With its sights firmly set on advancing its position in plastics additive manufacturing, 3D Systems Corp., unveiled two major innovations during Rapid + TCT, held May 9-11 in Pittsburgh.
Its ProJet MJP 5600 is a multi-material composite 3-D printer that was producing power drive components during the show in a 17-hour single build using rigid white and rigid black resin. All resins on the MPJ 5600 are acrylate-based. Five materials can be used with the printer, including clear, elastomeric black and natural. The machine's maximum build volume is 20.4 inches by 15 inches by 11.8 inches. The printer uses 3-D Systems' proprietary multi-jet printing process, using phase-change material and UV light to cure and harden photopolymer resin into 3-D shapes.
The machine is designed to create validation prototypes, rapid tooling and dies for forming applications. The company said its proprietary jetting technology reduces part costs by up to 40 percent when compared with competing printers, and its print speeds are twice as fast. Officials said a lot of factors affect print speed, but the key to its speed is a wide-format print head that covers half the platform in a single pass. That allows fast print speeds and high throughput of parts.
3D Systems does not publicly disclose its pricing, but considering how much it costs to operate, the time it takes to print a part and post-processing time, officials said the printer is a cost-effective purchase in the long run.
"We really believe we have a technology and capability to drive significant value for the customers," said Jim Ruder, senior VP and GM of plastics for 3D Systems. "We blend rigid and elastomeric polymers. We blend them at the voxel level to achieve superior mechanical properties. This can be used for overmolded parts, jigs, fixtures and dies. You have a whole range of design flexibility that this printer enables."
The printer builds in tiny, 3-D increments called voxels — akin to pixels in 2-D printing. Voxel-level printing allows block-by-block fusion that translates into better properties, including significantly better mechanical characteristics, officials said.
"You can tune the combination of the different materials that you're printing to modify the hardness of the end product," Ruder said. "You can print two different materials and vary the hardness throughout the part. You can vary the mechanical properties of the part within the part.
"We look at every piece of that end-to-end workflow, and that is where part of our advantage becomes very compelling," Ruder said. This includes innovative software that allows for improved support structures. The combination of improving the manufacturing of the support structures and data-processing time improves production costs.
Clients who currently use the Projet 5500X, a printer 3D Systems released earlier, can use an upgrade program to convert to the 5600. Upgrades will be available starting next month.
To 3D Systems, the software that is being used is critical. Along with ProJet MJP 5600, the company also introduced its 3D Sprint 2.5 software at Rapid. 3D Systems plans to gradually roll out the upgraded software on all its printers.
"We are on a path toward supporting all of our printers very soon," said Carol Zampell, VP of software engineering, of making the software available for all of its printers.
The software features a single intuitive and streamlined user interface. In 3-D printing, especially stereolithography, the process 3D Systems' printers perform, the ability to quickly and easily remove support structures is critical. To meet these challenges, the software allows the printer to create parts with fewer support structures, using delicate, lattice-like structures that require less material and are easy to remove. These support structures can easily be brushed off once the part is produced.
Users can modify STL files, and make use of new slicing algorithms. The software works with the most popular file types, including IGES, STEP and OBJ, to name a few.
Angie DeRosa, managing editor
Contact:
3D Systems Corp.Rock Hill, S.C., 803-326-3930, www.3Dsystems.com
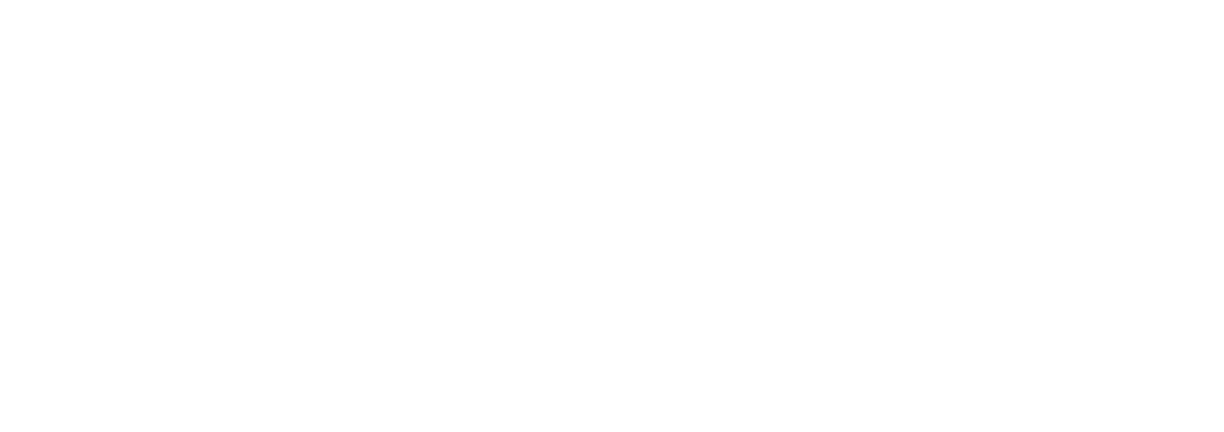