By Lynne Sherwin
A lot can change in six years. For Moretto at NPE2024, it meant a North American market presence that had grown significantly enough to make the leap from “a little corner and a little booth” in 2018 to an 8,400-square-foot space in the middle of the West Hall, said Moretto USA GM Gene Flockerzi.
The company, headquartered in Massanzago, Italy, took advantage of the additional visibility to show off multiple pieces of its distinctive sky-blue and stainless-steel auxiliary equipment. “We’re very proud of our design,” Flockerzi said, adding that some visitors compared the equipment to a Ferrari.
But form is nothing without function, and Moretto emphasized the energy savings and smart capabilities of its equipment, along with the fact that the company builds it from the ground up.
“Eighty-five percent of our product is made in-house. We bring sheet steel in the back door; we put finished goods out the front door. During the supply chain debacle during COVID ... we were able to maintain deliveries and get things out because we were our own supply chain. So, we had no issues,” Flockerzi said.
He said the approach helps keep Moretto’s equipment affordable, since the company is not paying markups to buy components from other companies.
One of Moretto’s biggest hits at the show was all about small. The DGM 20 Gravix gravimetric blender is designed for molders of small parts, especially in the medical market, that handle low throughputs — up to 44 pounds per hour — but need high blending accuracy.
“It's a cute little thing. People say it looks like an espresso machine. But it gives you all the great features that we have and we've developed over the last year. We've worked it down to be small enough that we can put it on very small machines,” Flockerzi said.
It has Moretto’s double-eyelid shutter valves for precise dispensing of resin, regrind or additives, and its Rotopulse microdosing technology for waste-free blending.
Flockerzi called the reception at NPE for the DGM 20 Gravix “phenomenal.”
“We're out there tearing it apart every 10 seconds and putting it back together,” he said. “Customers want to see it, they're excited about it, because they used to have to put these bigger machines on these little wee presses, and it didn't make sense.”
The CRX Comb Mobilux integrated drying and conveying series, another NPE introduction, is also tailored for smaller throughputs — 5 to 50 pounds per hour.
The series is built around the X Comb compact dryer line and includes an OTX (Original Thermal eXchanger) drying hopper, a conveying unit with Duo valve and vacuum receivers, and a trolley for easy placement beside the press. It has a single power supply and a 7-inch color touch-screen control.
The dryers include a honeycomb wheel of Zeolite desiccant, and they maintain consistent drying quality automatically; the operator needs to input only material type and throughput, and the dryer manages all other parameters.
“We spent a lot of money in development over the last few years with regard to drying principles,” Flockerzi said, and the company is particularly proud of the technology behind the OTX hopper.
On the older design, material flowed at different rates depending on where it fell into the system: “You’re not getting your material the same amount of time at the same temperature. So, you had to ... size the systems for the inefficiencies in the drying hopper,” Flockerzi said.
Material flows more evenly through the redesigned version with its bullet-shaped interior, so the hopper volume can be decreased while still achieving the same throughput, saving about 40 percent in energy costs.
Flockerzi said another innovation that’s been scaled down into Moretto’s smaller dryers is the Antistress system, which monitors the material as it exits the hopper, automatically adjusting airflow via a variable-frequency drive (VFD) to maintain the correct temperature, avoid overdrying and save energy.
“It's getting some feedback from the drying system and makes the proper adjustments, makes sure you're meeting that unique drying condition at that time,” he said, as opposed to fixed-speed motors that can waste energy and deliver too much or too little airflow.
“Energy savings is significant. So, the byproduct is you're not only doing it right, you’re saving a ton on energy costs,” he said.
Company founder and President Renato Moretto is “very, very big on sustainability ... and that runs through the system,” Flockerzi said, which translates into benefits for customers.
He added that Moretto and the company are “firm believers in intellectual property, coming up with things [that are] new and exciting for customers. We have about 169 patents that are active right now.”
Flockerzi said he expects Moretto USA to set a sales record in 2024.
“Our big customers are coming back time after time after time. We've done multiple plants. So customers are very happy, not only with the first installation, but the second or more,” he said. “It's been very, very rewarding, personally, professionally and for the Morettos as well.”
Contact:
Moretto USA Corp., Jackson Center, Pa., 724-269-7600, www.moretto.com/en/
Lynne Sherwin | Managing Editor
Managing editor Lynne Sherwin handles day-to-day operations and coordinates production of Plastics Machinery & Manufacturing’s print magazine, website and social media presence, as well as Plastics Recycling and The Journal of Blow Molding. She also writes features, including the annual machinery buying survey. She has more than 30 years of experience in daily and magazine journalism.
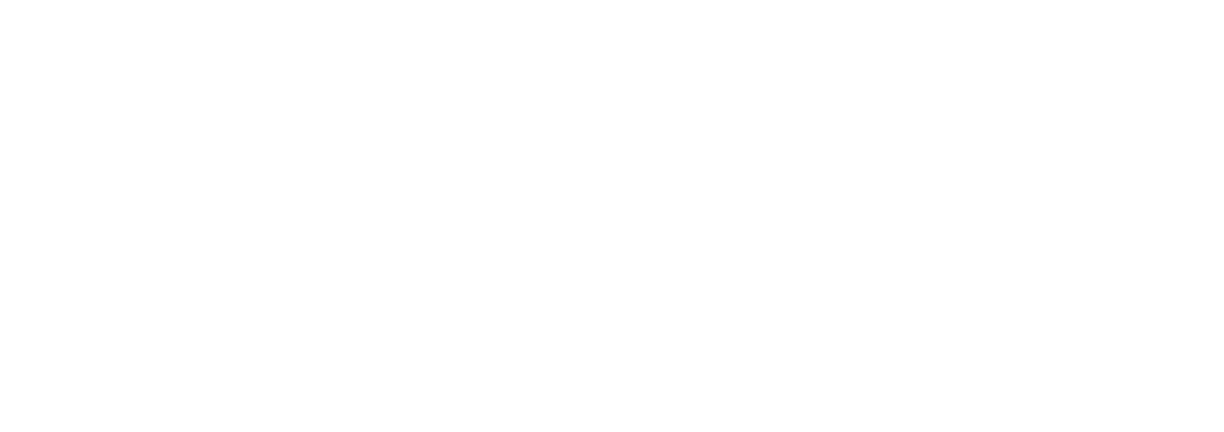