybrid injection molding machine that evening.
“We picked the tool up Wednesday afternoon, and I was making parts Wednesday evening,” Klem said. “I called the director of MAGNET, and they came out the next morning to approve the parts. We had the press running within 8 hours and had approved parts in less than 24 hours.”
In addition to the press, the work cell includes a W821 robot, Feedmax S3-net loader, Tempro Plus D200 temperature controller and a 5-ton Coolmax chiller. The work cell is operating 24/7 to make headbands as quickly as possible.
After Klem got the line running, he sent a video to Wittmann Battenfeld, which reviewed the video and made some adjustments to speed up the robot’s operation. Wittmann Battenfeld sent an updated software program to Pragmatic, which the company uploaded to the SmartPower molding machine’s B8 control system.
Those changes made a big difference in production.
“They have SmartRemoval technology on the robots, which I wasn't familiar with, so I wasn’t using it,” Klem said. “We made some adjustments with their help. We had to order some more cams for the Y-axis to allow the robot to start coming down as the mold was opening. We got a few parts overnighted to us. They were very helpful. We have had a long history working with them. It is a close relationship. Their technicians have always been very helpful.”
Engaging the robot’s SmartRemoval technology reduced the cycle time by 1 second.
“We now are running a 17-second cycle time. It was 18 seconds when we reached out to them,” Klem said. “In a two-cavity mold, we are making 10,164 parts with a 17-second cycle time in a 24-hour period. At the 18-second cycle time, we were making 9,600 parts in 24 hours. We are making an extra 564 parts a day with that extra second. That adds up because it multiplies daily. This was a great example of remote monitoring and service.”
Pragmatic Manufacturing ships the headbands to toymaker Little Tikes Co., in Hudson, Ohio, which repackages them into face shield kits that it sends to a central Ohio location, where the kits are distributed to hospitals throughout the state.
Pragmatic Manufacturing has a second Wittmann Battenfeld work cell that has all the equipment that it is using to make headbands, except for the chiller. That cell features a SmartPower 265-ton press and a W831 robot. At press time, the company was looking for work for that cell.
Bruce Adams, senior staff reporter
Contact
Pragmatic Manufacturing, Brunswick, Ohio, 330-222-6051, www.pragmaticmanufacturing.com
Wittmann Battenfeld Inc., Torrington, Conn., 860-496-9603, www.wittmann-group.com
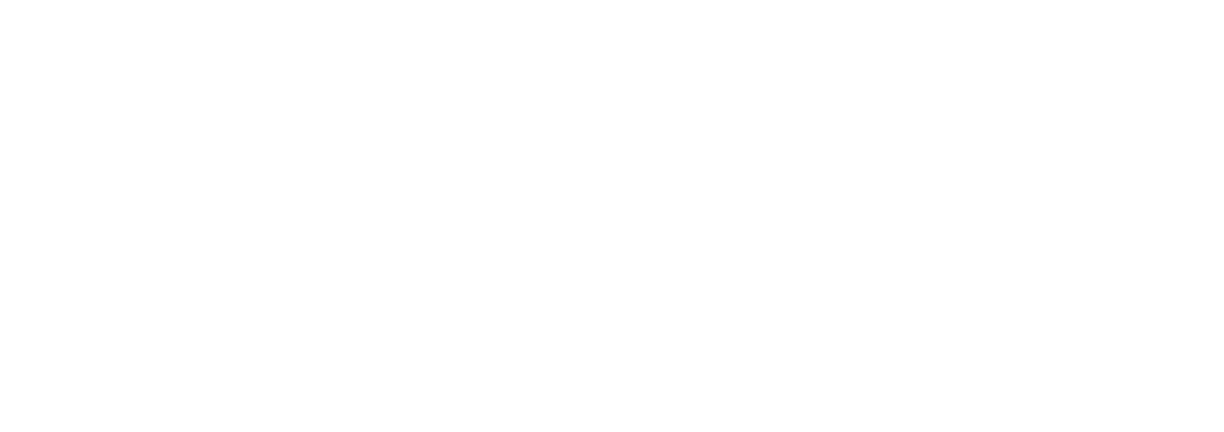