Listen to this article
By Ron Shinn
Is the 3D printing market slowing down?
Well, yes, strictly speaking.
A new report by British consulting firm IDTechEx says that frequent changes in interest rates by governments around the world trying to ease inflation resulted in many 3D printing processors delaying purchases of new equipment until interest rates lowered again or stabilized.
This was especially true in Europe, a key region for 3D printing, according to IDTechEx.
This slowdown in sales caused some materials and printer manufacturers to leave the market in 2024. BASF sold its additive manufacturing business, which was renamed Forward AM Technologies, to managers. Forward AM later filed for insolvency in German court. BASF was the last major chemical company with a significant additive manufacturing business.
Other 3D printing materials makers exited the business recently in France and Brazil. Several printer makers have reported quarterly losses during the past three years.
Among equipment manufacturers, Sintratec ceased building its desktop SLS 3D printers. The Swiss company had been in business for 10 years.
It was not all gloom and doom for the 3D printing industry in 2024, and IDTechEX predicts reshoring and U.S. tariffs will help the industry in 2025. It also expects inflation to stabilize.
We may look back at 2024 as a turning point in the 3D printing industry. Big players continue to embrace the process for intricate parts. BMW Group announced in January that it would start producing a 3D printed center console carrier in 2027.
This would be one of the largest 3D printed plastic components in any vehicle, measuring 11.8 inches by 11.8 inches by 39.4 inches and weighing 8.8 pounds. The single 3D printed component will replace a seven-part assembly and integrate two air ducts that previously required separate tooling-based molding processes. It will be 30 percent lighter than the current console carrier.
Each component requires about 3 hours and 40 minutes to print and the material contains 40 percent recycled carbon fiber and renewable raw materials.
BMW is using large-scale 3D printers and single-screw extruders from Germany’s Hans Weber Maschinenfabrik. The company describes the systems as being robot-based and says only minimal machining is needed to finish the part.
There has long been a belief that 3D printing is too slow for mass production, but continued improvements in 3D printing technology, important labor savings and sustainability considerations have now come into play. BMW announced it plans to produce 18,000 of the console carriers a year.
My guess is that we are going to continue to see major acceptance of additive manufacturing for parts that just a few years ago were deemed not feasible.
There might be a slowdown in companies touting the latest printer coming out of their skunkworks or a trend toward new materials that are only slightly better than the last version, but that might be a sign of the industry maturing.
IDTechEX predicts the desire to decrease labor cost and increase productivity will boost 3D printing and that automation will play a big role. Automating 3D printing will help with reshoring and reduce cost per part, which cuts labor cost and lessens the need for training employees, according to the report.
The report predicts the automotive market will continue to be a major driver for 3D printing as well as the defense industry, which has a big appetite for legacy parts, spare parts and on-demand parts.
I have long admired Protolabs Inc., a Minnesota-based processor that specializes in prototyping and low-volume manufacturing but has the ability to scale up to full production. 3D printing is an integral part of Protolabs’ service, and six years ago I visited the company’s facility near Cary, N.C. It has more than 100 printers using six different technologies.
The most interesting aspect of Protolabs’ business model is the way it has integrated 3D printing into a wide range of services so it can promise customers fast and comprehensive manufacturing. These services also include plastic and liquid silicone rubber injection molding, CNC machining and sheet metal fabrication.
This is a solid business model and has a lot to offer OEMs.
It is interesting that injection molding machinery manufacturers Arburg, KraussMaffei and Yizumi-HPM are now selling their own 3D printers for industrial applications. All three companies say the number of printers they have sold thus far is modest, but they believe it is a good long-term business.
The 3D printer you purchased two years ago that is now gathering dust may still be a useful processing machine. Think about how you can use it to expand your customer list.
Ron Shinn | Editor
Editor Ron Shinn is a co-founder of Plastics Machinery & Manufacturing and has been covering the plastics industry for more than 35 years. He leads the editorial team, directs coverage and sets the editorial calendar. He also writes features, including the Talking Points column and On the Factory Floor, and covers recycling and sustainability for PMM and Plastics Recycling.
Sign up for Plastics Machinery & Manufacturing Newsletters
The weekly voice for Plastics Processors and Manufacturers of Plastics Products. (3x/week)
Highlighting the most popular PMM articles as chosen by you, our readers. Discover the key topics of your peers and competitors, across the industry. (Monthly)
The latest news on plastics recycling equipment and technology. (Monthly)
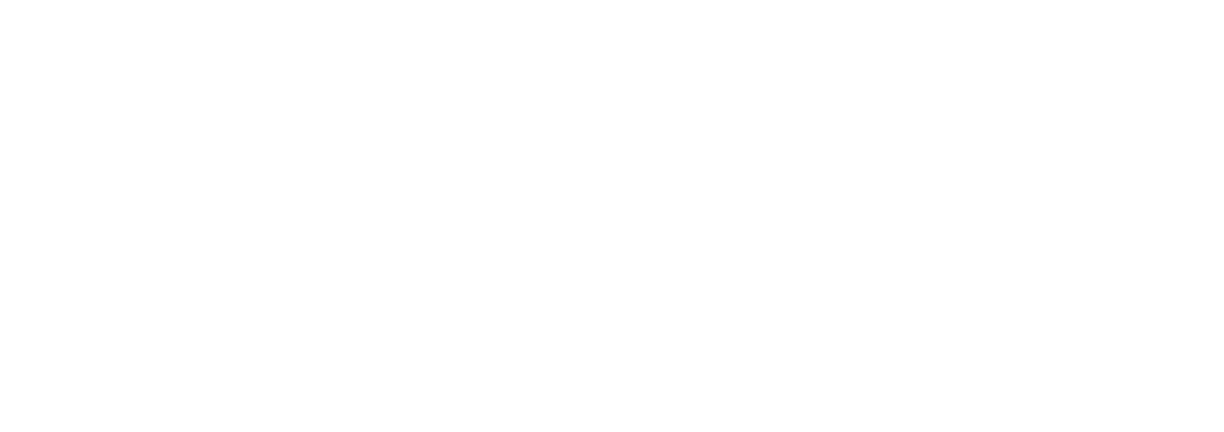