Reifenhäuser sheet line can switch from PET to PLA production
By Bruce Geiselman
In response to growing demand for more sustainable materials, Reifenhäuser has introduced a sheet extrusion line designed to process both PET and polylactic acid (PLA).
Demand for PLA, a bio-based material made from sugar, is growing, according to Reifenhäuser.
The plastics industry is experiencing a shift toward more sustainable strategies, and this trend harbors both opportunities and risks, the company said when announcing the new Mirex PET/PLA sheet line. Processors must be able to react quickly to changing market needs, by taking steps such as selecting the right raw material.
“The appeal of PLA, as we all know in this industry, is sustainability and recyclability,” said Steve Despain, VP of sales and marketing for Reifenhäuser Inc. “PLA fits right into that realm of what people classify as biomaterials. It’s a widely accepted material in not only our industry but by the end-user.”
Manufacturers of PLA cups, plates and clamshells can market them as being made from a bio-sustainable material, Despain said.
Consumer packaged goods producers are undertaking green initiatives that drive the popularity of PLA.
About 400,000 tons of PLA was produced worldwide last year, and production is expected to grow to 574,000 tons by 2025, according to market studies. About 70 percent of the PLA is going to be processed in the sheet sector, according to Reifenhäuser.
Processors who invest in PLA-capable equipment now will benefit from the coming upswing in demand, Reifenhäuser said. Due to its physical and mechanical properties, PLA is well-suited as a substitute for PET-based thermoplastics.
PLA and PLA blends are available as pellets in various grades for production of films, cups, bottles and other consumer goods, including trays for fruit, vegetables and meat.
The Mirex PET/PLA sheet lines include Reitruder co-rotating twin-screw extruders and a patented polishing stack. By using twin-screw extruders, instead of single-screw models, the lines enable direct extrusion without the need to dry the resin first. The Reifenhäuser lines thus use about 40 percent less energy than lines using single-screw extruders.
A line optimized for PLA production comes with optimized components, including a vacuum system with heated pipes and a different control unit, the company said.
“PLA is very temperature-sensitive, and it’s very hygroscopic,” Despain said. “We need to remove as much moisture as we can from it. We had to increase the vacuum pressure in our system, as well as control the temperature, so when we remove it, we don’t burn the material. PLA is a beautiful material, but it’s got some process challenges. It takes a little bit of nuance to run PLA. By increasing the vacuum and monitoring and measuring the temperature more accurately, it helps with the processing of the sheet.”
This optimized equipment also can be installed on existing lines as an upgrade to convert them to run PLA.
Reifenhäuser Inc., Maize, Kan., 316-260-2122, www.reifenhauserinc.com
Bruce Geiselman, senior staff reporter
Bruce Geiselman
Senior Staff Reporter Bruce Geiselman covers extrusion, blow molding, additive manufacturing, automation and end markets including automotive and packaging. He also writes features, including In Other Words and Problem Solved, for Plastics Machinery & Manufacturing, Plastics Recycling and The Journal of Blow Molding. He has extensive experience in daily and magazine journalism.
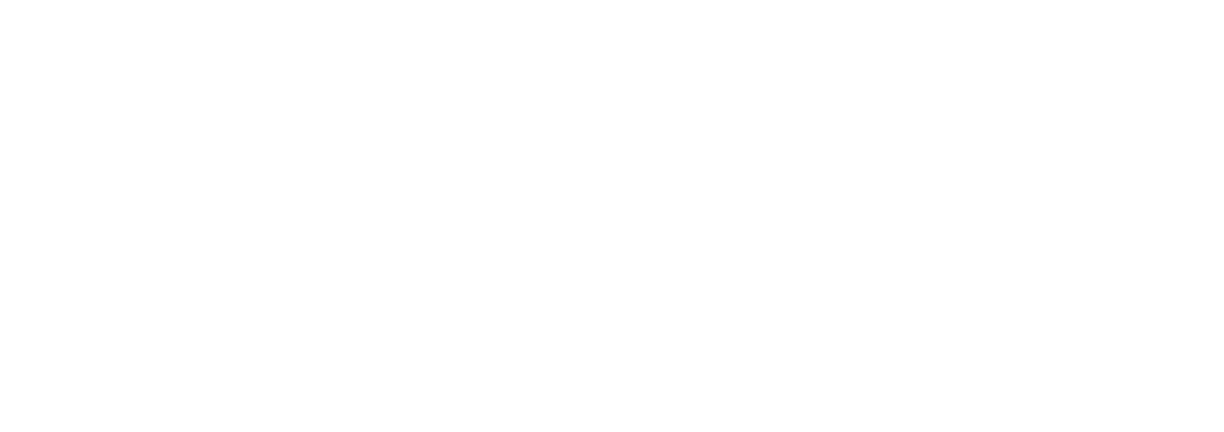