By Karen Hanna
Amid the labor shortage, one application robots seem poised to take on could be the job of selling themselves. Having employees who don’t take time off and never tire after performing the same task over time has its benefits.
Of the the 8.5 million manufacturing jobs in the U.S., 4.6 million could be automated — half with cobots — estimates Joe Campbell, senior manager of strategic marketing and applications development for Universal Robots (UR) USA. In deriving those numbers, the robot veteran has crunched statistics from the U.S. Census Bureau, the U.S. Bureau of Labor Statistics and automation maker Teradyne, along with other sources.
Multiple sources, including Campbell, reported to Plastics Machinery & Manufacturing that current demand for automation is hot — in large part because the job market remains competitive. For many plastics processors, collaborative robots (cobots) represent a practical point of entry.
According to a 2022 academic paper, “The Expanding Role of Artificial Intelligence in Collaborative Robots for Industrial Applications: A Systematic Review of Recent Works,” the U.S. cobot market was worth $1.01 billion in 2021, “and is anticipated to increase at a compound annual growth rate of 31.5 percent from 2022 to 2030.”
A record 3.5 million robots, worth an estimated $15.7 billion, were in operation last year, according to the International Federation of Robotics.
Campbell explained the demand with a real-life scenario.
“Let’s say you’re a contract molder, and you need a certain amount of labor to do the secondary operations and to pack the parts out,” Campbell said. “If you can’t hire that, you can’t run your machines. If you can’t run your machines, you’ve got a half-million-dollar investment that’s sitting there idle.”
In December 2022, more than three-quarters of employers surveyed by the National Association of Manufacturers reported they were concerned about attracting and retaining workers. That challenge ranked No. 1, higher than issues involving the supply chain, raw material costs and myriad other concerns.
As of January, the U.S. Bureau of Labor Statistics reported 803,000 openings in the manufacturing sector — down from 905,000 at the same time last year, but a moderate increase over the 797,000 openings reported in December 2022. At the same time, unemployment hit a 50-year low, at 3.4 percent.
According to statistics cited by Campbell, 2.1 million manufacturing jobs will go unfilled by 2035. Ten thousand baby boomers retire every day.
“Nobody is buying automation today to put people out of work,” Campbell said. “When I started selling robots 40 years ago, that was the model: You sold automation because the company needed to take labor out. Today, nobody can attract enough workers into manufacturing, so, the name of the game today is to put your skilled workforce into the highest-value operations.”
In some cases, automation can help manufacturers extend their shift, by finishing up tasks at night that are programmed during the day. For manufacturers that’s aren’t ready for fully lights-out production, it’s a “fairly big win,” he said.
According to Campbell, companies can see a return on investment in a year. “In many cases, it’s less than that. … It’s a really good payback, especially if you are having trouble hiring manual operators to load and unload machines.”
According to the Association for Advancing Automation (A3), North American companies set all-time records last year by ordering 44,196 robots valued at $2.38 billion.
More than 50 percent of sales came from the automotive industry, which ordered 23,807 robots, up from 16,752 in 2021.
“While the numbers of robots sold to non-automotive companies isn’t as staggering as it’s been over the last couple of years, it’s clear that companies in every industry see automation as necessary for success,” A3 President Jeff Burnstein said. “We look forward to seeing more unique and increasingly easy-to-use robots that all industries can benefit from at Automate 2023 in Detroit this May.”
Leveling up
Cobots are drawing attention from manufacturers that hadn’t previously embraced automation. They're becoming accessible — and essential to them.
“What I’ve noticed in industry is a lot of the traditional automation has always been there; now, it’s more or less trying to automate the positions that they just can’t find the labor for anymore,” said Tim Pelesky, who heads up marketing and sales enablement for integrator Onexia.
In addition to capabilities that make them easy to use, cobots boast a price that offers an attractive entry to automation, the academic report. In 2015, the average cost of a cobot was about $28,000, but that’s supposed to dip to $17,500 by 2025, the report says.
They’re appealing to automation novices.
“One of the primary factors driving growth in collaborative robots is the willingness for first-time adopters to embrace the technology,” said Chris Caldwell, product manager for Yaskawa Motoman. “Due to the additional safety considerations, many companies that are hesitant to cross into industrial robotics feel like collaborative robots are right for them.”
