From the Summer 2024 issue of Plastics Recycling.
By Marissa McNees
The Azek Co. has been in the manufacturing space for decades, but since 2019 the Chicago-based company has ramped up its recycling efforts.
Azek is an industry leader in manufacturing wood-alternative outdoor living, home exterior and other products traditionally made of wood, according to Amanda Cimaglia, vice president of environmental, social and governance (ESG) and corporate affairs at Azek. The company manufactures decking, railing and cladding under its TimberTech brand and residential siding, trim and molding products under its Azek Exteriors brand, and all feature a varying level of recycled material, including recycled polyvinyl chloride (PVC), polyethylene (PE) and wood fibers.
Though sustainability had always been a consideration among Azek’s operations, Cimaglia says it truly became a priority in 2016, when president and CEO Jesse Singh joined the company and brought with him a new outlook.
“He came from 3M, so he came from a large, global, multinational company,” she says. “He saw our manufacturing processes and appreciated how much raw material we were using, how many pounds of raw plastic material we were using, and he [said], … ‘There’s got to be a better, more efficient way to do this.’
“He had an inclination that switching to more recycled plastics would not only benefit the environment and keep that [material] out of landfills, but also positively impact our bottom line since the recycled material Azek uses tends to be less expensive than virgin material. So, there’s both a business case for it and a sustainability case for it.”
As Azek then formalized its ESG strategy and considered the impacts it has as a company and the impact it can have on the world, recycling became a big part of that strategy—“if not the biggest,” Cimaglia says.
But when Singh first pitched the idea of more recycling, Cimaglia says there was some initial pushback.
“It took very strong leadership on Jesse’s part to say, ‘Look, I understand this is how you’ve always done it, but there’s a better way,’” she says. “Azek had to retool its machinery; we had to build a recycling facility so we could vertically integrate on the recycling front, and so there was a shifting mindset that under Jesse’s leadership, it didn’t take long for people to see the benefits of using more recycled material.”
In the eight years since Singh joined the company, Azek has seen its recycling efforts continue to grow, and with a strategic partnership formed in 2020, the company has increased its use of recycled material in many of its core products with no intention of slowing down.
Finding the right partner
Azek acquired Ashland, Ohio-based PVC recycling company Return Polymers in January 2020. Return Polymers has been in operation for more than 30 years, collecting and grinding PVC, analyzing the material in a lab and turning it into a mechanical blend that original equipment manufacturers can use for decking and other building products.
Return Polymers was Azek’s primary supplier of recycled PVC, and though Azek uses a combination of virgin and recycled plastic in its products, Cimaglia says as part of the company’s recycling journey, its goal is to use an increasing amount of recycled material.
“We have the biggest opportunity to increase the percentage of recycled material that we use in our PVC-based products, whether that’s decking, railing, exterior trim, cladding or siding,” she says.
Azek’s trim and siding products contain approximately 30 percent recycled PVC. Its TimberTech Advanced PVC decking portfolio is made with about 60 percent recycled material, which Cimaglia says is the highest percentage of recycled material available in the current PVC decking market. “We’re really proud of that,” she says.
The acquisition also came with an increased role for Return Polymers, which found itself with quite a bit more material coming in and the need to rapidly expand operations. Laurel Foell, business development specialist at Return Polymers, says the increase was “wonderful” and a challenge for which the team was ready.
Cimaglia adds of the early days in Azek’s recycling journey, “We had a lot of decking contractors that [said], ‘We love working with your products, we love your material, but we know you can recycle the scrap cutoffs [and] we need you to support us in sending that material back to you instead of us having to pay for it to go to a landfill.’”
In November 2020, months after Azek acquired Return Polymers, the companies piloted a recycling program—the Full-Circle PVC Recycling Program—that included deploying collection bins on job sites or at dealers and lumber yards so contractors could fill them with scrap cutoffs or any PVC material they were removing from a building. The program started with smaller 4-foot-by-4-foot totes but has expanded over the last two years to include bins that can hold larger-format PVC scrap such as end-of-life vinyl siding.
“There’s a whole vintage of vinyl siding that’s at the end of its useful life and we don’t want that to go and sit in a landfill and take hundreds of years to decompose,” Cimaglia says. “We have the processing experience, logistical systems and expertise to be able to process that in-house and give it a new life.”
