By Nathan Knotts, Industrial Oils and Grease Portfolio Architect at Chevron
In the world of plastics manufacturing, efficiency is king, and nothing can sabotage smooth operations faster than hard-to-remove varnish deposits. Whether it’s hydraulic systems, turbines or compressors, keeping your equipment running is critical. But how do you fend off the unwelcome guest known as varnish?
Varnish buildup can cause major headaches, and that’s why we are diving into how you can better identify, test and tackle varnish problems head-on, ensuring your machinery stays in peak performance mode and your production lines hum along without a hitch.
Identifying varnish problems
Varnish deposits can significantly impact the performance of plastics machinery. Common symptoms include sticky servo or thermostatic valves, sticking hydraulic cylinders, inefficient oil coolers, high bearing temperatures or sub-synchronous vibration in high-speed bearings and seals. These symptoms can cause inefficient operation and increased wear and tear on machinery. Identifying these signs early is crucial to mitigating extensive damage and maintaining optimal machinery performance.
Recognizing varnish issues early not only helps to maintain machinery efficiency, but also extends the life of the equipment. For instance, sticky servo valves can lead to reduced precision in machine operations, affecting product quality and consistency. Sticking hydraulic cylinders can disrupt the smooth operation of machinery, leading to potential production delays. Similarly, inefficient oil coolers and elevated bearing temperatures can cause significant wear, increasing maintenance costs and potentially leading to unexpected downtime.
In addition, addressing varnish problems promptly can also improve safety in the workplace. High temperatures and unusual vibrations are not just signs of varnish deposits but are also indicators of potential mechanical failures that could pose safety risks. Regular monitoring and early intervention can prevent accidents and ensure a safer environment.
Testing for varnish
Testing for varnish involves oil analysis through life prediction tests and performance measurement tests. While life prediction tests estimate the remaining useful life of the oil, performance measurement tests provide a better indication of potential varnish issues by assessing the current performance of the oil.
However, oil analysis presents several challenges. The oil sample tested may not accurately represent the entire system, and varnish potential can vary throughout the year based on system usage. Measuring varnish precursors is difficult due to their tiny and oil-soluble nature, and there is no direct definitive method for identifying varnish-related issues without measuring critical parameters or visually inspecting the machinery for deposits.
Oil analysis should be conducted regularly as part of a preventive maintenance strategy. By establishing a routine testing schedule, you can track the condition of the oil over time and identify trends that may indicate emerging varnish problems. This proactive approach allows for timely interventions, such as oil changes or system cleanings, before varnish deposits become severe enough to affect machinery performance.
In addition to oil analysis, visual inspections play a crucial role in detecting varnish. Regularly checking key components, such as valves, cylinders and bearings, can reveal early signs of varnish buildup. Combining oil analysis with visual inspections provides a comprehensive understanding of the machinery’s condition, enabling more effective maintenance planning.
How to more easily eliminate varnish
The effectiveness of cleaners in removing varnish from plastics machinery varies depending on the type of deposits. Soft varnish and sludge typically clean quickly and completely, while hard polymerized deposits can be stubborn and may not be fully removed. Areas with low flow or low temperatures are less likely to be thoroughly cleaned. When using cleaners during operations, it is important to consider their impact on lubricants. Some top-treat life-extender products may alter the balance of modern lubricants and cause unexpected issues. To avoid these problems, it is recommended to use cleaners at the end of the oil’s life.
Selecting the right cleaner for your system is crucial. Cleaners designed specifically for industrial use are more effective in breaking down stubborn varnish deposits without damaging the machinery. It’s also important to follow the manufacturer’s guidelines on the concentration and application of the cleaner to ensure optimal results.
Using cleaners during routine maintenance can help prevent the buildup of varnish. Regular cleaning schedules, aligned with oil changes, can maintain the cleanliness of the system and enhance the performance of the lubricants. By integrating cleaning into the maintenance routine, you can significantly reduce the risk of varnish-related issues and extend the life of your equipment’s fluid and the machinery.
Mastering maintenance: Best practices for peak performance
Effective system maintenance involves several best practices to ensure optimal performance and longevity of plastics machinery. Draining systems should be done while the oil is warm and recently circulated to maximize varnish removal. Allowing the oil to cool can cause varnish to redeposit on equipment walls. What’s more, reservoir cleaning should consider the impact of varnish layer exposure to air for great lengths of time, as it can cause varnish on reservoir walls to polymerize and harden, making removal more difficult.
For filter maintenance, be aware that some cleaners can plug filters depending on the varnish and oil chemistry. It is good practice to have spare filters available during cleaning and monitor differential pressure to ensure filters are capturing varnish particles.
Another crucial aspect of system maintenance is keeping detailed records of all maintenance activities. Documenting oil changes, cleaning schedules, and any varnish-related issues can help identify patterns and optimize future maintenance strategies. This historical data can also be valuable when troubleshooting recurring problems or assessing the effectiveness of different maintenance approaches.
Training maintenance personnel is also vital. Ensuring that your team is well-versed in the latest maintenance techniques and that they understand the specific requirements of your machinery can lead to more effective and efficient maintenance practices. Regular training sessions and updates on new technologies or products can keep your team prepared to handle any maintenance challenges.
Cleaning and refilling practices
Proper cleaning and refilling practices are essential for maintaining the efficiency and longevity of the fluid and machinery. Rinse flushing involves the thorough removal of old oil, especially if it was degraded or if there were severe deposits. Then, put a set volume of a given flush fluid or new fluid into the system and charge the machinery and run this portion of fluid to further remove the degraded material from the system. This is then drained and any material suctioned out or mopped up. This ensures that the new oil performs optimally without contamination.
