Special Report: Technology broadens for mold temperature control units
Over the past year, equipment manufacturers have continued to improve their temperature control units (TCUs) for injection molds, increasing efficiency and temperature ranges, adding new features and, in some cases, making the equipment more affordable.
Advantage Engineering Inc.
Advantage Engineering Inc., Greenwood, Ind., recently upgraded certain sizes within its Sentra family of TCUs with its new G300 and T300 series controllers.
Water TCUs circulate water through the injection molding process for temperature control. The temperature control range for both the G300 and T300 series controllers is 30 degrees Fahrenheit to 300 degrees Fahrenheit, but they have different microprocessors. The G300 has an LCD display and simple five-button navigation, while the T300 has a color touch-screen operator interface.
The standard G and T series controls, introduced within the past year, have a fluid temperature limit of 250 degrees Fahrenheit. The higher temperature range of the new G300 and T300 controllers makes it possible to work with plastic materials that need to be processed at higher temperatures. However, in order to handle 300-degree fluid, some components on the machine have to be upgraded, which costs more, so it doesn't necessarily make sense for all units to be made in this way, company President Jon Gunderson said.
The G300 and T300 series controllers are used on the company's Sentra TCUs with pump sizes from 0.75 to 7.5 horsepower (hp)and pump flow rates from 35 to 100 gallons per minute. Sentra models can be made with heater capacities ranging from 10 to 34 kilowatts (kW).
Early this year, Advantage also upgraded the Temptender color touch-screen microprocessor control for its Sentra line to include the Euromap 66 communication protocol in addition to SPI, CAMAC, Modbus RTU and TCP/IP, which were available previously.
Sentra units can share valuable processing information, including temperature, flow and alarm conditions, with primary processing equipment.
Advantage also recently introduced the G and T series controls for its Regal Oil Unit, which uses a special-purpose heat-transfer fluid. Able to circulate fluids at temperatures up to 500 degrees Fahrenheit, the Regal Oil Unit is offered with heaters from 12 to 48 kW and pumps from 1 to 7.5 hp.
Oil TCUs are used when higher processing temperatures are required, typically 100 degrees to 500 degrees Fahrenheit. Water is a better heat-transfer fluid, however, so oil generally isn't used unless temperatures hotter than 250 degrees Fahrenheit are needed.
Mokon
Mokon, Buffalo, N.Y., redesigned its Full Range temperature control system earlier this year based on feedback from customers wishing to conserve space, said Robert Kennery, the company's VP of sales and marketing.
"The newly re-engineered Full Range system was designed with our customers in mind," Kennery said. "The reduction in cabinet size frees up valuable floor space for our customers."
Mokon made the machines more compact, so they're now taller than they are wide. Dimensions depend on the capacity of the unit.
The Full Range temperature control system combines a circulating water system and anIceman chiller to provide heating and chilling from a single compact, self-supporting unit.
The Full Range system is available in standard heating capacities up to 96 kW, pumping capacities up to 120 gallons per minute, chilling capacities up to 40 tons and a temperature range of minus 20 degrees Fahrenheit to 300 degrees Fahrenheit.
The Full Range temperature control system's standard features include:
• Stainless steel centrifugal pumps,
• Highly efficient brazed plate evaporator,
• Insulated nonferrous plumbing and components,
• Microprocessor-based controller with LED readout,
• NEMA-rated electrical enclosure with safety disconnect switch, and
• Heater canister with stainless steel diverter.
Additional optional features include stainless steel construction, higher and lower operating temperatures, larger heating and chilling capacities, and stationary skid-based assemblies.
Universal Dynamics
Universal Dynamics Inc., of Woodbridge, Va. — the U.S. arm of the Piovan Group, Santa Maria di Sala, Italy — is introducing its line of Aquatech DigitempEvo thermochiller/TCUs to U.S. injection molders. Aquatech is a company of Piovan Group.
Piovan no longer differentiates between TCUs and chillers, said Giorgio Santella, the chief marketing officer for Piovan. "When it comes to injection molding of plastic parts with high performance, the solution we always offer is the DigitempEvo," he said. "It's a combination of the two."
Unlike other TCUs, the DigitempEvo does not require a chilled water source. The DigitempEvo has an internal cooling source, which means injection molders need only pipe dry-cooler or tower water into the DigitempEvo. The unit then chills the fluid, if necessary, to the exact temperature needed to cool the mold.
