NPE Booth W5161
Farrel Continuous Mixer (FCM) An alternative to conventional compounding technologies, these Farrel Pomini compounding systems, launched in 1963, have two counter-rotating, non-intermeshing rotors and a large free volume mixing chamber. Mixing intensity is adjustable by changing rotor speed, working volume, thermal conditions and orifice position. The FCMs are ideal for compounding highly filled, temperature-sensitive and abrasive polymers.
What’s new? Optimized-for-recycling versions that can perform applications appropriate to mechanical and chemical recycling processes. Depending on raw material properties, the FCMs’ standard hopper can be replaced with an auger or piston-actuated crammer. The infeed of the systems’ mixers has been optimized with a patent-pending grooved mixer feed section and improved rotor feed flights. To reduce wear from contaminates and corrosion, the FCMs are hard-coated. They feature a Mixer Vent Filtration system that removes all moisture, volatiles and dust from the mixer vent, and cleans the exhaust air. Based on filtration requirements, Farrel can adapt any type of screen changer or continuous filtration technology to the end of the extruders. For chemical recycling, the FCMs serve as the primary stage of pyrolysis to heat and melt plastic. They can meet specific temperature and pressure conditions to homogenize feedstock resins, and maintain low process temperatures, with short residence times and efficient rotor shear, making them ideal for processing temperature-sensitive resins or materials with prior heat history applications.
Benefits Versatility and recycling efficiency. The new, energy–efficient systems can be used in mechanical recycling processes involving PE, PP, PVC and PET feed streams, and chemical recycling/pyrolysis processes involving film scrap, PE, PP and tire rubber streams. Based on their processing characteristics, polylactic acid, polyhydroxyalkanoate, polybutylene succinate also are appropriate for mechanical recycling via the FCMs.
Farrel Corp., Ansonia, Conn., 203-736-5500, www.farrel-pomini.com
Vital Statistics
Model |
Nominal hourly production rates |
4UM |
About 880 pounds to 1,540 pounds |
5UM |
1,760 pounds to 2,870 pounds |
6UM |
3,310 pounds to 5,510 pounds |
7UM |
4,410 pounds to 7,720 pounds |
9UM |
6,610 pounds to 15,430 pounds |
12UM |
11,020 pounds to 30,860 pounds |
13UM |
17,640 pounds to 39,860 pounds |
16UM |
33,070 pounds to 55,120 pounds |
18UM |
44,090 pounds to 88,180 pounds |
Karen Hanna | Senior Staff Reporter
Senior Staff Reporter Karen Hanna covers injection molding, molds and tooling, processors, workforce and other topics, and writes features including In Other Words and Problem Solved for Plastics Machinery & Manufacturing, Plastics Recycling and The Journal of Blow Molding. She has more than 15 years of experience in daily and magazine journalism.
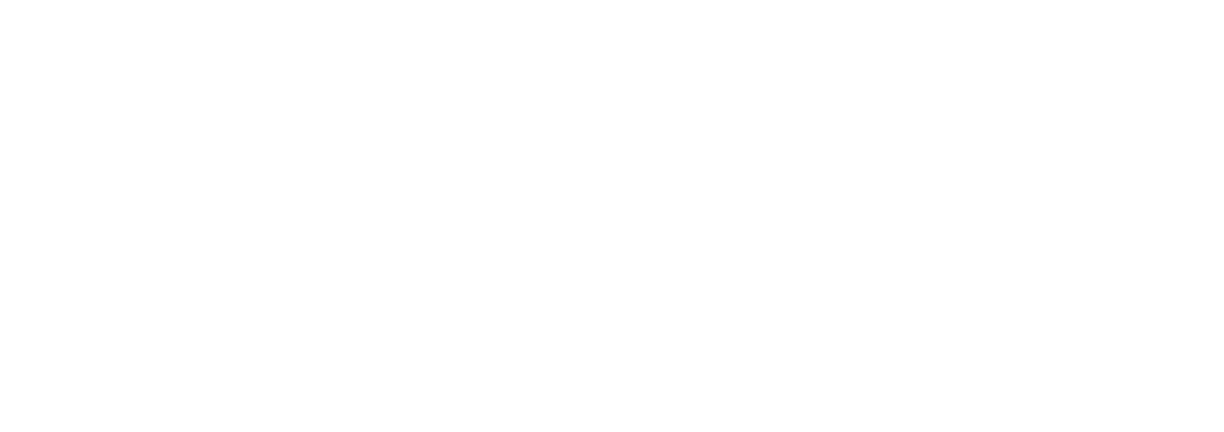