By Karen Hanna
A quest for continuous improvement spurred one worker at D&M Plastics to ask a question that’s led to tens of thousands of dollars in savings for the Burlington, Ill., injection molder.
Having heard that the area’s electric provider offered subsidies for energy-consumption improvements, the worker volunteered to look into programs to replace the plant’s halogen bulbs with LEDs.
“He got the electrical company to come in and do the study. We figured out what our savings could be. I think we had to spend about $20,000 to replace all the lights. It reduced our electricity [use] by about $20,000 a year, and we got a rebate of about 50 percent of what we spent from the electric company,” company CEO and president Peyton “Chip” Owen said of the clerk, now the manufacturing manager at the 53-employee plant.
In the plant’s commitment to going lean, Owen has found that the approach can go hand in hand with another goal: going green.
He and employees have seen lean’s benefits across the board.
“I view lean as totally and completely sustainable because you are eliminating waste,” Owen said.
Collateral benefits
Environmental improvements can be a side benefit of lean manufacturing, advocates say.
Kurt Middelkoop, a senior sustainability and lean adviser for the Texas Manufacturing Assistance Center (TMAC), which provides consulting services, sees sustainability this way:
“Basically, it’s the balance of how a business can make money, how it should take care of its people, and, while you’re doing that, also look at the impact you have on the environment.”
But lean manufacturing doesn’t explicitly target environmental waste; rather, the U.S. Environmental Agency characterizes environmental benefits as “riding on the coattails” of lean’s other goals. Traditionally, the approach targets seven specific kinds of waste, also known as muda: wasted movement of parts or materials, wasted movement of people or equipment, inadequate or excessive inventory, unnecessary waiting, overproduction, overprocessing and production of bad parts.
“Lean’s focus on eliminating non-value added activity is excellent at driving down the volume of material, water, energy, chemical usage and wastes, producing important competitiveness and environmental benefits,” the EPA says in a toolkit for companies looking to use lean to go green.
Sustainability is increasingly important to clients, said Vera Adam-Groetschel, who leads environmental, social and governance (ESG) initiatives at the Kaizen Institute, which provides lean consulting services.
Strong regulations in Europe and parts of the U.S., including California, mean that there’s a lot of green — as in dollars and cents — at stake in going green.
Speaking less than two weeks after the presidential election of Donald Trump, who has derided ESG investments, Adam-Groetschel expressed confidence companies won’t be turning back.
“When we think B2B suppliers, we as a supplier see that the pressure from our customers as companies is getting higher because they have to report on the supply chain,” she said. “The supply chain has to be more sustainable. And that is becoming a global thing.”
Start from Square 1
But Owen wasn’t concerned with sustainability when he began looking into lean. Instead, he was just hoping to figure out the ins and outs of manufacturing.
Thirty years into a distinguished commercial real-estate career, he couldn’t help but hearken back to a notion instilled in him by his father: “In order for America to be great, it has to make things.”
But, beyond majoring in engineering in college, he didn’t know anything about making things. In 2011, as he commuted between New York City, where he worked, and Chicago, he just wanted to move home.
He looked into manufacturing facilities and even sawmills, eventually buying D&M Plastics, which is just west of Chicago, in 2013.
A conference sponsored by the Manufacturers Association for Plastic Processors (MAPP) provided an introduction to his new reality. There, he saw a presentation by a lean manufacturing advocate that has influenced his company’s culture ever since.
“I didn’t know anything about injection molding. I knew a lot about running businesses, and I knew a lot about financial matters, but didn’t really know anything about manufacturing,” he recalled.
Needing a change
As a supplier of medical and electronics parts with an average weight of 50 grams, D&M Plastics has little margin for error.
However, prior to 2013, before Owen began sharing the lean manufacturing principles he was learning, it was accustomed to waste.
Parts falling from injection molding machines (IMMs) would bounce out of containers and skitter across the floor. After that, they had to be thrown out.
Lori Cobb, who in 34 years at the plant has moved up from operator to senior quality engineer, said a big change Owen brought to the job was his persistence in seeking input and suggestions from the entire workforce.
Realizing he wanted to learn and improve alongside the workers was refreshing.
Previously, Cobb said, “It was just a job, to raise my kids and move them on, and then I could grow and find something else.”
Now, her input matters, meaning, “Each day is different. You see the same people, but each day is just different with what you do.”
A focus on waste
According to Middelkoop, who has worked with numerous plastics processors over 28 years as a lean consultant, the journey toward greater efficiency can mean cutting scrap, eliminating risks of accidents or even eliminating overtime.
He cited several examples of the overlap between going lean and going green.
“We show companies how a single lean waste like scrap will also impact energy usage, waste disposal, increase safety risks, increase labor costs and facility overhead costs. Instead of thinking about lean in a silo, we teach companies to wholistically look at their process and determine where value- and non-value-added tasks are occurring,” he said.