The Aquatech system saves energy by chilling the water only by the amount necessary to maintain the proper mold temperature, Santella said. In addition, since each DigitempEvo cools one mold, it eliminates the need for insulated piping to be run through an entire manufacturing plant. In a conventional scenario, a processor could have each injection molding machine equipped with one or more TCUs (depending on the size of the part that is being molded) along with a central chiller water system.
Precise flow rate and temperature and pressure control are necessary when a manufacturer needs to produce parts with high performance standards. It's suited for technical applications in such fields as the automotive and medical industries.
The DigitempEvo is available in five models with single- and dual-circuit versions of each. Designed especially for injection and blow molding machines, these units supply water at a precisely controlled temperature, pressure and flow rate, performing the dual function of heating and cooling. The working temperature range is from 40 degrees Fahrenheit to 195 degrees Fahrenheit.
The units use Copeland digital scroll compressors, which reduce energy consumption while offering exceptional performance. In addition, the use of an electronic expansion valve, included in the standard configuration, further enhances energy efficiency and temperature control.
Overall, energy savings should range from 30 percent to 50 percent compared to equivalent models already on the market, according to the company.
The DigitempEvo uses refrigerant gas R410a, which does not contribute to ozone depletion.
Matsui America Inc.
Beginning in January, Matsui America Inc. will offer a new MC5 mold temperature controller. The MC5 is a complete redesign of the Hanover Park, Ill., company's MC models.
With a new controller and bright LCD display, the MC5 panel can easily be read from a distance or in bright environments, according to the company.
"Improvements in accuracy along with a host of added features make the MC5 a great value," Matsui America GM Greg Lewis said.
Smaller and lighter than the models it replaces, the MC5 increases performance and improves accuracy, Lewis said. The MC5 produces more flow while dramatically reducing heat-up times, thanks to heaters that are larger than the current MC series.
"While Matsui temperature controllers are known for trouble-free operation and a long service life, the MC5 raises the bar in these areas, too," Lewis said.
The MC5 initially will be available in three sizes and two temperature ranges.
Thermal Care Inc.
Niles, Ill.-based Thermal Care Inc. recently released a new mold temperature controller: the RQE Series Basic. It comes with a user-friendly interface for simple operation and was designed for applications that don't require the additional features and options available on other RQE Series units.
The controller features buttons, a clear LCD display and adjustable tuning parameters for uniform temperature control, regardless of external loading. Features also include temperature readouts that can easily be switched from Fahrenheit to Celsius. The TCUs can maintain consistent temperatures with accuracy of within 1 degree Fahrenheit.
The units have pumps that can provide up to 70 percent more flow than similar pumps, twin tank assemblies and Incoloy-sheathed, 12 kW heaters. They are available in 0.75-hp and 2-hp versions and come with a three-year warranty.
Conair Group
Conair, Cranberry Township, Pa., has upgraded its TW-S TCUs with a new user interface that features indicator lights and plain text information, rather than coded readouts, to convey critical operating information. Until now, this control interface was available only on the premium TW-P temperature controls.
The microprocessor controls maintain a uniform temperature regardless of external loading. Built-in features include a counter that tracks the running hours of the pump, temperature-deviation alarms and warnings, adjustable alarm-delay times and error diagnostics.
Both the TW-S and TW-P models are available with optional remote communication capability that allows users to change settings.
The new TCUs — including the TW-V "value" model, which comes preconfigured with just two pump sizes and no options — were first introduced a year ago and have a higher maximum water temperature than previous generations. They feature an innovative pump design that has been shown to reduce energy costs by almost $750 per year.
As an option, TCUs are available that can achieve leaving-water temperatures of 300 degrees Fahrenheit, allowing users to achieve higher mold temperatures without using oil as the heat-transfer medium.
Frigel North America
Frigel North America Inc., East Dundee, Ill., is introducing advanced control technology to its Microgel machine-side chiller/TCUs.
The 3PR control technology for the Microgel units was introduced last month at K 2016. Frigel first implemented its 3PR technology in 2015 on its Ecodry closed-loop adiabatic central cooling system. Based on customer feedback, as well as a growing need for seamless internet connectivity, Frigel decided to extend the control platform to its Microgel line.
The advanced control technology provides more information than previously was available in a portable chiller, and it provides Wi-Fi and Ethernet connectivity.
"The big advantage is the amount of detail it conveys to the customer compared to even our [own] control system or other control systems," said Al Fosco, Frigel North America's global marketing manager. "There are separate screens giving customers information on everything going on in that chiller."
