By Karen Hanna
It might have been dust that collected too close to a heat source. Or oily rags left near a hydraulic motor. Maybe an electrical panel was overloaded.
Whatever the cause, whether it was because a maintenance position went unfilled, or someone was out sick with COVID-19, no one was around to prevent the disaster that followed: Fire — the No. 1 cause of supply chain disruptions last year, for the third year in a row.
According to a January press release from Resilinc, a subscription service that tracks supply chain disruptions, “2021 saw the most factory fires [it] ever recorded in a single year." In an effort to warn its clients of events that could affect them or their suppliers or customers, the company sent out 1,946 Factory Fire alerts — an increase of 129 percent over the previous year.
Of all the fires, 288 were bad enough to trigger a service Resillinc calls its WarRoom — virtual platforms in the dashboard available to clients where they and their suppliers can collaborate to assess and resolve supply chain issues. In all, 1,252 alerts involved businesses engaged in manufacturing — an increase of 90 percent over the previous year.
In its press release, Resilinc blames “gaps in regulatory and process execution, as well as a shortage of skilled labor in warehouses.”
The supply chain hit by the most fires was the automotive industry, which, before the pandemic, would experience 200 or 300 fires a year, Resilinc co-founder and CEO Bindiya Vakil said. Last year, 1,268 alerts went out, about three times as many as the 468 triggered in 2019, the year before the pandemic struck worldwide.
In the last 18 months or so, at least three fires have caused outages at plants engaged in manufacturing semiconductors — key components at the center of shortages that have hobbled the automotive industry.
While the outbreak in fires isn’t a direct result of the virus’ spread, Vakil argues the two situations are no coincidence.
“That is what we looked at, is why so many factory fires? Because people are not doing the preventive maintenance. Factories need to be kept clean, free of debris near the hot work areas,” she said. “There needs to be constant inspection of the electrical systems and machinery and things like that, so this is one of those things that’s the outcome of COVID.”
Vakil isn’t the only supply chain expert taking note of the pressures on plant maintenance.
Rapid turnover and labor shortages have created challenges for companies to bring new workers up to speed, observed Jade Rodysill, EY Americas chemicals and advanced materials industry leader, who spoke before Christmas about vulnerabilities in the automotive supply chain.
“If you think about standard work in a plant … you think about a good, sound maintenance practice. Those are still very important things to have, particularly as you have such high turnover in your plant, with a whole new set of people coming in. They do not know why you do what you do, or why you do it the way you do. Don’t infer that. You’re going to have to train them. You’re going to have to bring them up to speed; you have to build competency faster,” he said.
Vakil concedes that the connection between maintenance, COVID-19, fires and the supply chain isn’t immediately obvious. The number of fires has surprised her, too.
But that is why she believes companies need to pry into the details of what is going on with their suppliers and sourcing locations — the sooner they learn of an event, the sooner they can respond.
“A lot of times in our industry people even in procurement don’t realize that this shortage that they’re working on today, [the reason] why a supplier just decommitted some deliveries, was because of a factory fire that happened three months ago, either to that supplier or one of their suppliers,” she said.
Karen Hanna, senior staff reporter
Contact:
EY Americas, Dallas, www.ey.com/en_us/chemicals
Resilinc Corp., Milpitas, Calif., 408-883-8053, www.resilinc.com
Resilinc Corp. fire alerts
2019 | 2020 | 2021 | ||||
Number of factory fires | 468 | 753 | 1,268 |
ABB appoints chief sales officer for B&R
KraussMaffei now building extruders in U.S.
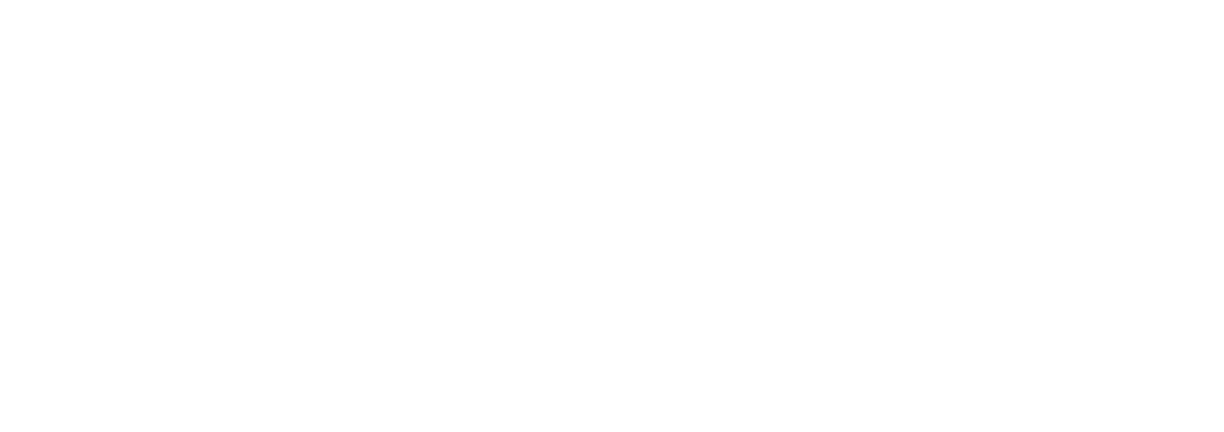