By Karen Hanna
Big or small, no matter their processes, manufacturers can benefit from lean, proponents said. Training to develop a workplace culture that embraces continuous improvement is available.
Most of his clients are small to medium-sized companies, said Henry Foppoli, a managing partner at the AMSaxum consulting firm. Some are in distress; others are just looking to improve.
Many qualify for state or provincial grants for the services offered by his Burlington, Ontario, firm, which has provided consulting about lean to more than 40 companies since its founding in 2017.
Foppoli said that many times, companies are unaware of the availability of grants, but consulting firms or government liaisons can help them identify and possibly apply for funds.
“I don’t know if it’s a lack of marketing problem of the government. They have these beautiful programs, but sometimes they don’t spend too [many] resources in advertising them,” he said.
One example of a company that’s benefited from grants is Parker Plastics, which has had to cover only half the costs of lean manufacturing training at its Hagerstown, Md., blow molding facility. It's partnered with a number of organizations for training, including Hagerstown Community College and the Maryland World Class Consortia (MWCC), a nonprofit lean consulting firm.
Over two years, Parker Plastics has gotten close to $30,000 in grants, according to plant manager Michael Genevro.
“I always let people know, to join that workforce development [agency or Chamber of Commerce] because there's lots of grant money out there,” Genevro said.
Supported by public/private partnerships as well as member dues, the MWCC offers workshops and extended trainings. Hundreds of people have graduated from its Lean Facilitator Certification Program since it launched in 2005.
In October, it will welcome the 28th cohort of its Lean Peer Group, a 12-month program, in which Parker Plastics has participated. It brings together groups of leaders from various companies and industries who are seeking to help each other brainstorm ways to make their businesses more efficient. They share problems and successes along their lean journey.
Some companies participate on an ongoing basis, said David Rizzardo, associate director of the MWCC, who co-developed the peer group program in 2012.
“I’m most impressed with the companies that are doing well, but they realize that just because you’re doing well today doesn’t mean you’re going to be doing well tomorrow,” Rizzardo said.
According to its website, the state provides reimbursement for half the cost of the 12-month program. Companies located elsewhere should check with their own states for funding help.
Karen Hanna, senior staff reporter
Contact:
AMSaxum Inc., Burlington, Ontario, 888-772-2809, www.amsaxum.com
The Maryland World Class Consortia Ltd., Joppa, Md., www.leanmaryland.com
Karen Hanna | Senior Staff Reporter
Senior Staff Reporter Karen Hanna covers injection molding, molds and tooling, processors, workforce and other topics, and writes features including In Other Words and Problem Solved for Plastics Machinery & Manufacturing, Plastics Recycling and The Journal of Blow Molding. She has more than 15 years of experience in daily and magazine journalism.
ABB appoints chief sales officer for B&R
KraussMaffei now building extruders in U.S.
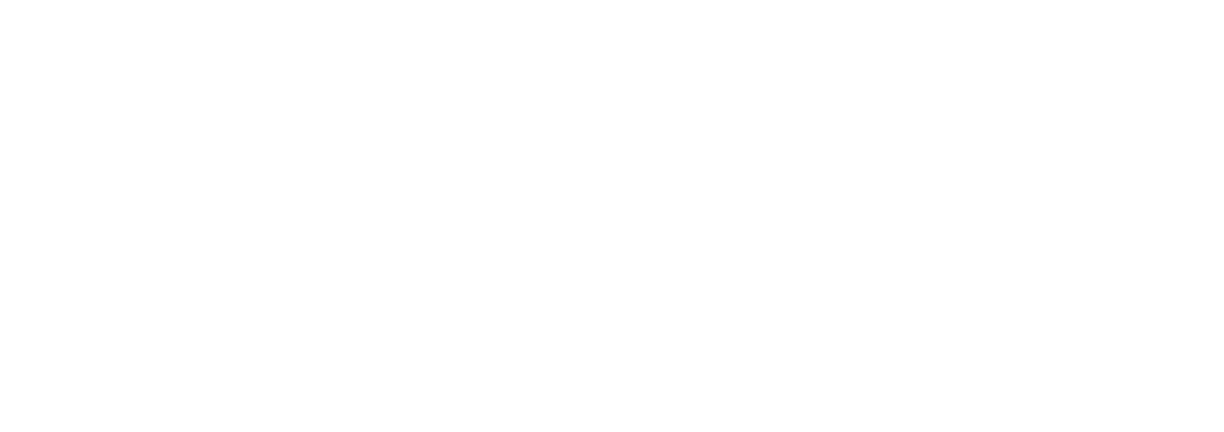