By Troy Tepp
Sentry Insurance
Mounting supply chain challenges have changed day-to-day operations for most businesses. Compounded with other emerging obstacles, such as the rising prices of petroleum and resin, plastics manufacturers are in a uniquely precarious position.
These issues complicate everything else, including recovery from significant emergencies such as cyberattacks, extreme weather and especially equipment malfunction. Lack of preparation for such incidents can increase your recovery time and risk of business closure.
Given today’s challenges, recovery strategies you’ve identified in the past may not be as reliable as you expect. Now is the time to evaluate your emergency response and business continuity plans.
Proactive planning can help ensure that you’re not left scrambling among other market threats if an emergency occurs. As a director of safety services with Sentry Insurance, my team and I have compiled some recommendations to help businesses like yours reassess your business recovery plans, so you can resume operations as quickly as possible.
Planning for emergencies in plastics manufacturing
Business continuity plans outline what steps can help you recover and resume operations if an emergency occurs. These recovery plans are not the same as your emergency response procedures, which guide your immediate response to such incidents, keeping your team safe from imminent danger.
However, continuity planning should begin with emergency preparedness. Start by defining and gauging the extent and scope of potential incidents. Consider the severity of each potential threat — critical, serious, average and secondary. This can help you focus on developing and planning strategies to address the most serious risks to your business. Some of the biggest risks plastics manufacturers routinely face include:
- Chemical hazards and related medical emergencies
- Injuries caused by manufacturing equipment
- Machinery and equipment failure
- Cybersecurity breaches and data system crashes
- Extreme weather events, such as tornadoes, hurricanes, earthquakes, flooding and fires
Looking at this list, it’s easy to see how almost any of these risks could harm both your employees and your key operating equipment.
While the immediate safety of your teammates and anyone else on site should be the top priority for emergency response planning, you must also identify strategies to protect your equipment and business operations. As you know, downtime can cost you revenue and create additional expenses for your business — particularly if you need to purchase new equipment. Supply chain issues can mean delays in getting crucial new equipment or replacement parts, increasing that downtime.
Protecting your equipment and business operations
Your business continuity plan should include ways to secure electronic information, protect or recover facilities, and perhaps most importantly, protect your physical assets — particularly equipment that is fundamental to your operation. For plastic manufacturers, such equipment may include:
- Mechanical equipment such as air compressors, pumps, gears, engines, molds and die sets.
- Electrical equipment, including motors, generators, transformers, servo drives, switchboards, distribution systems, programmable logic controllers, computers and communications equipment.
- Production equipment like injection molding machines, extruders, blow molding machines, blenders, thermoformers, robotics, thermal transfer printers and packaging equipment.
When equipment failure hits you, it can result in expensive repairs and productivity losses. Though you may have identified equipment-related recovery strategies in the past, reassess those strategies, keeping in mind today’s supply chain challenges, to help you get back up and running with minimal disruption.
Insurance partners may be able to help you assess exactly what you’ll need to protect or recover equipment specific to your operation. If you’re working with a partner, make sure you discuss the following questions as you begin creating a new continuity plan:
- Where will we purchase new equipment? You likely have a preferred vendor for your business’s key equipment — but their stock may be limited, or shipping delayed. Customized or highly specialized equipment may be even more difficult to source now than it was two years ago. Identify new or backup vendors for all necessary equipment. Inquire about lead times and delivery schedules to help ensure you can rely on them in an emergency.
- Can we conduct business from an alternate location? Whether damage to your equipment or your facility itself makes it impossible to continue operations in your facility, you’ll need to identify another location — at least temporarily. If key equipment is down and it will be some time before you can go back into full production, consider your options for outsourcing. While engaging other businesses — even your competitors — to manufacture or process materials for you isn’t a good long-term strategy, it can help bridge the gap between your emergency and resuming regular operations.