Depending on the complexity of your system and the capabilities of your team, you may handle cleaning internally or hire a service provider. Service providers offer valuable expertise, especially for tasks such as confined space entry, certified oil disposal and determining the most effective cleaning practices.
When deciding between self-cleaning and hiring a service provider, consider the benefits of each approach. Internal cleaning allows for more control and can be cost-effective if your team is experienced and equipped with the right tools. However, service providers bring specialized knowledge and can often complete the cleaning process more quickly and thoroughly, minimizing downtime.
Service providers can also offer additional services, such as oil analysis, system audits and recommendations for improving overall system performance. Partnering with a reputable service provider can provide peace of mind, knowing that your machinery is maintained to the highest standards.
Evaluating cleaning effectiveness
Evaluating the effectiveness of cleaning involves monitoring several key indicators of success. Aside from visual inspection of deposits, a noticeable reduction in oil temperature, lower bearing temperatures, improved valve performance and reduced vibration are strong signs of effective cleaning. A darkened oil color suggests that insoluble varnish precursors are now stabilized in the oil, preventing further deposit formation. In addition, the presence of captured debris in filters is a clear indication that the cleaning process has effectively removed varnish particles from the system.
Regularly evaluating the cleaning process ensures that your maintenance efforts are yielding the desired results. Establishing baseline measurements for temperatures, vibrations, and other indicators before and after cleaning can help quantify the effectiveness of the process. This data can then be used to refine cleaning procedures and improve future maintenance activities.
In addition to quantitative measures, gathering feedback from maintenance personnel about the ease and effectiveness of the cleaning process can provide valuable insights. Their observations and experiences can highlight potential areas for improvement and ensure that the cleaning process is as efficient and thorough as possible.
Be proactive: Long-term maintenance and cleanliness
Ensuring long-term maintenance and cleanliness of plastics machinery requires a proactive approach. Identifying and eliminating the root causes of oil degradation is essential for extending system cleanliness and preventing future issues. Refilling with high-grade varnish-resistant oil enhances the longevity and performance of the machinery, and incorporating chemical cleaners during every oil change helps maintain system cleanliness and prevent varnish buildup. Cleaning should be conducted whenever operational evidence, such as performance degradation or visible varnish deposits, indicates the need.
Developing a comprehensive maintenance plan that includes regular inspections, oil analysis and cleaning schedules to remove varnish can significantly improve the reliability and performance of your machinery. This plan should be flexible enough to adapt to changing conditions and system requirements, ensuring that maintenance efforts remain effective over time.
Investing in high-quality lubricants and cleaners is another key factor in maintaining long-term cleanliness. While these products may have a higher upfront cost, their superior performance and longer lifespan can result in cost savings through reduced maintenance needs and extended machinery life.
Final thoughts
Proper maintenance of plastics machinery involves regular monitoring and cleaning to address varnish problems. By following best practices and using appropriate cleaning methods, you can ensure efficient and long-lasting operation of your systems. Understanding the symptoms, testing methods and effective cleaning practices helps you better manage varnish-related issues and maintain optimal performance of your plastics machinery.
Nathan Knotts is an industrial oils and grease portfolio architect at Chevron.
Nathan Knotts | Chevron
Nathan Knotts is a Portfolio Architect at Chevron, overseeing the portfolio for industrial oils and greases. With over 15 years at Chevron and a PhD in organic chemistry from the University of Missouri, Nathan is a seasoned expert in the development and management of advanced lubricant technologies. His work is pivotal in driving innovation at Chevron and in the energy sector as a whole.
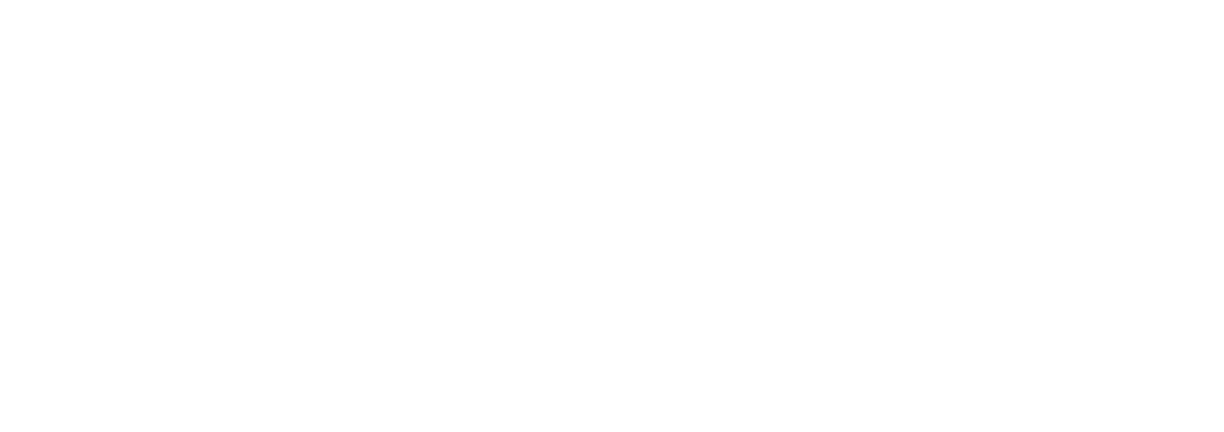