By Ron Shinn
Plastic Recycling Inc. (PRI) has invested $10 million in adding two state-of-the-art extruder systems and upgrading lab equipment, boosting the company's capacity to compound 200 million pounds of recycled resin a year.
The Indianapolis-based company is aiming to increase its business for recycled resin compounds used in the automotive and electronics industries. It recently launched 12 new grades of automotive compounds based on 100 percent recycled resin.
The 35-year-old compounder has carved out a substantial niche developing and marketing compounds using recycled resin. Most of those compounds are made from 100 percent recycled resin, according to Brandon Shaw, second-generation owner of PRI. The company uses post-consumer recycled (PCR) material.
PRI has production facilities in Indianapolis, Jefferson City, Tennessee, and Cowpens, South Carolina. There are 10 compounding lines in Indianapolis, two in Jefferson City and none in Cowpens. Total employment is about 200.
Recycling for the automotive industry in Europe, which uses more recycled plastics in its parts than other regions, has provided a roadmap for PRI. “The goal is to recreate the European mentality around recycling here in the U.S. to satisfy these automakers’ demands for PCR,” Shaw said.
That means PRI must develop technical compounds with high ratios of recycled resin that are consistent from truckload to truckload.
“If you control the resin streams and have systems to control the formulations and the extrusion process, you can make really high-percentage PCR feedstocks to go back into cars or electronics, or even food-grade products,” Shaw said.
The two new machines and pelletizers added to the Indianapolis facility are built by Italian manufacturer Celectric Technology and Delco Extrusion in Sesto Calende. One is a 112mm twin-screw unit and the other is a 200mm single-screw extruder. Total capacity for the two compounding lines is about 60 million pounds.
Each extruder has four attached mixing silos. Two are dedicated to incoming material, and two to the finished compound. Each silo has a one-truckload capacity. Metalmeccanica Rossi Srl in Forli, Italy, made the 35-foot tall, self-cleaning silos with mixing screws.
BHT Srl, based in Modena, Italy, made the three-stage mezzanine, dosing systems and pneumatic conveying equipment.
PRI buys curbside PCR in bales, automotive residue that has been shredded and electronic waste shredded or in bales. Other waste comes in bales, or as purgings or discarded parts.
PRI has a wash line for No. 5 bales of postconsumer polypropylene. It is also believed to be the only compounder in the U.S. accepting mixed electronic waste.
“We put that through different density tanks, shredders, grinders, aspirators, rubber-removal machines and electrostatic separators, so we can get pure PS [polystyrene], pure ABS [acrylonitrile butadiene styrene] and PPE [polyphenylene ether],” Shaw said.
Incoming material is assigned an electronic ID. “We have full traceability of the material that goes into the silos,” COO Marco Meloni said. "That is a key element in developing and repeating specific resin recipes, he said.
Meloni previously ran a recycling and compounding company in France that was one of the largest compounders of polypropylene for the automotive industry. He and Shaw met at a K show and kept in touch over several years, and he joined PRI in 2021 when his company was sold.
The extruders are fed gravimetrically from a mezzanine. “While we are using one silo, we are pneumatically loading the other one,” Meloni said. “We never have to stop the machine, even when we change production, and we always have a homogenous flow.”
Recipes for the extruders come electronically from the lab, and the dosing equipment and extruders are set automatically. Dry components of the recipe are mixed in the silo and liquid components are added at the extruder.
PRI developed a degassing system for the new extruders. Meloni said PRI worked with the extruder manufacturer to develop a devolatization system, continuous filters and pelletizers. Product samples are taken automatically and sent to the lab throughout the production cycle.
Throughput is about 5,500 pounds per hour. The material is mixed for four hours before and four hours after it is compounded.
This allows PRI to use a higher level of recycled resin in its compounds, Meloni said.
“We make a really homogenous blend that we can give to our customers,” Meloni said. The system can output a full truckload of material, or the company can produce material to be loaded into super sacks or other packages.
One person can monitor both highly automated systems.
Meloni said there is very little degradation of the material as it is compounded.
“It is very simple to make standard products with 100 percent recycled resin, but it is very difficult to make technical products 100 percent recycled because you lose properties,” he said. “But with these machines, it is quite easy for us to achieve the properties and go to very high ratios of recycled content for very valuable products.”