- Do we have the right insurance coverage in place? Insurance is meant to help mitigate losses and provide the financial support you need to recover quickly from an emergency. You should ensure you have the right coverage levels and policies in place for damage to specialized equipment, as opposed to things like windows and roofing materials that are easily sourced. Remember the initial damage to part of a facility from fire or lightning can be far less impactful than the mechanical failures caused by an electrical surge. Consider other policies that may better protect your equipment, like equipment breakdown coverage. Also, plan for other business concerns with policies like business income insurance, general liability and workers’ compensation plans. Remember, while insurance can offer some protection, the speed of your business recovery is key to ensuring your operation remains profitable — and in business.
Identifying solutions to these questions can help mitigate losses related to your equipment, minimize downtime in your operation and protect your business continuity after an emergency.
Keeping your continuity plan up to date
Continuity planning is always more successful when you’re continually planning. Today’s challenges make it especially important to increase the frequency with which you should re-evaluate your plan. While planning your new recovery strategies is the critical first step, remember to stay vigilant as the industry evolves. To stay engaged with your recovery approach:
- Revisit your recovery strategies monthly. Ensure they’re relevant and that you can rely on the resources you’ve identified in your plan (including your material suppliers, equipment vendors and backup site resources).
- Practice your plan and update it when necessary. Train employees to understand their roles and reduce the risk of miscommunication by including public relations and employee and customer communications in your plan. Prepare inventory and equipment checklists, and account for data backups and potential backup sites.
- Determine your critical business operations and prioritize their recovery. Remember that these may change as your business evolves to meet customer needs and confront supply chain challenges. Use an impact analysis worksheet to help assess which operations will have the biggest effect on your business, and which equipment is most critical to protect or replace in an emergency.
- Stay connected with your insurance provider. Maintain the insurance policies you need. That may include business interruption, equipment breakdown coverage, commercial property, liability or even key person insurance. Partner with your insurance provider and regularly review your coverage levels to support current recovery costs.
More downtime equals a longer road to recovery and, most likely, more significant damage done to your business. Effective emergency plans can help protect your employees, but remaining in business as a profitable employer depends on protecting your equipment as well.
Now is the time to plan for today’s plastics supply chain challenges and the impact they may have on your business continuity as market conditions evolve. Take the first step by speaking to your local expert about the latest guidance for continuity planning in your area. Making a well-considered recovery plan can make all the difference in a successful recovery.
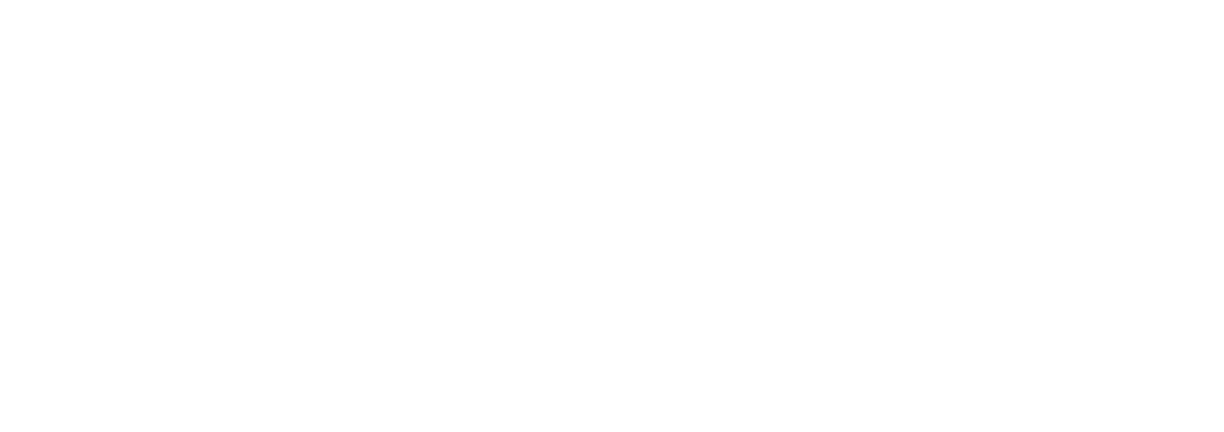