Pandemic, worker shortage fuel interest in smart factory software
By Bruce Geiselman
Smart factories, the industrial internet of things (IoT), Industry 4.0, digital transformation — these are terms that are used to describe the concept of optimizing manufacturing operations by connecting machinery, equipment and computer software to continuously collect, share and interoperate using digital information.
In many cases, software employing artificial intelligence and machine learning can help factories optimize their operations by running more efficiently, reducing scrap and minimizing unplanned downtime.
Recent challenges from the COVID-19 pandemic, coupled with a worker shortage and supply chain disruptions, have fueled adoption of smart factory technologies, according to executives with Oden Technologies and DelmiaWorks, which offer smart factory software.
Oden connects the factory floor
The co-founder and CEO of Oden Technologies, which offers cloud-based industrial automation and analytics software, says increasing numbers of manufacturers and plastics processors are adopting smart factory technologies.
“Not all of them are, but there are plenty of them that are adopting it at an accelerated rate,” Willem Sundblad said. “Every new technology goes through an adoption cycle, and I think that we are past the point of early adopters. We’re now in what I would say is the early majority, but you always have a significant amount of laggards as well.”
Sundblad sees a correlation between the size of a manufacturer as measured by revenue and its adoption of smart factory technologies.
“The bigger the company, the more they’ve started adopting smart factory and Industry 4.0 technologies,” Sundblad said.
The smaller companies, where “they have a much bigger hurdle to jump,” are less likely to have embraced smart factory technologies, he said.
“In the beginning, we started serving more smaller players but found that we had much more of a pull from the bigger kind of enterprise customers,” Sundblad said. “I think it is a combination of factors. Small manufacturers have less resources, but they also might be serving a specific niche with less competitive pressure, whereas the larger manufacturers have more resources. Generally, manufacturers spend 2 percent to 3 percent of their revenue on IT and technology. That ends up being a lot more dollars going to the bigger ones.”
In addition, larger manufacturers might be facing more global competition, and competition drives smart factory adoption, Sundblad said.
Another recent factor motivating investment in smart factory technologies is an increased demand for products, so manufacturers need to rapidly increase their capacity and output.
“You can do that much faster with digital technologies than you can by just adding factories or adding production lines,” Sundblad said. “A lot of our customers are seeing an incredible increase in demand, whether they’re serving the packaging industry or the building and construction industry. There are a lot of industries where demand outstrips supply right now. … Deglobalization is starting to happen where more goods are being manufactured here. Demand is increasing in the U.S. because of supply chain issues and an increase in costs of transportation.”
The shrinking workforce has also affected adoption of the technology.
“I think this is the one that manufacturers are facing most acutely right now,” Sundblad said. “Digital technologies really hit on the workforce in multiple ways. There are the core automation technologies that just help you make things with fewer people. But the type of technologies that we do, we help customers find and solve problems faster. That means that all the individuals that they have, be it engineers or operators, they can be more effective with their time, which, again, means they need fewer people.”
With the workforce shortage and the skills gap, he said, companies “will not be able to hire themselves out of it. They will only be able to invest themselves out of it. I think that is really the biggest catalyst of all these digital investments now.”
Smart factory technology helps automate many tasks to make it simpler for people to do their jobs, Sundblad said.
Oden’s industrial IoT platform connects numerous sources on a factory floor, including enterprise resource planning (ERP) and manufacturing execution system) software or an open platform communications server, and collects their data.
“We make that [data] useful, accessible and accurate for the users,” Sundblad said. “In the past, if a process engineer wanted to solve a quality issue, it might take them three hours to manually go to those data sources, download the data, put it into Excel and then try to figure out what actually happened. Now, they can do that in 10 seconds instead.”
In addition, Oden’s platform incorporates a machine learning model capable of predicting the quality of manufactured parts.
“In most manufacturing processes, you can’t know in real time whether what you are making is good or bad,” Sundblad said. “You have to take a sample, run it into a lab, and you’ll find out hours later if it was good or bad. What we do with that data is we build a machine learning model that can both model the whole process itself and create a real-time predicted quality score of that offline quality test. With 98 percent accuracy, we can say, ‘This is what that offline quality test will tell you about this product five hours from now when you test it.’ That, of course, allows the manufacturer to know that they are making good products, but it also allows them to tune the process in real time in order to make more.”
For example, to predict the quality of extruded parts, the Oden software might look at line speed, the temperature profile, the melt pressure in the extruder, motor load and motor RPM. That way, manufacturers can tweak those variables and increase their output by 5 percent to 10 percent just by having the information in real time rather than after the fact, Sundblad said.
“You’re giving people access to new tools that they didn’t have access to before that is built on machine learning intelligence that allows them to make better decisions and take better actions in real time,” Sundblad said.
Oden software also can help companies identify opportunities to increase performance, reduce scrap rates and improve their utilization of equipment, Sundblad said.