Coming full circle
The Full-Circle PVC Recycling Program involves a four-step process: collection, logistics, processing and sustainable product manufacturing.
First, Return Polymers works with contractors and local dealers to determine which size collection bin will work best on a particular job site. Once the bins are full, the company facilitates pickup before the material is taken to a Return Polymers processing site. The collected PVC is reprocessed into recycled polymer materials in-house for Azek to manufacture into new decking, siding, cladding and trim.
“There’s so much of this material in construction and demolition, we just saw such a need for this type of program to exist,” Cimaglia says.
With more than 1,000 totes in circulation, Foell says the program has a very strong foothold in the Northeast, through the South and into the western region of the U.S., and her team is working to expand into California and into the West Coast—a goal she expects to reach this year. Large-format bins are concentrated around the regional grinding centers to ensure logistical support and customer service, making it easier for contractors to participate.
In May 2023, Azek and Return Polymers introduced trailer-sized bins—Foell describes them as “beautiful dumpsters”—to the program, deploying them in Return Polymers’ home state of Ohio to collect PVC trim, fencing and siding from as far north as Cleveland and down through Cincinnati. There currently are more than 70 bins that can be sent to job sites, and Foell says most of them are filled up and returned biweekly to the company’s grinding facility in Ashland.
“We’ve been able to collect from people who are really right in our backyard … [and] we’ve been able to reach people that we weren’t able to reach before due to the fact that they had such a larger material dimension,” she says.
“When you’re talking with contractors, you’re really in the business of changing mindsets of where this material can go after use. Return Polymers is having to re-teach what can be recycled and how it can be effectively recycled,” Foell adds “You’ve had family businesses doing this for decades and they’ve never had to remove certain materials like wood or take out nails, and suddenly they have the option, if done correctly, for this material to go somewhere other than a landfill. … My team has been able to work with a lot of businesses that are inclined to change, eager to learn and want to do better than just landfilling a reusable product.”
The goal, she says, is to prove that if deploying trailer-sized bins to job sites in Ohio can yield even more material without major logistical headaches, this aspect of the Full-Circle program can be introduced in more regions across the U.S.
“One of the smartest things we did when we first started this program was pick strong distribution partners who are able to hold a full truckload of bins—between 70 to 140 bins at a time—and are able to distribute them to the contractors via the lumber yards and getting them back from the contractors,” Foell says.
“We understand that to have anyone who’s going to be willing to put the time and effort into recycling this product, we will work with them as long as they’re getting us good [material]. We always figure out a way to make it work,” she adds.
The partnership between Azek and Return Polymers made sense logistically, too, as Azek has leveraged its relationships with its TimberTech and Azek Exteriors distribution partners, including about 40 distribution partners with more than 170 branch locations across the United States.
“Because we already had those relationships with them to ship our products, this is almost like creating a reverse logistics program,” Cimaglia says. “I think that’s something that’s also strengthened our relationships with them and been able to allow them to strengthen their relationships with their dealers or lumber yard partners. It’s really a ‘rising tide lifts all boats’ situation. We’re able to support one another and advance each other’s recycling goals, which is really rewarding for everyone involved.”
With the help of its Return Polymers team, each year, Azek uses between 400 million pounds and 500 million pounds of scrap material to manufacture products across its portfolio.
“Our leadership team has done a phenomenal job of growing the program to meet internal and external demand while continually expanding and adding capacity,” Foell says. “It’s been a phenomenal journey to think back where we started and where we are now in 2024.”
Prioritizing recycling
Azek’s operations include about 14 manufacturing and recycling facilities, with its main manufacturing locations in Wilmington, Ohio; Scranton, Pennsylvania; and Boise, Idaho. Its main recycling hubs are in Ohio—in Wilmington for polyethylene recycling and in Ashland, Ohio, where its partner, Return Polymers, recycles PVC.
Cimaglia says Azek’s recycling strategy draws upon two proprietary technologies the company employs: one for PE and one for PVC.
“There is a more mature market for recycled polyethylene than there is for PVC, which is more fragmented and why we saw a need—not only as a recycler, but a consumer of that product,” she says. “I think that’s also what makes us unique as a company is that we’re able to process and consume two types of plastic material that most other companies cannot or do not want to use.”
