Evolution was on display at K 2019, as OEMs showed off the latest improvements in hydraulic injection molding machines. Based on existing models, new machines and series from Haitian, Bole Machinery and Arburg took steps forward in terms of characteristics such as maintenance requirements and user convenience.
Haitian
Haitian updated its Mars series of servo-hydraulic injection molding machines at K 2019 with the introduction of the Mars III line. Twenty-five models of the new IMMs, with clamping forces ranging from 67 tons to 3,709 tons, will be available in the second half of this year.
The series will replace the Mars II line and include improvements to the injection unit, clamp, servo-hydraulics, the housing’s sheet metal and machine bed, and its controls. It is part of Haitian’s new third-generation technology, which also included updates to the company’s electric and hybrid IMMs.
Haitian's Mars III machines sport a number of upgrades over the Mars II series.Haitian Plastics Machinery Corp.The Mars III’s injection unit features upgraded linear guides that improve acceleration, deceleration and back pressure control; new screw elements and barrel components for more efficient plasticizing; a swiveling injection unit that makes it easier to clean and replace the screw; increased injection speed and injection-unit pressure ranging from 3 percent to 5 percent; and shorter dry cycle times.
Clamp unit improvements include a thicker and stronger platen for more centralized force transmission from the platen to the mold; bigger distance between tie bars to accommodate larger molds; and improved repeatability of the clamp movement. The tie-bar distance increases range from 50mm by 50mm on smaller machines to 100mm by 100mm on some of the larger machines.
An upgraded servo motor controls the hydraulics on the Mars III. It requires less lubrication, for a cleaner process and less maintenance. Hydraulic lines made with new technology that eliminates welding can withstand higher pressures and are less likely to leak, according to Glenn Frohring, president and co-owner of Absolute Haitian, which is the official U.S. and Canadian distributor for China-based Haitian. Improvements in the proportional control-valve technology allow for faster mold opening and closing times and repeatability of up to 0.5mm.
The company reinforced the Mars III machine bed for better rigidity. The machine’s design now includes a frameless door designed to provide easy entry and space for mold changes and robots. Designers also created open space under the machine bed for auxiliaries or conveyors.
“That space used to be blocked off so that a conveyor could only go out of the back end of the machine,” Frohring said. “Now parts can be dropped onto a conveyor that goes out the back end of the machine, the operator side or the non-operator side of the machine. Or both. For example, after a part is made, a camera can be positioned to take a picture. If it’s a good part, it can drop onto a conveyor on the operator side where it can go into a box of good parts. Alternately, if the camera determines it is a bad part, it drops onto the conveyor but travels to the non-operator side of the machine and goes into a box for bad parts.”
Like Haitian’s third-generation electric and hybrid IMMs, the servo-hydraulic Mars III now includes Motion Plus and Connectivity Plus technology. Motion Plus is a combination of hardware and software designed for intelligent motion control, such as the precise movement and adjustment of the clamp or injection unit.
Connectivity Plus is a software feature designed to make the presses compatible with a wide range of automation and interface options, including manufacturing execution systems and all common Euromap interfaces.
The Mars MA1700III/plus on exhibit at K 2019 produced bottle opener handles from 100 percent recycled PP using insert technology. Metal bottle openers were placed in the IMM and plastic was injected over the metal to form the handle. A robot from Haitian Drive Systems was integrated into the production cell.
Bole
Bole introduced several features on its DK series of injection molding machines, which are fully hydraulic two-platen machines with clamping forces ranging from 585 tons to 7,644 tons. Sixteen models are available in the DK series and each one can be equipped with three different screw diameters, according to Alfred Rak, president and CEO of Bole.
Updated DK-series machine features include electrically actuated split tie-bar nuts, tie bars that are made of forged steel, a new screw tooth design on the tie bar and linear guide rails.
“The electrically actuated split tie bar nuts improve cycle times 15 percent to 20 percent compared to other hydraulic machines equipped with a classic closing mechanism,” Rak said. “I am not aware of any other major IMM manufacturers that offer this. It is a unique feature and selling proposition to Bole in the industry.”
Bole's DK series of injection molding machines has been updated to facilitate a smoother operation.Bole Machinery Inc.The tie bars on all DK-series machines are now made of forged steel, which is stronger than the tie bars on previous DK models that were made of machined steel.
“The forged steel tie bar has a 7.5 times safety factor built in to hold the pressure of the IMM,” Rak said. “We are almost guaranteeing that there will be no cracked or broken tie bars.”
In addition to the forged steel, a new screw tooth design on the tie bar contributes to stronger, smoother operations, he said.
“The tie bar now has a progressive screw tooth design for even stress on each of the teeth,” Rak said. “The tie bar has grooves where the tie-bar lock engages. They have a variable tooth spacing for even force application.” Previously, teeth were equally spaced, which did not distribute force as evenly, he said.
“The variable tooth spacing means the force is evenly spread out. The tie bar engages for even force application,” Rak said. “The distance from one groove to the other grooves is not even. The grooves that are further away from the platen [have] a smaller distance, rather than those that are closer. The reason is the stress and the force from the most remote grooves looking from the platen toward the end of the tie bar have to [absorb] a larger stress than those that are closer to the platen. It is patented and unique.”
All the DK machines now use linear guide rails, which offer smoother operation. “The linear guide rails are instead of regular flat steel-on-steel gliding shoes that were not linear,” Rak said.
At K 2019, Bole exhibited an updated 520 DK machine, which made an under-the-hood cover part for the automotive industry. The redesigned DK series is available in North America. Bole plans an open house at its Stow, Ohio, headquarters this summer to showcase machines in the series, including the BL950 DK, which the company is targeting to automotive customers and others with larger molds.
