DAVIS-STANDARD
Davis-Standard’s newest product appropriate for recycled resin pelletizing lines is its Industry 4.0 monitoring package, the DS Activ-Check system.
“It’s predictive maintenance,” said Steve DeAngelis, VP of sheet, film and reprocess/reclaim for the company. “You know when it’s going to fail, so you plan on downtime rather than unexpected downtime.”
DeAngelis said the first pelletizing line equipped with DS Activ-Check that is targeted for handling recycled resins has been sold and will be installed in the next few months.
Vibration sensors on the extruder reducer supply data on the condition of the gears, bearings and lubrication system. The extruder motor is supplied with combination temperature and vibration sensors. Operators can monitor key parameters in the drive power unit, such as operation hours, number of run commands, cooling fan maintenance, capacitor maintenance and soft-charge bypass relay.
Other features that the device monitors include the reducer lubrication system, extruder motor characteristics, the drive power unit, and barrel heating and cooling.
“It’s monitoring how the motor’s performing, how the gearbox is performing, and it’s creating a baseline database of information,” DeAngelis said.
The system tells the operator that bearings are likely to fail, for example, in a certain number of hours, turns of the switch or cycles. The vibration signature can indicate when to change the oil.
The aim is to eliminate all unplanned downtime related to the extruder, he said.
AMERICAN KUHNE
American Kuhne has expanded its new XC300 Navigator control to its pelletizing systems. The company shipped the first pelletizing line equipped with the controller in March to a major rotomolder, which will use it to recycle and reintroduce its internally generated regrind to its primary process, said Mike Duff, director of business development for Welex and American Kuhne, which are brands of Graham Engineering.
The XC300 Navigator controls the pelletizing process, matching the extruder speed and/or melt pump speed to the cutter speed, which ensures consistent pellet size and shape. The control monitors extruder pressures, extruder speeds and drive loads.
The control also provides notifications about changes in water-bath temperature, which can indicate a shift in the process or an outside change that could hurt pellet quality, Duff said. It can monitor and control the process, whether the system uses underwater, water-ring or strand pelletizers. The rotomolder will be using a 130mm water-ring pelletizing system to introduce functional surface modification additives to create the raw material for rotomolding.
“By introducing a modern control system, from feeder through pellet drying, the entire process can be governed, monitored and improved,” he said. “With on-line trending, the operator can see instant correlation data, including extruder pressures, extruder speed, melt temperatures, water-bath temperatures and cutting speeds.”
Often, the repelletizing process is ignored by plant managers, Duff said. Commercial resin manufacturers produce a highly consistent pellet. “If this highly engineered, controlled virgin material is blended with internally generated, uncontrolled product, it can add variation and stress to the end product — a ‘garbage in, garbage out’ result; however, when the internal process is controlled, so is the product, improving the result,” he said.
COPERION
Coperion is offering recycling-friendly modifications for its pelletizing systems.
One option is the use of belt filters instead of cartridge filters. This is to address greater contamination, said Stefan Wygas, head of engineering for Coperion Pelletizing Technology.
In addition, wear-protection features are available because of the abrasive nature of recycled materials. Those can include nitro carbonization of split sieves, different coatings for the upper feed roll and a variety of materials, such as tungsten carbide, for the cutting rotor. This provides good product quality and service life even when processing recycled materials that put intense strain on conveying and pelletizing equipment.
Quick-exchange conveying bands with a cantilevered (single-bearing) belt design present another option for recycling applications. The feature allows for quick maintenance.
One other component for recycling applications is a band filter for process-water systems. The filter ensures clean water and prevents cross-contamination, Wygas said.
The options are available on Coperion’s semi-automated models SCP 100, SCP 200, SCP 300 and SCP 400, and its automated lines, the ASC 500 and ASC 700. Those products are complete systems that include the conveyor, pelletizer, suction device and, when applicable, a process-water system.
ADG SOLUTIONS
ADG Solutions, working with Davis-Standard, has two recent developments for pelletizing post-consumer and post-industrial plastics.
The first is a pelletizing system to process both nylon and PET post-consumer carpeting. The system, which will be delivered to a customer soon, uses an 8-inch Davis-Standard extruder with double venting and a closed-loop vacuum system, said ADG President Sandy Guthrie. It also features a Davis-Standard backflush screen changer and a 12-inch water slide to a rotary cutter.
ADG supplied a feeding conveyor with metal- detection capability, as well as a pickup hopper and auger that moves pellets from the pelletizer dryer to a pellet classifier. The classifier discharges pellets into another hopper. Following metal detection, the material flows into a storage hopper that is used to fill and weigh gaylords. An automated ADG system moves the gaylords and labels them according to time, weight, material type and other characteristics.
What’s distinctive about the pelletizing line, Guthrie said, is that it will handle only post- consumer carpet. The resulting pellets are used in automotive parts.
The second pelletizing line features a Weima shredder and a Davis-Standard 6-inch double- vent extruder with a fully automated feed system. The line can process everything from roll stock to films made for either consumer or industrial products.
The Davis-Standard air-cooled Ram Stuffer extruder has an L:D ratio of 38:1. The line includes an ADG CFO-20 self-cleaning filter for handling heavily contaminated materials. The filter has a 20-inch-diameter punched plate with hard surfacing for durability.
The system’s water-ring pelletizer is capable of handling both PE and PP.
ADG integrated the complete conveyor system, which features automatic metal ejection. ADG also supplied ancillary equipment, such as a complete water chiller system.
Allan Gerlat, correspondent
Contact:
ADG Solutions LLC,
Tucker, Ga., 678-292-6144, www.adgs.net
Coperion Corp.,
Sewell, N.J., 201-327-6300, www.coperion.com
Davis-Standard LLC, Pawcatuck, Conn., 860-599-1010,
Graham Engineering Corp.,
York, Pa., 717-848-3755, www.americankuhne.com
Request More Information
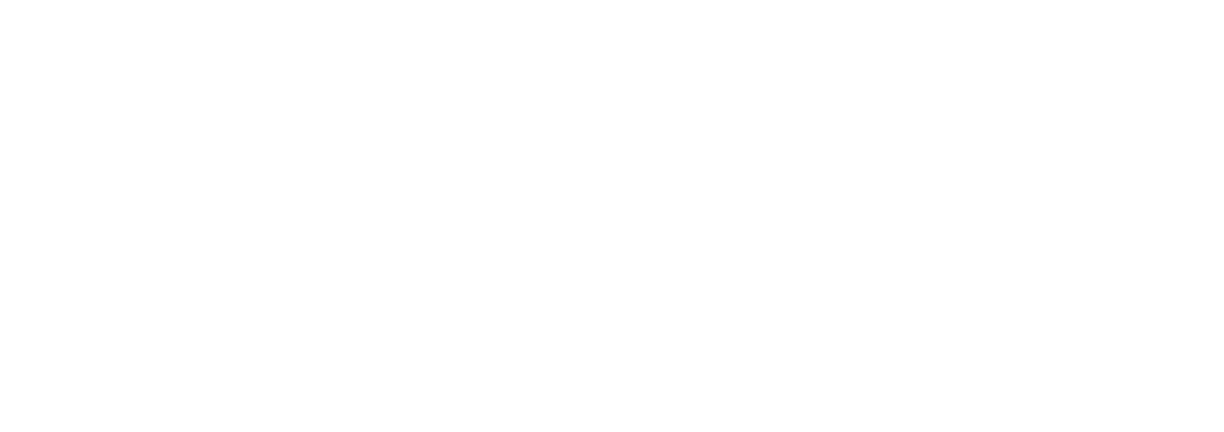