The technologies to spot defects in film, sheet, pipe and tubing are as varied as the problems they identify. With new offerings from companies such as BTG Labs, MoistTech, OneBoxVision and Wintriss Engineering, extrusion professionals have plenty of options when it comes to quality control. Whether it's poor wettability, unwanted specks or unacceptable moisture levels, the problems that extrusion operations face have met their match.
BTG LABS
BTG has begun touting the down-to-earth applications of a technology it originally devised for use by manufacturers of the F-35 stealth fighter plane. At NPE2018, it showed off its Surface Analyst in the booths of two partner companies, Plasmatreat USA Inc., Elgin, Ill., and Enercon GmbH, Bremen, Germany.
Designed to determine bonding potential, the Surface Analyst is a hand-held device that works by calculating the contact angle of water upon any 2-D part. With the device, which has an ink-jet valve, a user deposits a drop of water upon the surface, then an integrated camera snaps an image of the drop, and taking account of its volume and diameter, the device calculates contact angle — providing a direct measurement of surface energy.
It's useful for testing any flat surface that will be painted, printed, coated or sealed, said Emily Leporati, BTG marketing manager. The device can verify whether surfaces treated with flames, plasma or some other method have suitable wettability. "The Surface Analyst is used to determine how much treatment is necessary to avoid overtreatment, which leads to material surface damage … and undertreating, which leads to a poor bond because the surface wasn't activated enough to receive the bond, whether that's laminating two pieces of film together or printing ink onto a film surface," she said.
According to Leporati, the Surface Analyst originally was used to test composite materials before they were laminated to build airplane wings and to inspect the surfaces of metals before they were painted. Over the past year or so, however, BTG has expanded its reach, and in late 2017, the company discovered the technology could be used with plastic films, as well. It works with any flat surface — including sheet.
In addition to aerospace manufacturers, operators of plants that make film and flexible packaging, medical devices, and parts for the automotive, electronics and green-energy industries have adopted the technology. "It has even been used by a manufacturer of vinyl doors and windows to inspect surfaces it was bonding," Leporati said.
Compared to traditional methods, such as dyne-ink tests or goniometer inspection, the Surface Analyst provides faster, more accurate and more reliable results. According to the company, the test takes just 2 seconds. Unlike more common dyne tests, which use a special ink that reacts in various ways depending on surface energy, it uses no dangerous chemicals and requires far less training. It also causes no damage to the product being tested.
In addition to determining whether a surface can be effectively decorated or sealed, the Surface Analyst helps users define optimal surface-treatment levels and monitor production. It can determine how surfaces deteriorate over time, and how long parts can be stored before they become unsuitable for adhesion.
MOISTTECH
MoistTech, which makes moisture-measurement systems for the extrusion, converting and coatings industries, rolled out its latest non-contact moisture meter, the IR-3000C, at NPE2018.
Designed for both film and sheet, the plug-and-play near-infrared system continuously analyzes multiple wavelengths of light to measure moisture content, thickness and temperature. Compared to its predecessor, the IR-3000, the IR-3000C can be more finely tuned.
IR-3000C sensors typically are installed between 4 inches and 16 inches from the extrusion head, and even at high speeds, they can provide real-time feedback that is not hindered by material variations, such as differences in particle size, height or color. Equipped with a suite of high-tech Windows-based programs, the system is compatible with any PC platform and provides user-friendly interfaces for configuration, data logging and diagnostics monitoring. The sensors are calibrated at the factory according to customer specifications and require no maintenance or recalibration once in operation.
The system works with many kinds of materials, including PVC, PP, PE and polyvinyl butyral.
ONEBOXVISION
Ireland-based OneBoxVision has refined its ImageFlow software. Designed for scanning very large areas, it can be used for all kinds of parts, including molded parts and pipe, but CEO Conor O'Neill said it's predominately for film and sheet.
The software compares images of actual parts against design drawings to keep production within parameters. It can identify many types of defects, including gels, specks, fish eyes, holes, oil stains, insects, scratches, coating voids and air bubbles. The latest update, Version 6.7, features a new adaptive algorithm for inspecting the opacity and color of film.
According to the company, real-time feedback on errors can help operators and plant managers minimize downtime, optimize die cleaning processes and identify the best raw materials for their extrusion and converting applications.