Arburg
Arburg introduced two new hydraulic injection molding machines at K 2019 — the Allrounder 270 S compact and the Allrounder 1600 T vertical rotary table machine.
With a clamping force of 40 tons, the Allrounder 270 S compact is a more compact version of Arburg’s standard Allrounder 270 S. It is the first Arburg press that can be configured and ordered online using the arburgXworld digital sales portal, the company said.
“With the option of ordering machines over the Internet, we are pioneering new ways in our sales organization,” said Gerhard Böhm, managing director of sales at Arburg. “At the same time, the new Allrounder 270 S compact is a continuation of our successful model 221 K, because it offers reliable hydraulic machine technology within the smallest footprint.”
Arburg's Allrounder 1600 T vertical injection molding machine has a clamping force of 225 tons.Arburg GmbHTwo primary requirements of the development of the new machine were to minimize its footprint — it’s 20 percent smaller than the standard Allrounder 270 S — and to make it less expensive through standardization and the use of arburgXworld.
The advantages of standardization, the new price and online sales complement each other. Due to the standardization, the Allrounder 270 S compact can be easily configured and ordered online and shipped promptly, the company said. This standardization of basic equipment, combined with the new online distribution channel, allow the company to offer it to processors for 25 percent less than the standard Allrounder 270 S.
Standard features of the 270 S compact include a fixed combination of the clamping unit and injection unit; an energy-saving servo-hydraulic system with a water-cooled and speed-regulated servo motor; a highly wear-resistant cylinder module; a smart Selogica control offering extensive standard functions; and a clamping unit that is highly compatible with a variety of molds due to the hole patterns in the mounting platens.
The machine’s servo motor operates quietly without creating air turbulence. It also wastes little heat, the company said. The wear-resistant cylinder module can process thermoplastics with highly abrasive or corrosive components.
The 270 S compact exhibited at K 2019 was equipped with a two-cavity mold that produced 2.3-gram electronic terminal strips from polybutylene terephthalate in a 15-second cycle time. The parts and sprues were separated in a sorter.
With the introduction of the Allrounder 1600 T, Arburg is expanding its range of vertical rotary table IMMs to include a 5.2-foot table diameter option.
The Allrounder 1600 T has a clamping force of 225 tons and can be equipped with injection unit sizes ranging from 170 to 800. It was based on the Allrounder 1500 T but offers footprint and weight improvements compared to that machine, the company said.
The new machine has a small footprint, more space for mold installation and a working table height of about 3 feet for ergonomic reasons.
To streamline mold setup, the company revised the routing of hydraulic lines and their connections. It features a standard ergonomic package that includes a combined vertical and horizontal light curtain that protects operators and robot systems from harm.
The rotary tables on T-model machines are powered by servo-electric motors that work independently of the other machine movements. This allows the tables to operate quickly and precisely without any vibrations, the company said.
The Allrounder 1600 T, like other Allrounder T models, features dual-circuit pumps designed to ensure simultaneous movements for the ergonomic overmolding of inserts. The technology can be adapted to process- and mold-specific conditions.
The Allrounder 1600 T at K 2019 was equipped with a four-cavity mold and was overmolding metal bottle openers with PP. A Multilift V 15 linear robot that was integrated into the Selogica control system handled the inserts and removed the finished parts and set them on a conveyor belt. The cycle time was 30 seconds.
Bruce Adams, senior staff reporter
[email protected]
For more information:
Absolute Haitian Corp., Parma, Ohio, 216-452-1000, www.absolutehaitian.com
Arburg Inc., Rocky Hill, Conn., 860-667-6500, www.arburg.com
Bole Machinery Inc., Stow, Ohio, 330-983-4700, www.boleamerica.com
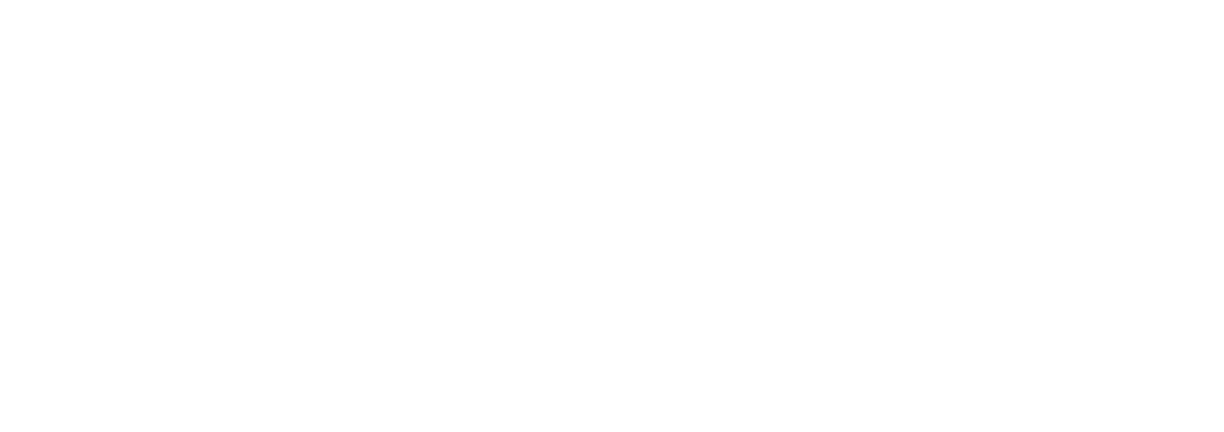