Customers can use the screens to see information including temperatures, pressures, flow rates, energy use, onboard maintenance suggestions and onboard troubleshooting.
"What is unique is the Ethernet connectivity. A customer can connect these units to a plant management system and see this information on their central system," Fosco said.
The company also plans to introduce a Wi-Fi app in the future so customers can see what is going on with the units, even while away from the machines.
"In addition, our service people can tie into these units and troubleshoot them remotely from our offices," Fosco said.
Also among the key features of the control technology is a 7-inch full-color touch screen. Users can view, control and optimize all aspects of their equipment based on real-time data. The information is displayed in the user's language of choice.
ACS Group
ACS Group, headquartered in New Berlin, Wis., is introducing TCUs with stainless steel cabinets that can be washed down. The equipment is being marketed in part to the food and pharmaceutical industries, where companies have installed their own injection molding machines for manufacturing bottles, product manager Tim Hallett said.
"Some heavy plastics users have decided to bring injection molding equipment into their existing facilities," he said.
The units are being sold under both the AEC and Sterling brands. They feature washdown-rated pumps and an electrical enclosure that protects them from water when they are being cleaned. They come standard on casters, but optional sanitary legs or nonmarking casters are available. The stainless steel units are available in a variety of configurations.
The water temperature operating range is from 32 degrees Fahrenheit to 250 degrees Fahrenheit, with 9-kW to 48-kW heaters as options. Easy-access side panels allow for rapid maintenance.
ACS Group also is introducing a new high-kW TCU in an upright design. It offers heater options of up to 150 kW and pump selections up to 240 gallons per minute. Lower-watt-density heaters, which reduce the breakdown of glycol, are also available.
Bruce Geiselman, correspondent
bgeiselman@plasticsmachinerymagazine.com
Contract:
ACS Group, 262-641-8600, www.acscorporate.com
Advantage Engineering Inc., 317-887-0729, www.advantageengineering.com
Conair Group, 724-584-5500, www.conairgroup.com
Frigel North America, 847-540-0160, www.frigel.com
Matsui America Inc., 847-290-9680, www.matsuiamerica.com
Mokon, 716-876-9951, www.mokon.com
Thermal Care Inc., 847-966-2260, www.thermalcare.com
Universal Dynamics Inc., 703-490-7000, http://unadyn.piovan.com
Bruce Geiselman | Senior Staff Reporter
Senior Staff Reporter Bruce Geiselman covers extrusion, blow molding, additive manufacturing, automation and end markets including automotive and packaging. He also writes features, including In Other Words and Problem Solved, for Plastics Machinery & Manufacturing, Plastics Recycling and The Journal of Blow Molding. He has extensive experience in daily and magazine journalism.
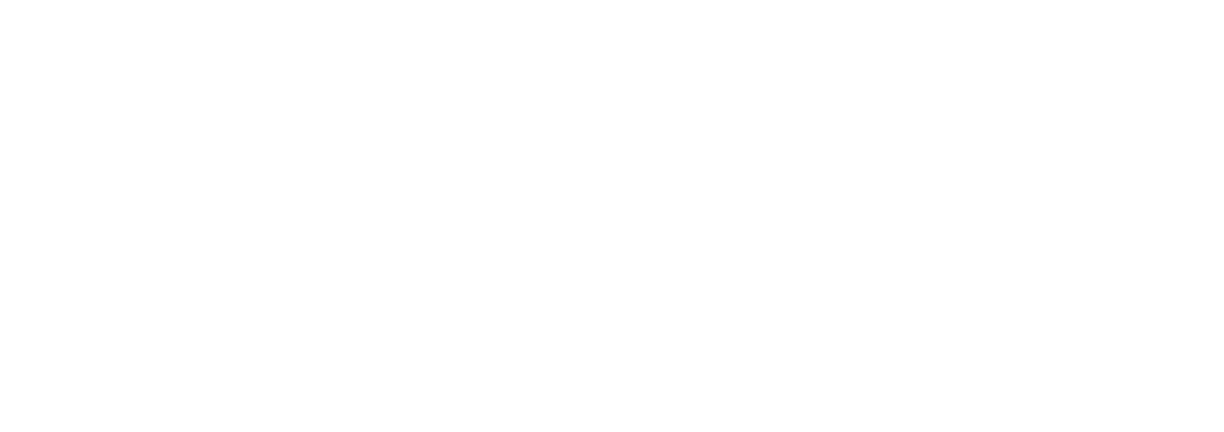