Coperion targets bottle-to-bottle PET recycling
Coperion recently revealed two compounding equipment innovations, one involving PET bottle recycling, and the second relating to a new graphical interface for the ZSK extruder controller.
Bottle-to-bottle recycling
The U.S. Food and Drug Administration has approved a process developed by Coperion for processing PET bottle flakes into pellets without pre-drying the flakes. The method involves processing the flakes into pellets using Coperion ZSK twin-screw extruders. Next, the pellets are processed in a solid-state polycondensation (SSP) reactor, which increases their intrinsic viscosity, and makes them suitable to make bottles with the quality of virgin material, according to the company.
Before recycled PET is pelletized, it must be shredded to flakes and then cleaned. Traditional technologies involve washing, pre-drying and crystallization of the PET flakes. However, Coperion’s process allows shredded PET to go directly into a ZSK twin-screw extruder for compounding.
ZSK extruders’ high torque enables processing at low temperatures and with almost no viscosity loss, the company said. The twin-screw extruders also remove volatile components including monomers, oligomers and water.
Coperion K-Tron high-accuracy Smart Weigh Belt feeders or gravimetric feeders feed the shredded flakes into a ZSK extruder. Other materials, including virgin resin, can be added. Melting, intensive devolatization and complete homogenization take place in the ZSK process section before the melt is transferred via a gear pump and filter with an automatic screen pack changer to a strand or underwater pelletizer for pellet production.
The pellets are condensed in a solid-state polycondensation reactor. The pellets meet the standards of virgin material, and the FDA’s letter of no objection certifies they meet the standards for food-safe plastics and can be processed into bottles again, according to the company.
“With FDA certification, we have officially confirmed the high product quality of the PET recyclates,” Jochen Schofer, Coperion’s business segment manager for recycling and direct extrusion, said in a press release. “With the Coperion solution, we make a technology available to recyclers that is economical and at the same time allows them to make a decisive contribution to the plastic industry’s path toward a circular economy.”
“Thanks to the highly efficient plastification within the ZSK extruder, Coperion systems for this bottle-to-bottle recycling process achieve throughput rates between 2 and 8 tons per hour,” the company said. “Therefore, recycling companies profit from very high product quality, reduced operating and logistic expenses, as well as from energy cost savings up to 30 percent in comparison to conventional PET recycling methods.”
Upgraded ZSK controls easier to use
Separately, Coperion has upgraded the graphical user interface (GUI) on the CSpro control for ZSK extruders to reduce its complexity without limiting functionality.
The redesign results in more-intuitive touch operation, allowing an operator to control the extruder’s functions easily and precisely. The GUI includes new high-contrast icons, and additional information can be accessed at the touch of a finger. The risk of operator error is “markedly reduced,” increasing efficiency, the company said.
“The development and implementation of the new CSpro control interface for our ZSK extruders underwent an extensive analysis phase,” Markus Schmudde, head of R&D for compounding and extrusion at Coperion, said. “We were able to implement everything we learned from that into the new GUI. At the same time, we have set the foundation for more digitization in compounding and extrusion processes going forward.”
An extruder’s status information — including production progress and information regarding orders in process — can be found at the topmost level. Torque and throughput can be regulated quickly and intuitively using slider controls that are ergonomically positioned on the lower display edge.
User-specific registration and simple recipe administration are now integrated into the controls.
The extruder start-up sequence is shown step by step within the GUI. The new CSpro control software automatically adjusts and adapts to any screen size so that the GUI can be used on various devices, including tablets.
The control allows ZSK extruders to seamlessly connect to production monitoring and order management systems, the company said.
Bruce Geiselman, senior staff reporter
Contact:
Coperion Corp., Sewell, N.J., 856-256-3175, www.coperion.com
Bruce Geiselman | Senior Staff Reporter
Senior Staff Reporter Bruce Geiselman covers extrusion, blow molding, additive manufacturing, automation and end markets including automotive and packaging. He also writes features, including In Other Words and Problem Solved, for Plastics Machinery & Manufacturing, Plastics Recycling and The Journal of Blow Molding. He has extensive experience in daily and magazine journalism.
Request More Information
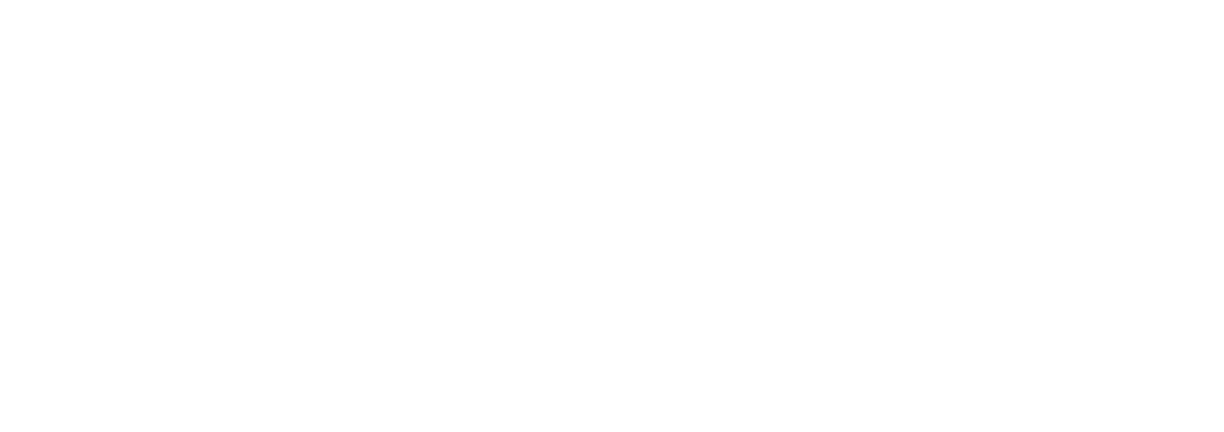