Problem: The maker of a badge designed to reinforce employee distancing wanted to expedite its path to market as the COVID-19 pandemic took hold.
Solution: Standardized processes at mold maker and molder Protolabs yielded a fast turnaround and $20,000 in savings.
By Karen Hanna
Manufacturers that could not send workers home as COVID-19 cases mounted in the spring found themselves confronting the potential day-to-day risks of a deadly virus. Keeping everyone safe took on new urgency. Getting risk-mitigation products to market became critical.
At Fleetwood Electronics, which makes low-power wireless devices and hospital ID tags, employees working on a Friday night in April leveraged their expertise to create a badge to reinforce safe physical distancing. They hoped it could allow the company’s 120 employees to work on site safely, but company leaders realized it would also have value for other businesses.
Related: Protolabs named one of IndustryWeek's "Best Plants"
To manufacture the new badge, which they called the Instant-Trace, they turned to Protolabs, a manufacturer of molds, as well as parts made through injection molding and additive technologies.
With companies battling to come up with innovations of their own, and desperate to stay open, time was of the essence.
Speed to market
Using ultra-wideband short-range wireless technology, the Instant-Trace flashes red LED lights and vibrates when wearers are too close to each other, and a web-based app records the encounters to facilitate contact tracing, should that be necessary.
Hayhoe had previously used Protolabs’ services and knew the Instant-Trace was “the right product at the right time.”
A contract manufacturer, Protolabs is built for speed, said Rob Young, the company’s product marketing leader for injection molding.
“We provide manufactured parts very quickly through a number of different services,” Young said. Unlike molders that can streamline the manufacturing process by making huge volumes of the same part, Protolabs focuses on creating efficiencies early in the manufacturing process, even when it comes to short runs. Working with about 50,000 product developers a year, it handles many programs involving volumes of 10,000 to 30,000 parts, with some clients requiring just 100 parts and others 1 million, Young said.
To get parts to market quickly, it has standardized its processes and machines, running more than 100 Haas milling machines and more than 150 presses from Toshiba and Arburg for thermoplastics and LSR, respectively.
“The bread and butter of our company was essentially to automate the front end of manufacturing, so whereas traditional molding would typically automate the back end of the process, we’re automating everything on the front end, so everything from the intake, analysis, the CAD models, the design of the mold, the vast majority of that is done through automation through proprietary CAD software, so we can go through those stages really, really quickly, like within hours,” Young said.
From design to deployment
As manufacturers raced to get products related to the pandemic to market, Protolabs realized early it could help ease the logjam.
“We felt that the best way that we could help from the business standpoint was when a customer would come to us — and this ended up being hundreds of customers over this time — if they said that this product was somehow related to the COVID-19 pandemic response, we would automatically expedite the parts as fast as we could physically manufacture them,” Young said.
He said Protolabs charged nothing to move such products to the front of the line.
After using 3-D printing to prototype the badge in-house, Fleetwood Electronics brought the innovation to Protolabs, using its CNC machining services to test the housing design of the badge.
Hayhoe and Protolabs communicated almost daily for a couple of weeks while finalizing housing and electronics designs, and Protolabs’ technical-support team provided manufacturability and materials recommendations. Protolabs helped identify specific blends of PC that would allow the flashing LED lights to be seen from the front of the badge.
“From the time we started to make the mold to the time that we delivered parts was just a couple days,” Young said.
Protolabs prepared tooling four weeks sooner than a traditional mold maker, and its work cost $20,000 less, Hayhoe said.
When it came to finding buyers for the badges, that speed paid off.
Hayhoe credits the nimble manufacturing process with allowing the Instant-Trace to hit the market in time to grab the attention of one of its first buyers, a Fortune 100 pharmaceutical company that now is one of Fleetwood Electronics’ biggest customers.
For users, too, the badge buys time — and peace of mind.
“How do you make a decision in the face of a positive case? You can overshoot and send everyone home, shut it all down. Or undershoot and put your team at risk. That’s scary,” said Eric Bronkema, director of information technology of Metal Flow Corp. A metal stamping plant based in the same town as Fleetwood Electronics, it provided its testimonial of the product to the company after implementing Instant-Trace for its own employees.
“We needed actual data,” Bronkema said. “Instant-Trace gave us that data, empowering us to do something concrete, and to do it efficiently, rather than making best guesses and running on gut feelings from our team on the floor.”
For Protolabs, the production of the Instant-Trace badge was just part of the pandemic story.
In the nine months since the pandemic began, Young said the company also made personal protective equipment and ventilator parts, along with other items related to COVID-19.
“I think there is 100 percent satisfaction that comes from being able to help and support the pandemic response,” he said.
Karen Hanna, associate editor
Contact:
Protolabs, Maple Plain, Minn., 877-479-3680, www.protolabs.com
Karen Hanna | Senior Staff Reporter
Senior Staff Reporter Karen Hanna covers injection molding, molds and tooling, processors, workforce and other topics, and writes features including In Other Words and Problem Solved for Plastics Machinery & Manufacturing, Plastics Recycling and The Journal of Blow Molding. She has more than 15 years of experience in daily and magazine journalism.
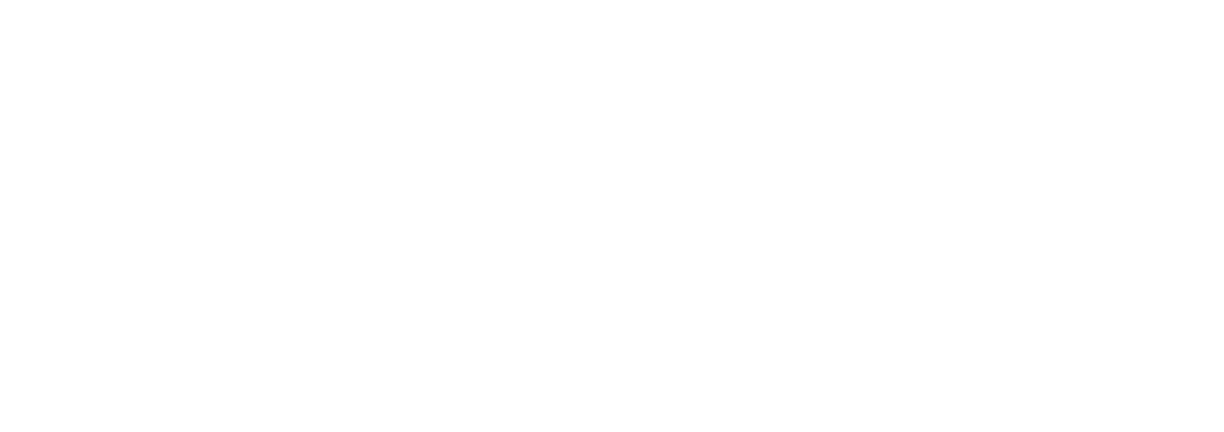