"We basically learn what the actual plastic should look like, and we look at variances in the actual plastic," O'Neill said.
OneBoxVision pairs its software with vision-inspection hardware from Acquire Automation, Fishers, Ind. "We scope the hardware based on the operation," O'Neill said. "There are no limitations on how many cameras the software can handle."
WINTRISS ENGINEERING
Wintriss Engineering announced updates to its Web Ranger vision system, which can identify spots, specks, scratches and other surface flaws in film and sheet. Armed with smart cameras, high-intensity lighting and newly upgraded software, the system can even let you know when it's time to call an exterminator.
CTO Ravi Malkani demonstrated the system at the company's NPE2018 booth, using a tiny, simulated roll of film marked with a number of flaws, including pictures of bugs and six-legged squiggles. Not only can the system be programmed to flag the flaws as film is wound across a roller, it also categorizes them. It can provide reports with filters that give operators and plant managers more information about the types of flaws plaguing their product. For example, Malkani showed, his simulation could track insects, misplaced logos and specific flaw shapes, such as squares; the software also can filter based on factors such as flaw size and condition.
According to Malkani, the system can spot defects as small as 10 microns in diameter, though he said typically, customers specify inspections for defects of 0.1mm in diameter or bigger.
He said the software has been upgraded so that operators can simply scan a bar code to indicate the recipe and specifications of the product they're running; that saves time and cuts down on the possibility for human error.
Based on film width and the details and tolerances specified in the reporting functions, Malkani said the system can be tailored to individual users' needs. "Every system is slightly customized. The cameras are the same, the software is the same."
Karen Hanna, copy editor
khanna@plasticsmachinerymagazine.com
Contact:
BTG Labs, St. Bernard, Ohio, 513-469-1800, https://btglabs.com
MoistTech Corp.,
Sarasota, Fla., 941-727-1800,www.moisttech.com
OneBoxVision Ltd.,
Clonmel, Ireland, 353-52-614-6000,www.oneboxvision.com
Wintriss Engineering Corp., San Diego, 858-550-7300, www.weco.com
Karen Hanna | Senior Staff Reporter
Senior Staff Reporter Karen Hanna covers injection molding, molds and tooling, processors, workforce and other topics, and writes features including In Other Words and Problem Solved for Plastics Machinery & Manufacturing, Plastics Recycling and The Journal of Blow Molding. She has more than 15 years of experience in daily and magazine journalism.
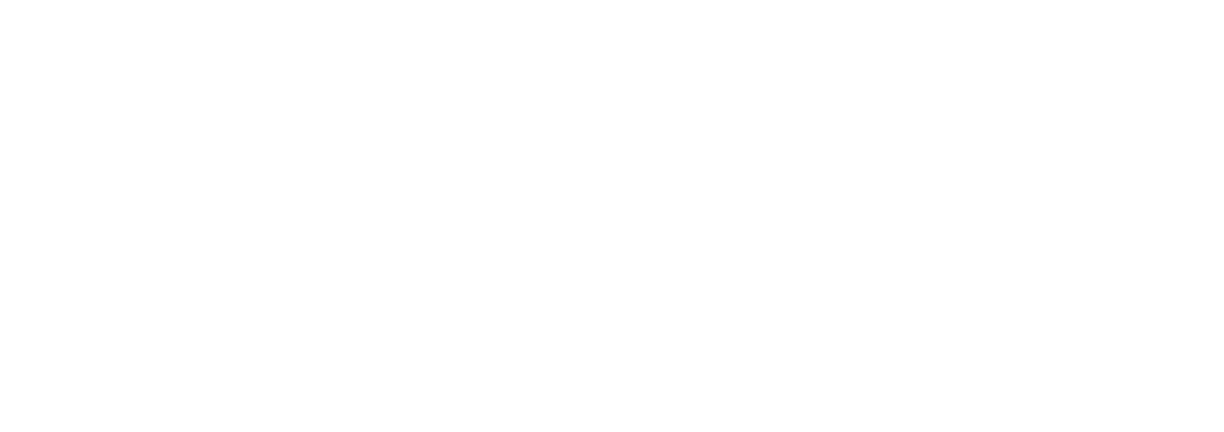