Azek’s goal is to use 1 billion pounds of recycled material annually, and Cimaglia says the company is about halfway there. For example, in 2019, Azek decking products contained about 40 percent recycled PVC, and today, they contain about 60 percent recycled PVC. Generally, most Azek products incorporate some level of recycled content, using a combination of postconsumer and postindustrial materials.
“I think one of the biggest challenges with recycling is we’re getting all these different sizes, compositions, colors and form factors,” Cimaglia says. “It’s so variable, so how do you take a product that is so variable as an input but process it into something consistent to go into the manufacturing process.
“I think those processing and technology capabilities have been something that has allowed us to innovate and expand our product portfolio. It’s the art of taking the chaos that is recycling and converting it to the consistency required to make a world-class product.”
Azek also has a partnership with online retailer ThredUp that started less than two years ago in which the retailer supplies its PE mailer bags to Azek for use in its TimberTech Composite products.
“These types of partnerships are things that we’re really excited about,” Cimaglia says. “We want more and more suppliers and direct sourcing partners like ThredUp and other consumer brands that we can partner with on plastic wrap, shrink wrap, pallet wrap—any type of stretchy plastic film. We’re always on the hunt for more recycling partners.”
With PVC recycling, in particular, the biggest challenge they’ve faced has been the same as when Singh joined the company and emphasized recycling as a critical part of Azek’s operations—educating contractors and other potential suppliers that the material can be recycled and should not end up in a landfill.
“Most people don’t understand how well [PVC] can be recycled, how safely it is recycled every day and the diversity of applications it can go into,” Foell says. “You have to be willing to look at who you partner with and understand their capabilities and motivations so you can align appropriately.
“The Full-Circle program is the best way of reaching all those who want to be recycling but don’t have the space, the availability or the funds to do it. We give the option to work with people who are trying to do the right thing every single day, they just didn’t have an outlet for it. We have created the end market for this type of otherwise hard-to-recycle material. And, in my opinion, 1,000 pounds—although it might not be a lot in the scheme of things—1,000 pounds out of the landfill from Joe or Jill down the road is still 1,000 pounds. That’s a win.”
For more information:
The Azek Co., www.azekco.com, 877-275-2935
Return Polymers, www.returnpolymers.com, 419-289-1998
Marissa McNees
Marissa McNees is Managing Editor of Recycling Today and can be reached at [email protected]. This story was published in Plastics Recycling, a joint publication of Plastics Machinery & Manufacturing and Recycling Today.
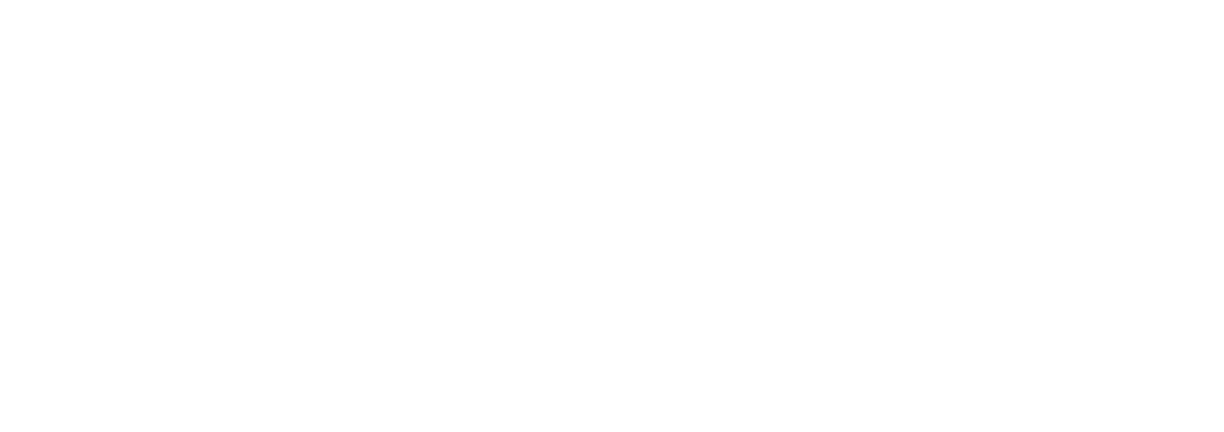