Western Case Inc. (WCI) is a premier manufacturer of blow molded carrying cases that took a big leap and has successfully expanded into blow molding large industrial parts.
In the past seven years, the company has doubled its number of manufacturing lines and added an impressive portfolio of business beyond its core product. It has also demonstrated that it is possible to grow a manufacturing business in California.
“We were an expert at cases,” said Jennifer Clark, operations manager, who joined the company in 2013, just after it moved from a 20,000-square-foot plant in Tustin, Calif., to the current location in Riverside, which is nearly three times as big. “We doubled our machines from six to 12. There was not a whole lot of experience on the industrial side. Nobody here had really done it.
“There were a couple years of growing pains in terms of being able to process with these gigantic machines,” she said. “But we got it under our belts and have been relatively successful.”
WCI was founded in 1978 by Martin Smetter, who ran the business until it was sold in 2012 to the current owners, who do not want to be named. Mario Robles is the president.
The company continues to use AirForm continuous-extrusion machines with small shot sizes — generally under 4 pounds — for its wide range of custom and stock carrying cases, which it refers to as its legacy business. The cases are for power tools, field equipment, musical instruments and the like.
To expand into industrial products, it added accumulator-head blow molding machines from Waldron-Hartig, Sterling, Impco and Cincinnati, ranging from a 6-pound shot size up to a dual-head 35-pound model that gives WCI the potential for a 70-pound shot.
WCI says the dual-head 35-pound Cincinnati unit is one of the largest blow molding machines on the West Coast.
Making a large blow molded part “requires a specific machine, specific head tooling and specific processing,” Clark said. “Not a lot of blow molders have that capability, particularly on the West Coast, because it costs a lot of money to do business here. We can do it.”
Clark said molding large industrial parts takes experience. “You can learn what you learn and then when you are really hands-on is where you gain your tribal knowledge,” she said. “This type of blow molding takes a lot of years.”
She said being in Southern California means high costs for labor, workers’ compensation insurance, freight and utilities.
Nick Fortunato, WCI’s quality engineering manager, is also responsible for cost improvement and cost reduction. “Once we have a process we can run, we study it and determine how we can do it more efficiently to reduce our cost for the customer. This is a continuous-improvement system in-house, as well.”
WCI makes a variety of industrial products, including orange-and-white traffic delineators, traffic and construction safety barriers, spa steps, floating solar panel bases, medical labware, food and beverage containers, automotive and household parts, underground cable housings, telecom boxes, toys and sporting goods.
“We still run our cases,” Clark said. “We specialize in cases. We run cases with interior molds and with logos and in different colors.”
The plant runs 24 hours a day, five days a week. The workforce ranges from 50 to 60 employees.
“I think we’ve done a good job of leaning that [employment] out because we have gotten better at what we are doing,” she said. “We learned to do more with less.”
WCI acquired most of the processing machinery it uses for industrial products from another California company that went out of business.
“We bought the machinery with the understanding that we would have to find projects to run on it,” Clark said. “Typically, you have something to run, then buy the machine. But we did the opposite because the equipment was available, and we had the footprint for it.”
An example of WCI’s work is the SolarTub, a project that won a prize at the SPE’s 2019 Blow Molding Conference. WCI manufactured the floating tub for a high-tech start-up company in California. Injection molded stanchions are added to the tub to support a solar array, and multiple solar arrays can be connected to form a floating solar farm.
“That project was well-managed and a lot of front-end engineering and collaboration with the customer went into that project,” Fortunato said. “There were a lot of changes made in the design steps. When it went to the tool builder, there was not a whole lot more that had to be done there.
“When the mold came back to us to do sampling, we had parts that were pretty much ready within a half-dozen shots,” he said. Shot size for the part is 24 pounds.
An improved version, designed to withstand winds up to 100 mph, is scheduled to go into production this summer.
Another award-winning project for WCI was a 6.5-gallon container used for brewing beer at home. It was a first-place winner at the SPE conference in 2018. WCI was involved in the design and engineering, material specification, engineering development and blow molding the container.
WCI has older processing machines from a variety of manufacturers but refurbishes and updates them continuously. “If you refurbish those machines periodically, upgrade the controls and other things, they really should run for a long time,” Fortunato said. “Our in-house maintenance people are geniuses.”
Machine controls have been upgraded with new Maco systems. “They make our process more efficient and allow us to do some things like exhausting and flushing that could not be done with older control systems,” Clark said. “They also have really good tech support.”
Clark said the mix of machinery gives WCI an advantage over its competition.
“It’s the size, or capacity of our equipment that gives us an edge,” she said. “Not a lot of companies can run the size of industrial parts that we can run. We also have dual heads and dual extruders, which gives us the capability to run more than one part. It makes costing more competitive.
“On a machine with dual heads and dual extruders, I can run two colors at once if I want to, which is not a capability most industrial blow molders have,” Clark said. “We have that capability and we have done it. The size of our machinery and the ability to customize sets us apart.”
WCI outsources its mold building primarily to two shops in Iowa, Midwest Mold Builders Inc. in Waverly, and Hawkeye Preferred Tooling Group in Charles City.
“Both are really good with big molds,” Fortunato said. “If they build it, we know we are getting a mold that is probably ready to run.” Hawkeye Preferred Tooling has a blow molding machine to test its molds before they are shipped to WCI. “I can’t tell you how valuable that is to us,” Fortunato said.
