By Rick Bohan
Chagrin River Consulting
Over the years, I’ve had a number of managers say to me, “I want to implement lean methods in my plant, but I don’t know how to get started.” The answer I give them: “It’s really simple. Clean your plant up, and get it organized.”
Too many of the texts and articles that cover lean make it appear to be a complicated mix of tools and concepts: takt time, value stream mapping, kanban, heijunka, one-piece flow, single minute exchange of dies and on and on. It’s no wonder managers get confused about how to start the lean journey. The fact is that all of these methods will be more effective if your plant is clean and well-organized.
Some managers find it difficult to believe that simply cleaning up is the best way to start a lean implementation. “It can’t be that simple,” they say. “Shouldn’t we start with a value stream map or something?”
Lean is all about controlling manufacturing processes so as to eliminate or reduce variation. Simply said, variation is all the things that happen that we don’t want to happen: scrap, delays, breakdowns, lost material or product, and so on. Variation makes operators’ work harder and managers’ work more frustrating. Variation increases costs.
There are lots of sources of variation, and you’ll tackle all of them at one time or another as you implement lean manufacturing in your plant. A large source of variation (maybe the biggest) is disorganization in your plant. When your plant isn’t clean and organized:
- It’s unsafe because electric cords, air hoses, water and oil create tripping and falling hazards,
- Your operators can’t find the tools, materials and supplies they need when they need them,
- Important information and documents get lost,
- Junk and clutter increases movement and travel times,
- Operators and managers waste a lot of time looking for work-in-progress and finished goods.
- Productivity is lost when dirty equipment heats up, loses lubrication or hides maintenance problems.
All of these issues can be improved by employing the simplest lean method of all: cleaning and organizing the plant.
Workplace cleaning and organization has a number of benefits. First, it’s a good way to get all your operators and supervisors engaged. They will be doing the planning and the work needed to get to your workplace organization goals. My experience has been that operators get enthused about their role in organizing the workplace (so long as the why and how of workplace organization is communicated to them effectively.)
Second, workplace organization leads to quick, visible results. Third, the engagement by employees and the visible results lead to increased morale. Fourth, improved cleanliness and organization provides a foundation for measurable process improvements that, in turn, lead to improvements in operating performance.
Here’s the thing … though cleaning up and getting organized is simple, it’s not easy. I’ve had clients get started on that part of a lean implementation with excitement, only to abandon the effort halfway through. Why would this be the case, especially given the benefits?
Cleaning and organizing a manufacturing shop takes a good bit of patience and discipline. Most importantly, it requires ongoing time, attention and commitment on the part of the plant’s leadership team. Just sending everyone to a class on workplace organization and instructing supervisors to see that it gets carried out will not work. The plant manager will need to walk the plant floor frequently and spend time talking with operators about the workplace organization project. Supervisors and lead techs will be required to plan, schedule and lead clean-up efforts. Depending on the size and complexity of the plant, the effort will take anywhere from a couple of months to a year.
Sustaining the gains achieved takes attention as well. My clients who abandoned workplace organization initiatives didn’t find them difficult. Rather, they had underestimated the commitment of time and attention needed to make them successful and decided that the “price” was too high.
My intent is not to scare you away from the task of cleaning and organizing your workplace. Rather, it’s to help you be sure that you can commit the necessary resources to the project’s success.
So, you understand what’s going to be required of you and your colleagues and you’re ready to get started … what now? We’ll tackle that in our next article!
More on lean manufacturing
Comco and Mercury Plastics show how they've improved through cutting waste.
Lean manufacturing terms, explained.
Help is available to get smaller firms into lean manufacturing.
In-house program guides Engel through supply chain and labor challenges.
Commentary: Your workers are the key to continuous improvement.
ABB appoints chief sales officer for B&R
KraussMaffei now building extruders in U.S.
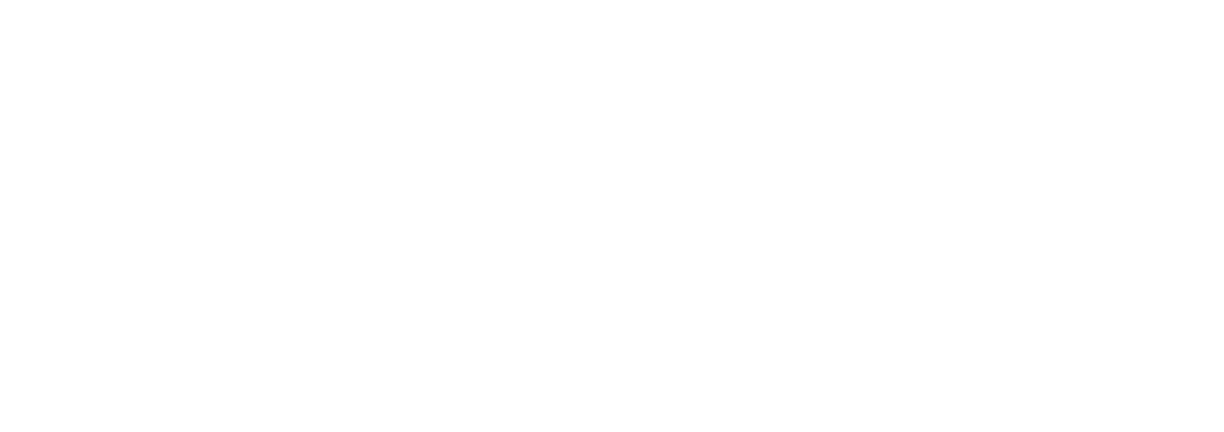