Special Report: Monitoring technologies enhance extrusion film lines
Extrusion machinery maker Windmöller & Hölscher KG introduced a new monitoring system for its Filmex II cast film line that for the first time allows processors to integrate data from the extruder and downstream film-handling equipment.
W&H MONITORING SYSTEM INTEGRATES PRODUCTION/DOWNSTREAM DATA
The company's new Film Performance Monitor (FPM) measures, collects and models process-related data from all equipment involved in the production of cast films manufactured on its Filmex II extrusion lines.
Previously, process information collected from the cast film line during production was separate from data produced by downstream equipment. The integration of production and downstream equipment data provides greater insight regarding film quality, according to the company.
FPM lets processors tailor properties of a cast film or cast stretch film for a specific application. FPM provides 100 percent traceability, since information from the entire process chain is visible, according to W&H.
The use of film-monitoring equipment during production, such as FPM, is especially critical for end users in certain industries, such as shipping. Cast PP stretch films are commonly used to secure cargo, and so it is imperative that they be reliable and strong. According to a study cited by W&H, improperly secured truckloads have been blamed for traffic accidents, injuries and even deaths.
Data collected by FPM through the Filmex II line can be linked through a cloud-based server to data from a film-testing lab or downstream equipment. Machine operators can optimize their process by evaluating data relating to the performance of the equipment.
The FPM system generates a code containing a comprehensive set of production parameters relevant to the properties of the film roll produced. The code is attached to each film roll. End users can scan the code to determine the properties of the film. Properties recorded for one film roll can be achieved by duplicating the process parameters that led to that roll's production.
Data collected by the FPM are available immediately, unlike results from a lab test, which can take several hours. Information from both sources can be used for product development and process setup, and to establish appropriate parameters for film production, according to W&H. The company says it currently has three pilot projects using Filmex II cast film lines with FPM, at customer facilities in North America, Europe and Asia.
FACTS ADDS OPTICAL WEB GAUGE SYSTEM
Factory Automation, Controls & Technical Services (FACTS) has broadened its product line of noncontact, non-nuclear measurement gauges for extruded film by re-introducing an optical measurement system that monitors multilayer films.
FACTS, which offers a portfolio of control systems, information-management systems, and measurement and monitoring products, re-introduced its CFT gauge for measurement of coatings and multilayer film thicknesses, GM Scott Hall said. The CFT uses reflections from infrared light to measure certain translucent, transparent and colored materials, Hall said.
The CFT gauge, originally developed around 2010, was mothballed with the U.S. and global economies in recession. "It was an expensive, highly accurate measurement technology that did not gain traction due to the slowing economy. We have re-engineered the system, including the sensor probe and scanning system, so this is a new-generation unit," Hall said. FACTS exhibited the CFT gauge at the MD&M West show in February in Anaheim, Calif. Since it was last made available, the probe is now less expensive and more precise.
The gauge, designed to scan multilayer or coated films with thicknesses from 12 microns to 16mm, operates on the principle of interferometry, evaluating the interaction of light reflected from materials with different indices of refraction.
The system consists of a probe that is placed over the target material and shines a high-intensity infrared light onto and through the film, Hall said. As the light encounters a layer of material, it is reflected back to the probe assembly. The probe transmits information about the reflected light to a control module, where its characteristics are analyzed. Ultimately, the thickness of each layer and the total thickness of the film are precisely calculated, Hall said.
The CFT gauge can be operated as a profile scanning system for use with film webs with a width up to 120 inches, where it provides measurement of the film's cross-direction profile and machine-direction thickness. In this setup, the probe is mounted to a scanning frame, moving in a linear fashion above the web. The CFT gauge can also be used as a fixed-point system, where it measures the thickness of the film in the machine direction, Hall said.
The monitoring device can be integrated into the company's Total Profile Control (TPC) console to control product thickness based on scanner measurements. The latest TPC, the TPC 5001, is a menu-driven, touch-screen system that provides a high-resolution display of scan profiles. Users can save and recall select profile and trend plots. The TPCs can be supplied with consoles and scanning frames. Automatic Profile Control, software controls that provide automatic adjustments based on measurements, is also available with the TPC units on extrusion lines equipped with an auto extrusion die.
The CFT gauge joins FACTS' laser-triangulation measurement C-frame gauge and its shadow micrometer eddy gauge, which were rolled out in 2015 and measure the total thickness of a sheet or film.
Last year, FACTS also introduced an extruder-controller package designed for film, sheet, tubing or profile extruders looking to upgrade a simple extrusion line with a higher level of control, said Tim Fisher, the owner of FACTS. The package is designed, Fisher said, "for converters looking to upgrade from the use of push-button and discrete controllers to a more integrated extrusion monitoring and control system with recipe-based functions and alarm capability."
Commander is a complete monitoring and control system configured specifically for single-screw extruders.
It can support up to eight temperature zones in the extruder and eight tooling and die zones, and control the extruder speed and the speed of one downstream piece of equipment, such as a puller or vacuum tank. Users can monitor three pressure transducers and two auxiliary points, with an option to monitor heater currents with another transducer. It comes with a 15-inch touch screen.
The system is designed to be economical yet flexible enough so that users can designate and name barrel or tooling zones.
Mikell Knights, senior staff reporter
mknights@plasticsmachinerymagazine.com
For more information
Factory Automation, Controls & Technical Services Inc.,Cuyahoga Falls, Ohio, 330-928-2332, www.facts-inc.com
Windmoeller & Hoelscher Corp.,Lincoln, R.I., 401-333-2770, www.whcorp.com
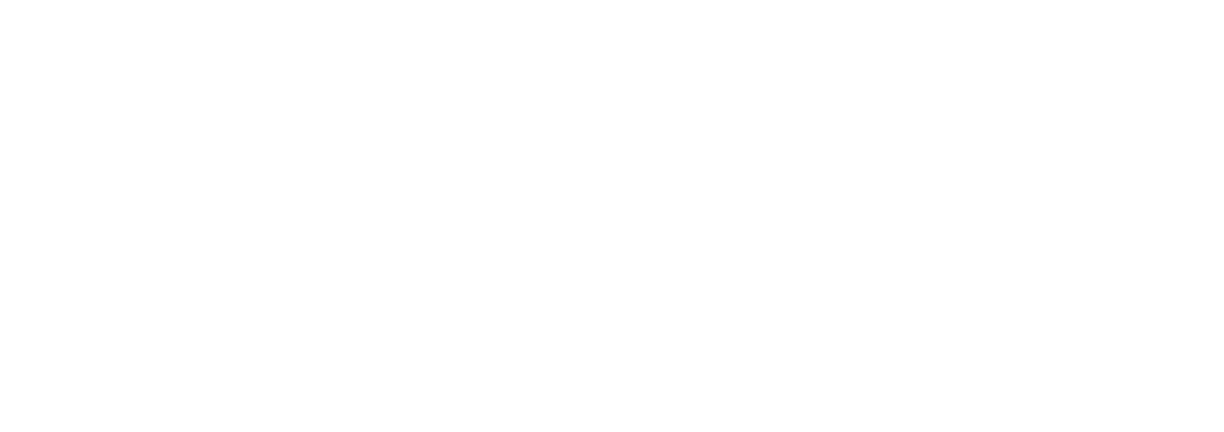