Duane Jebbett walks the factory floor at Rowmark with an eye on process and efficiency improvement. The Findlay, Ohio, company is obsessed with precision plastic sheet extrusion and Jebbett, CEO and president, makes sure that goal is always in sight. "Extrusion is our obsession," reads one wall. Big, bold signs on Rowmark's factory walls remind everyone that what's important here is quality, pure and simple, and attention to detail is how to achieve it.
In-line gauge-control technology uses intelligent beta transmission sensors to measure sheet thickness. Specialized PLC control systems in the line work to provide a stable process. Each line is equipped with a real-time quality data system that reports into a central database. Employees carefully clean and maintain dies and supervise line production for any imperfections.
At the time of PMM's plant visit in late 2014, Rowmark was preparing for its next extrusion line, a custom-designed turnkey system from Welex, York, Pa.
Anatomy of a Turn-Key System
Branded as the Welex Hercules industrial sheet line, the machine features a 4.5-inch main extruder and a 2.5-inch co-extruder, both with double-vented cylinders, to run a wide range of hygroscopic materials including ABS, TPO, acrylic and PC. The line will produce sheet up to 74 inches at a thickness of 0.15 to 0.35 inch. The tooling includes melt pumps, static mixers and Nordson Xaloy hydraulic screen changers for both extruders, which feed a Nordson EDI distribution block and 80-inch dual manifold fast gap die. The 80-inch Welex Evolution sheet take-off features three 24-inch-diameter polishing rolls with high temperature capability and a boosted pneumatic high PLI (pounds per linear inch) roll-closure system. The rolls are individually driven via 5-horsepower AC motors with precise ABB drives, with the middle roll rapid roll change-enabled. The roll gap adjustment is motorized at all four nip points with digital display on a control system, Graham Engineering's XSL Navigator. The take-off features a two-station, double-sided laminating payoff with magnetic particle brake tension control for applying decorative or protective films on one or both sides of the sheet. The line includes tandem sets of pull rolls for precise edge trimming followed by a hump conveyor, Famco power shear, and motorized take-away conveyor. All machine functions are accessed via the Beckhoff industrial PC-based Graham Engineering control system. The system features integrated manuals, recipe management, real-time production monitoring and integrated diagnostics for troubleshooting and maintenance.
Line Review
Officials are moving some lines and re-engineering its existing factory as part of a massive expansion set for completion in spring. A brand new, 85,000-square-foot Rowmark manufacturing facility is under construction just down the street from the company's current location. Recent growth in all divisions now calls for separate facilities. The new building will provide much-needed space to expand the manufacturing and administrative headquarters for the company's signage and engraving materials division, officials said. The new building will include advanced clean rooms to further enhance the quality initiatives for laminated sheet products, a custom R&D lab for more innovative product development initiatives and a showroom for product displays. The company's current facility will be re-engineered for its custom plastic sheet division, Premier Material Concepts (PMC). PMC produces and markets custom sheet and roll stock for the point-of-purchase, sign and thermoforming industries. Backing these expansions is private equity investment firm Bertram Capital, San Mateo, Calif., which purchased Rowmark in 2013.
The changes represent a strategic, carefully planned evolution of a company morphing to meet market demands, say Jebbett and the Rowmark executive team, which includes Eric Short, VP of operations, and Eric Hausserman, VP of PMC products and services management.
"Our new facility will give us new state-of-the-art manufacturing capabilities, which will enhance our ability to grow and to innovate products to meet market demands," says Jebbett. "We want to be the absolute technical experts in our industry."
One of Rowmark's core competencies is lamination. The new facility will give them the ability to house their press capabilities as well as state-of-the-art lamination lines to grow the business. With the capacity expansion, they anticipate that the PMC business will grow rapidly in the current facility.
Of the Findlay plant's current extrusion lines, two will move into the new facility. The remaining lines, including the new Welex, a large co-extrusion line referred to as "The Beast" and the original line that started Rowmark, will remain in the original factory. Of those, one will handle all of the high-volume TPO, said Hausserman.
The speed and efficiency of line changeovers is an important ingredient of efficiency and process improvement, officials said. "The faster and more efficient you are at changeovers, the better," says Short.
The Beast processes the largest widths (up to 120 inches) and single, double or triple layers. Within the last year, the line was equipped with an EDI flat sheet die, purchased at the K 2013 show, that allowed for A/B/A sheet construction. The Beast's first die, also purchased from EDI in 2011, allowed for A/B/C construction, said Hausserman.
The Beast's system components were supplied by Mega Machinery Inc., Riverside, Calif. The technological advantages of the machinery design are many, says Richard Risch, Mega Machinery president. It is equipped with a high-capacity water system for heating or cooling the rolls with three active zones (one per roll) and one stand-by zone so that there is no down time on repairs; pumps with cartridge seals for rapid replacement; and plus or minus 1 degree temperature control. There are individual roll drives and direct mount-on rolls for smooth transmission of power without chatter.
Jebbett and his team have a goal of making it easy for their customers and they are eyeing other markets. The Rowmark business has more growth potential in primary markets such as health care, government, education and hospitality.
Now, Rowmark products are sold into nearly 84 countries but all manufacturing is done on its campus in Findlay. The company has a warehouse in Antwerp, Belgium.
Angie DeRosa, managing editor
Bandera reports cybersecurity incident
The kid from Chicago
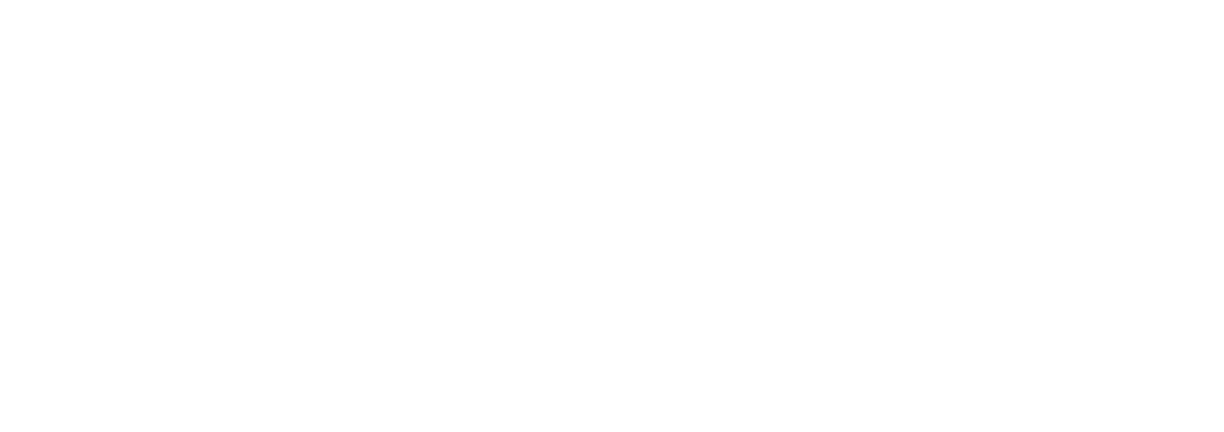