“It really is software that allows people to see how they’re doing and how they can find the best actions to take to improve how they’re doing,” Sundblad said.
DelmiaWorks helps fill labor gap
DelmiaWorks (formerly IQMS) sells enterprise resource planning software, which provides predictive maintenance software tools for real-time production and process monitoring. The software leverages data from existing PLCs on production equipment, as well as additional sensors that can be installed by customers.
The pandemic pushed manufacturers to minimize the number of workers on the floor for worker health, DelmiaWorks CMO Steve Bieszczat said.
“It used to be, ‘Well, I don’t want a bunch of people [on the plant floor] because I don’t want to pay them,’ and now it became, ‘I don't want a bunch of people there because I can’t have them there,’ which was augmented by, ‘I can’t have a bunch of people there because I can’t find a bunch of people to be there because of the workforce shortage,’ ” he said.
“We saw a pretty dramatic increase in the number of people using the part of the equation that we supply, which is the automatic production monitoring and reporting and process monitoring and reporting because they could, instead of having an operator at a machine keeping an eye on things, they could have basically a computer at the machine keeping an eye on things.”
Challenges particularly arise when high worker turnover, like industry has experienced in recent years, is coupled with frequent product changeovers, Bieszczat said. Normally, with shorter production runs and more frequent changeovers, automation becomes less practical, he said.
“It’s an inverse curve; the shorter the job, the less practical automation is and the more you need to use people,” Bieszczat said. “People need to know what to do and how to do it and when to do it, and that’s where Shopworks comes in.”
Shopworks is the latest module for DelmiaWorks, and managers can use it to set up a digital to-do list for individual workers. Shopworks can guide them step by step through the tasks they need to accomplish, such as during changeovers.
“It’s a guided workflow for a worker to do this, do that, stop, measure this, take these next steps,” Bieszczat said. “It’s the human instruction panel, if you will, at the machine for what to do, when to do it and how to do it. In the short run, that’s where Shopworks really comes into play. Its point is to sort of semi-automate the human actors.”
DelmiaWorks now is working on the next steps in the manufacturing process — what to do with the part once it’s made.
“The next phase in the production process is generally some sort of assembly,” Bieszczat said. “So, the next extension to Shopworks, which is called Assemblyworks, is the next product in that family.”
When it is introduced, it will offer guidance for assembly tasks and the tracking of the assembly process, Bieszczat said. He said it could come out “in the next year or so.”
Bruce Geiselman, senior staff reporter
Contact information:
DelmiaWorks, Paso Robles, Calif., 805-227-1122, www.3ds.com/delmiaworks
Oden Technologies Ltd., New York, 800-230-9063, https://oden.io
Bruce Geiselman
Senior Staff Reporter Bruce Geiselman covers extrusion, blow molding, additive manufacturing, automation and end markets including automotive and packaging. He also writes features, including In Other Words and Problem Solved, for Plastics Machinery & Manufacturing, Plastics Recycling and The Journal of Blow Molding. He has extensive experience in daily and magazine journalism.
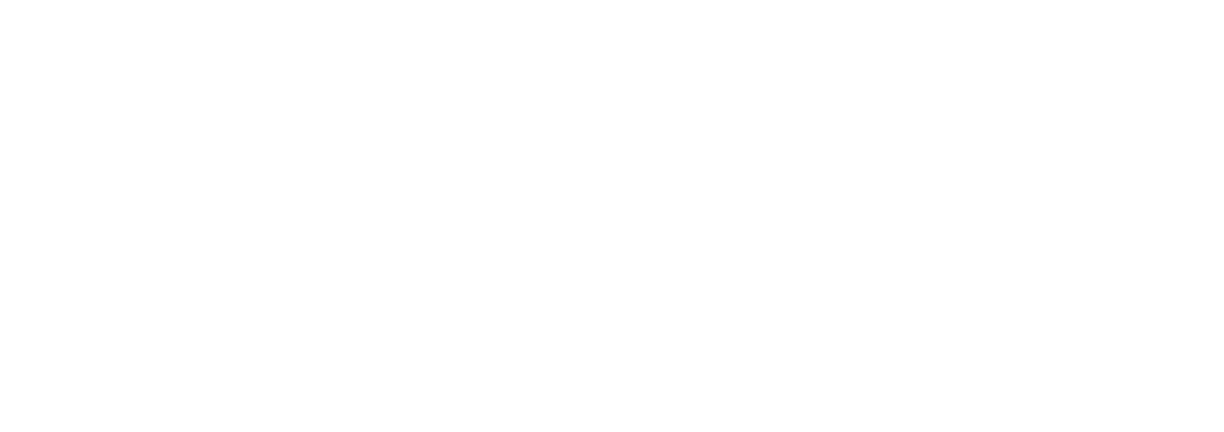