PRI designed the entire system and worked with the Italian machinery and equipment manufacturers to put it all together.
“We are a compounder, and our equipment is at the level of the best compounders in the market,” Meloni said.
PRI was founded on the idea of developing compounded products for a specific end product, but the strategy is moving toward developing a range of products OEMs can choose from. That is the same business model virgin resin makers follow.
“We built this range of products that fits the needs of our customers, like the virgin resin makers do,” Meloni said. “We came up with this following the experience we had in Europe. There, we had 22 grades that were motivated by the car makers for exterior, interior, under the hood and so forth, and these can also be used in other applications.
“This has changed our definition of who we are, our image and our position in the marketplace. Up until now, there was a virgin resin maker, a recycler and then a compounder. We need to be in the middle of all those.
“We are a now compounder that uses as material our recycled stream,” he said
The upgraded lab makes this possible, Meloni said. It is the key to turning the waste PRI buys into material it can use in its compounds. A great deal of time and resources go into understanding and preparing the material PRI sends internally to its extrusion department.
“We are able to understand exactly what are the materials we are putting into our recipes, how they behave and the advantages of using them,” he said.
“We sell specifications,” Meloni said. “You cannot order waste based on specifications. You get what you get. We make the specs ourselves. We will do all the testing that is needed to make our spec. We know exactly what we put into a recipe, so, at that point, we are on the same level as the virgin resin compounders.”
Shaw said PRI acquires waste plastic from across the U.S. and sells its compounds in the U.S., Canada, Europe, China and Mexico. “We will probably be looking at South America and Central America soon with some of our automotive compounds,” he said.
General consumer products currently make up about 50 percent of PRI’s markets; followed by automotive parts, with about 20 percent of the portfolio mix; food, 20 percent; and electronics, 10 percent. But Shaw said he expects to grow PRI’s automotive business this year to the point that it makes up about 50 percent of the business.
“A lot of hard work is going to pay off in 2025,” Shaw said. “With our new capacity and new focus, I think 2025 is going to be a pretty good year for us.”
Contact:
Plastic Recycling Inc., Indianapolis, Indiana, 317-780-6100, www.plastic-recycling.net
Ron Shinn | Editor
Editor Ron Shinn is a co-founder of Plastics Machinery & Manufacturing and has been covering the plastics industry for more than 35 years. He leads the editorial team, directs coverage and sets the editorial calendar. He also writes features, including the Talking Points column and On the Factory Floor, and covers recycling and sustainability for PMM and Plastics Recycling.
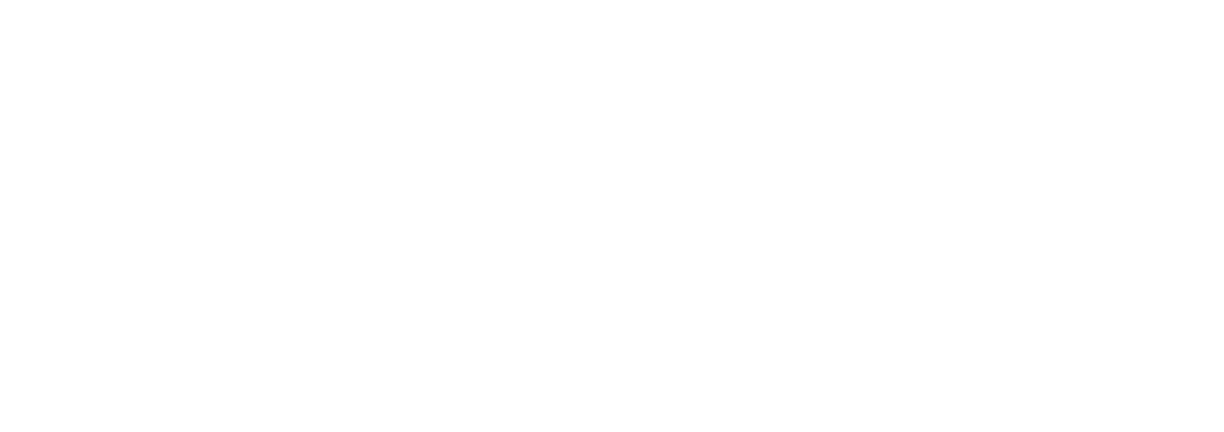