Thermoformer manufacturers woo former SencorpWhite customers
By Bruce Geiselman
Thermoforming manufacturers are stepping up to fill the void left by SencorpWhite.
Once a major player in the thermoforming industry, Sencorp surprised many last year when it announced that it would cease building new thermoforming machines due to “challenges in the continuing business environment in which the company operates.” At NPE2024, Illig, Kiefel and BMG highlighted options for manufacturers looking to replace the company’s existing thermoforming machines or buy additional equipment while keeping Sencorp tooling.
Illig, which did not bring any thermoforming equipment to the show, highlighted its new RDF 85 XL modular thermoforming system with a Sencorp 2500 interface.
“With the going-out of the market from Sencorp, our customers have been asking us: ‘Do you have a solution to run our existing Sencorp tools?’ Now they have a solution,” said Erik Hemgesberg, VP of Illig’s business unit for thermoforming and packaging systems.
The RDF 85 XL is an enlarged and reinforced version of the RDF 85 modular thermoforming system. Illig describes it as a cost-efficient thermoforming machine that offers a flexible solution for the operation of existing Sencorp 2500 tools.
To accommodate Sencorp tools, the RDF 85 XL has a forming area measuring about 3 feet in the production direction. Illig increased the punching force to 80 tons. As is typical with Sencorp, the forming and punching tools are changed in a block, according to Illig. The steel rule cutter was made moveable so that the tools can be lifted in and out as a block with a crane. The tools can then be pushed into the forming and punching stations via rail systems. Tool changes can be carried out in about 30 minutes.
The RDF 85 XL’s open tool interface means the machine can accept not only Sencorp 2500-series tooling, but also tooling designed by other equipment manufacturers, Hemgesberg said.
At NPE2024, Kiefel, part of the Brueckner Group, ran a Speedformer KMD 90.1 Premium machine equipped with a six-cavity Sencorp tool for 100 percent post-consumer recycled PET lids for aluminum ready-meal pans.
Unlike some other manufacturers who recently developed technology for running Sencorp tooling, Kiefel developed the technology years ago. It now is receiving increased interest from former Sencorp customers.
“The real emphasis that we’re placing on this show is, we had a competitor, Sencorp, that exited the market, and it’s left a lot of converters with a lot of Sencorp tools and no chance to buy new equipment to run them,” Kiefel Packaging VP Gary Sowden said. “Luckily, 10 years ago, we developed this platform with very simple adapters that can run Sencorp tools. We have a Sencorp tool in the machine right now that came out of a Sencorp 2500.”
The Kiefel KMD 90.1 Premium on display not only operated with a Sencorp mold, but did so very efficiently, Sowden said.
“In the Sencorp, it ran 10 to 11 cycles per minute,” Sowden said. “In our machine, it’s running just under 25. It’s the same mold. It’s a real benefit to customers — it’s easy to adapt the tools in, and then you gain a lot of enhanced performance.”
Former Sencorp customers could prove to be a sizeable market in the future as they look to replace and invest in machinery, Sowden said.
“They, over the years, had quite an installed base and had been a pretty popular brand here in North America,” Sowden said. “There are a lot of customers out there now that, as they make new machine purchases but have existing molds, need a way to deal with that.”
The KMD 90.1 Premium recently underwent performance enhancements, which corresponded with the renaming of the machine from the KMD 90.
The KMD 90.1 Premium offers faster ergonomic tool changes of only 1.5 hours, increasing machine utilization, according to a company press release.
BMG also has developed a product line to meet the needs of former Sencorp customers and continues working with customers looking for solutions for running Sencorp tooling, according to a company official.
“When Sencorp chose to no longer make equipment for customers, we had several of their customers come to us looking for a solution,” said Jake Kowalewski, BMG chief commercial officer.
Many of the companies had standardized their operations based on Sencorp equipment, and not all thermoforming machines can use that tooling, he explained.
“We worked with those customers to develop a solution that would accommodate the full suite of all the Sencorp machines and tool options that they currently had,” he said.
In addition to wanting to allow them to continue using their existing tooling, BMG wanted to deliver some advancements, he said.