One market that’s largely untapped is among manufacturers with small or mid-sized shops. Those processors have been traditionally ignored as robot suppliers have focused on companies with deeper pockets, Campbell said.
But UR and other companies see potential in that demographic.
“It’s a huge market that we’re barely scratching the surface on. About 90 percent of the businesses, the manufacturing companies in the U.S., are less than 100 employees. I can tell you having sold automation for decades, that’s not a high-priority sales target,” Campbell said.
Good colleagues
Rather than replacing people, cobots are making their jobs better, in addition to helping the companies that employ them, automation experts say.
“It opens up the world for the people that are showing up to go to a more value-added position. And also it helps just get product out the door more efficiently,” Onexia’s Pelesky said.
By doing dirty, dangerous and dull jobs, cobots improve the quality of life for their human counterparts. According to statistics cited by UR’s Campbell, 70 percent of workers believe automation will create opportunities for them to do higher-level work.
“Companies may grow exponentially and automate various manufacturing processes with the aid of cobots, which also makes extra space available for working remotely. By taking over undesirable duties, they also increase worker safety,” the academic report says.
In a tight job market, both employers and employees see the benefits.
Overall, robot suppliers say, business is brisk. Kristian Hulgard, GM of the Americas for OnRobot, characterizes it as “hot.” Demand for palletizing automation, in particular, is at a “fever pitch,” Pelesky said.
“When cobots started, everyone was always saying, ‘Oh, this is going to take a lot of jobs from us.’ The fact is today, there’s nobody who wants to take those jobs, and now we’re trying to create more jobs by installing more robots,” Hulgard said.
Karen Hanna, senior staff reporter
Contact:
Association for Advancing Automation, Ann Arbor, Mich., 734-994-6088, www.automate.org
International Federation of Robotics, Frankfurt, Germany, 49-69-6603-1697, https://ifr.org
Onexia Inc., Exton, Pa., 610-431-7271, www.onexia.com
OnRobot, Odense, Denmark, https://en.onrobot.info
Universal Robots USA Inc., Ann Arbor, Mich., 844-462-6268,
www.universal-robots.com
Yaskawa America Inc., Motoman Robotics Division, Miamisburg, Ohio,
937-847-6200, www.motoman.com
Karen Hanna | Senior Staff Reporter
Senior Staff Reporter Karen Hanna covers injection molding, molds and tooling, processors, workforce and other topics, and writes features including In Other Words and Problem Solved for Plastics Machinery & Manufacturing, Plastics Recycling and The Journal of Blow Molding. She has more than 15 years of experience in daily and magazine journalism.
Related
What's a cobot?
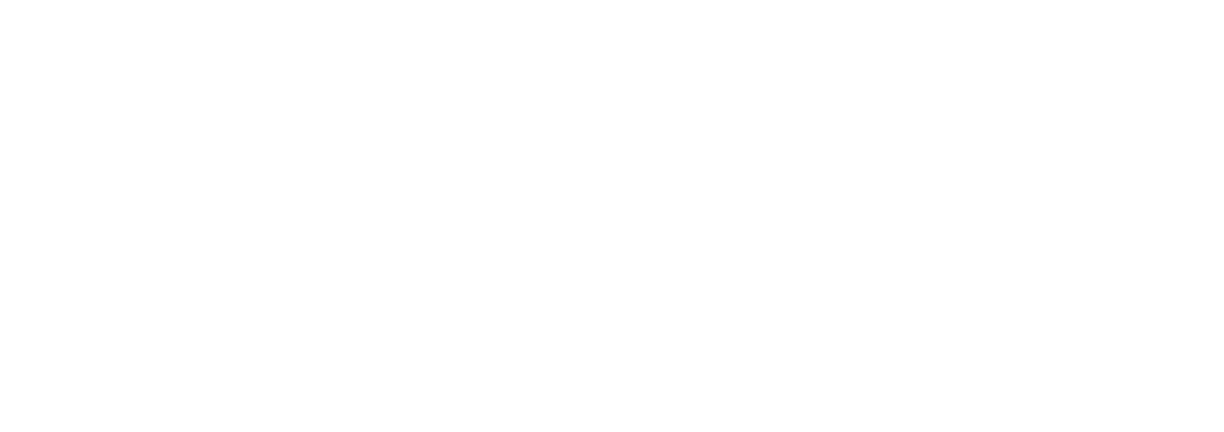