WCI has three resin silos with 90,000 pounds capacity each and uses one for LDPE, one for HDPE and the third for ultra-high-molecular-weight HDPE. Resin is delivered from the rail yard by trucks.
From the silos, a vacuum system moves resin to the blow molding machines. Four-compartment blenders at each blow molding machine are from Maguire Products. “We use one compartment for regrind resin, one for virgin resin, one for color and the fourth for additives when needed,” Fortunato said.
Resin going through the blow molding machine is measured. “We know what our resin usage is per day, per week or even per hour,” Fortunato said. “We are tracking it all the way through the system.”
Because it is located on the West Coast, far from where resin is manufactured, WCI is required to buy 200,000 pounds of resin at a time. “The manufacturers yard it for us and we only have 90 days to use it,” Clark said. “But we are not always in control of how sales fluctuate, so if we go into a slow period and there is 200,000 pounds of resin sitting in the yard, we have to act quickly.”
WCI recently installed camera-based data collection systems on its two biggest blow molding machines. Once the new system is dialed in, it will be able to capture video of the operators and machine, plus related AI software will capture machine conditions. Fortunato said the system, a rarity in industrial blow molding plants, will collect data to help with training operators as well as lowering overall operational cost.
“The value of this is tremendous,” Fortunato said. “We are using the latest technology to improve our process.”
WCI has one shredder and several granulators. The most recent acquisition was a granulator from Zerma Machinery & Recycling Technology. Others are from Conair. WCI reuses some of its own regrind but most is sold to a scrap resin dealer. It does not use post-consumer material.
Two products — traffic delineators and spa steps — run all five days a week. Most other jobs average about 5,000 units per run. A 5,000-unit run can take five to eight business days, depending on the size of the parts.
“Right now, we are running a medical bottle with a 24,000-unit run, but cycle time is 90 seconds to 120 seconds, so that is a lot of machine time,” Clark said.
Short runs and long cycle times mean there is not much automation at WCI. The spa steps, which run on the large Cincinnati blow molding machine, have a 180-second cycle time. Two operators on the machine have plenty of time to remove the part, manually trim flash and box the product for shipment to the customer.
A quality control inspector on each shift walks the plant floor checking products as they come out of the blow molding machines.
A variety of final assembly tasks are also performed, such as adding handles, latches and drilling holes. The company sends screen printing jobs to a nearby vendor.
WCI maintains about 150 molds and there are five to 10 mold changes a week in the plant, which can take up to 12 hours for a large mold.
Fortunato is working with iD Additives Inc. to test using endothermic blowing agents to improve production costs for its traffic delineators. Clark said WCI also uses iD Additives’ Eco-Pro 360 product to clean molds and mold water channels and to prevent rust.
WCI is a private company and does not release sales figures, but Fortunato and Clark characterized WCI as a medium-sized industrial blow molder.
Ron Shinn, editor
rshinn@plasticsmachinerymagazine.com
Just the facts:
Company: Western Case Inc.
Location: Riverside, Calif.
Primary business: Blow molded carrying cases and various industrial products
Plant size: 58,000 square feet
Employees: 50-60
Blow molding machines: 12
Ron Shinn | Editor
Editor Ron Shinn is a co-founder of Plastics Machinery & Manufacturing and has been covering the plastics industry for more than 35 years. He leads the editorial team, directs coverage and sets the editorial calendar. He also writes features, including the Talking Points column and On the Factory Floor, and covers recycling and sustainability for PMM and Plastics Recycling.
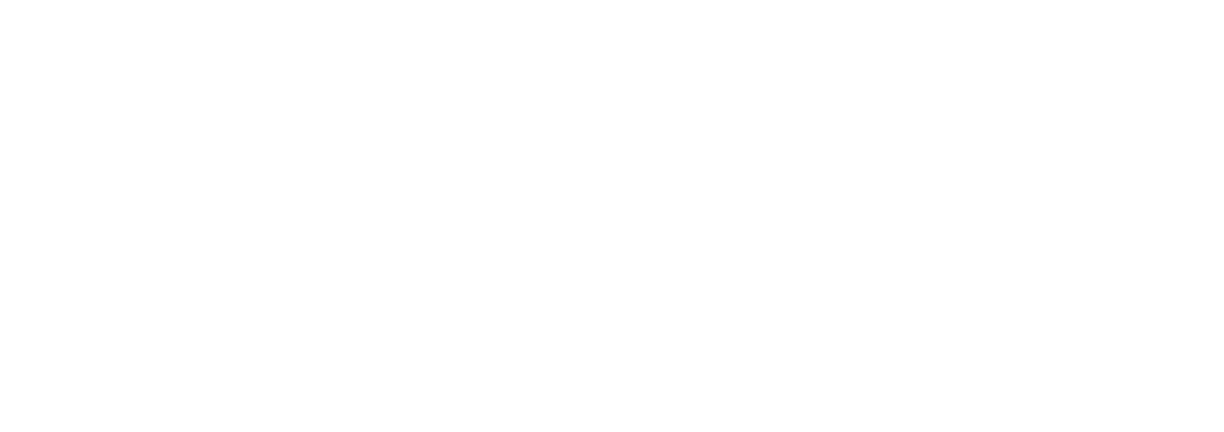