The original technology request from a customer was for a machine compatible with the Sencorp Ultra machine line, according to BMG. BMG studied Sencorp's technology with the goal of developing a thermoforming machine that would be compatible with its tooling but exceed Sencorp’s performance. BMG “reached critical improvement levels in forming and trimming tonnage, oven heat capacity, platen layouts, stroke lengths, shut heights and servo-driven allowances,” according to a company press release. The enhancements will allow the customers to significantly improve their ROI, according to BMG.
BMG’s new NXTMod10 is capable of running tooling for the Sencorp 2500 thermoforming machine and the Sencorp 2500 Ultra machine, which has a larger forming area.
“Sometimes, you just have to step up to the plate and take a swing,” Kowalewski said. “We altered our production line and rescaled personnel responsibilities to execute a plan that could fulfill this customer’s needs on the best timeline possible to keep them in the game.”
As of mid-May, when NPE took place, BMG had completed 20 percent of the requests it had received from former Sencorp customers and anticipated being able to finalize all requests by the end of 2024. That’s a commitment to supply 20 machines in less than 12 months.
The NXTMod10 can run tools from most other major machine builders and third-party tooling providers, according to the company.
The forming area is up to 2.9 feet by 3.3 feet, which is the largest in the market, according to BMG.
Due to its modular design, the NXTMod10 also can be used for fiber thermoforming.
“There are modifications that have to be made,” Kowalewski said. “As you go from the plastic to a fiber, there are some modular changes.”
Because operators would need to swap out numerous stations, changing from plastic to fiber isn’t like “flipping a switch.”
“It’s not something that they would want to change over on a daily basis, but they will be able to swap or change the machine configuration in plant as needed,” Kowalewski said.
He said he is unaware of any other models capable of thermoforming both plastic and fiber. BMG is putting the technology to use creating a new product line: round pizza boxes.
BMG also offers its NXTFiber paper former, which comes with the necessary modules for fiber thermoforming.
Contact:
BMG, Beaverton, Mich., 989-435-7741, www.bmg-solutions.com
Brueckner Group USA Inc., Dover, N.H., 603-929-3900, www.kiefel.com
Illig LP, Indianapolis, 855-824-0004, www.illig.de/en-de
Bruce Geiselman
Senior Staff Reporter Bruce Geiselman covers extrusion, blow molding, additive manufacturing, automation and end markets including automotive and packaging. He also writes features, including In Other Words and Problem Solved, for Plastics Machinery & Manufacturing, Plastics Recycling and The Journal of Blow Molding. He has extensive experience in daily and magazine journalism.
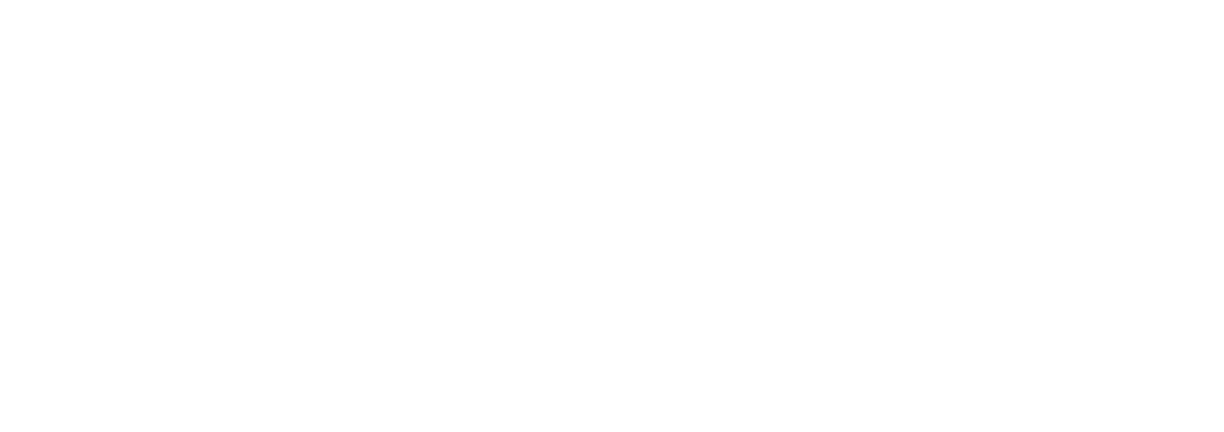