In some cases, a drive to greater efficiency can curb the number of hours a plant has to operate, saving energy.
“When a company is efficiently doing things and turning the product quickly, they are able to get their work done during the work week. Companies that are not lean ... they’ll come in on a Saturday. ... Now, you have to turn on the entire building, so now you’ve got an environmental impact of a half a day or a whole day where you’ve got the whole building on,” he said.
Overtime also means more people commuting and creating emissions.
Some molders take solace in knowing they recycle their scrap. But that shouldn’t be the goal because any scrap — even a tiny percentage — is detrimental.
Middelkoop doesn’t look at scrap as just the cost of doing business.
“People will say, ‘Well, Kurt, that’s the industry average.’ I’m like, ‘That’s not what you need to be saying. Your goal was to have zero.’
“Because when you generate the grinds, that plastic bead now has the labor of you collecting it, moving it over to the other area, shoving it into the grinder, spending money on that gigantic motor ... and also it’s a maintenance nightmare. It’s a loud thing. ... It can generate dust. ... It’s a safety risk. ... Then, they may have to dry it, weigh it and measure it.”
All that amounts to extra labor, as well as energy costs and the risk of releasing contaminants.
Instead, Middelkoop said, “Lean says: Work on why you’re generating the waste.”
Bringing lean to life
Since Jan. 14, 2014, each of D&M Plastics’ three shifts has begun or ended with a short meeting to do just that: eliminate waste and get better.
Managers share operations data, including the volume of parts and revenue produced the previous day, as well as the goals for the current shift, and encourage workers to make any suggestions, big or small, that could help them perform their jobs. They even talk about how lean has helped them improve at home. People provide updates on the jobs running on each of the company’s 24 IMMs.
Missed shipments and safety concerns are rare — perhaps because those topics also are discussed every day. The last lost-time accident was more than seven years ago.
Huddles typically take less than 15 minutes.
“It’s very simple, it’s very fast, it’s very fun,” Owen said.
The company practices profit sharing, and Owen says he gets satisfaction from handing out checks when business is good. He said he believes it’s the right way to interact with his employees, “because I view them as owners of my business — or not my business, they’re owners of our business.”
At each huddle, managers share with employees the previous shift’s lean ideas, and everyone chips in to make them better. They record them on a whiteboard, then file away each of them in a log that now includes around 20,000 suggestions.
“We get a chance to speak with management on first shift, and they get an idea of what goes on on the floor, and ideas from the people who are working on the floor, how to improve the process around the plant,” said second-shift foreman Kyle Bellon, who in just a few months on the job has embraced the culture.
“It has potential to improve a lot of things,” he said. “I think it helps everybody improve.”
The D&M Plastics teams wrap up lean huddles with inspirational quotes or music. Owen attends two huddles a day, with the shifts alternating between end-of-shift meetings and beginning-of-shift meetings, so that, over a period of weeks, he’s able to interact with all the plant’s workers.
Often, he shares something for which he’s grateful. It isn’t difficult to solicit an example, as an hourlong discussion produced repeated praise for his employees:
“These are people that are operators, materials handlers, maintenance guys ... these are guys that are on the floor every single day. They know more about what’s going on than I ever will. And their ideas have a lot of value,” he said. “Because ... they do something I can’t do.”
Lean leads to sustainability
Lean ideas can run the gamut, but many of them have implications for sustainability.
At D&M Plastics, one major source of both environmental and financial savings has been the professional prowess of the plant’s maintenance staff, as those employees are able to keep pieces of equipment running that other plants might retire.
For Owen, that represents “the ultimate in sustainability.”
As an example, he said, “Rather than going out and buying a new pump, they will tear the pump apart, replace all the seals, put it back together, and it runs like it was brand-new.”
At 40 years old, the cooling tower attests to maintenance employees’ skills.
“It’s outlived its life by at least 20 years. Our guys continue to find ways to keep it alive,” Owen said.
The plant also has addressed a problem that used to bother Cobb before Owen came along — those parts that had to be trashed after hitting the floor.
To prevent that from happening, Cobb said the plant has installed curtains that guide the parts from the IMMs to catch trays.
She said the plant also is trying to reduce the amount of paper it consumes, using computers instead to better manage information, including increasingly robust procedures for the processes workers perform.
In addition to better containing parts, Bellon said the company is exploring whether to regrind scrap parts.
“There’s definitely been a lot of other discussions,” he said. “Whether it be reducing the amount of energy or ... finding a better way to do things.”
Current scrap rates stand at 1.1 percent, and some weeks, the plant produces less than $100 worth of scrap parts, according to Owen.
The TMAC’s efforts illustrate what’s possible at other plants. Over 19 years, it has trained 1,881 people and delivered on-site assessments to 173 manufacturers to identify lean, energy and environmental improvement projects, resulting in over $40 million in savings. Its recommendations have led to reductions in consumption of more than 91 million kilowatt-hours and more than 24 million gallons of water. It’s also helped clients lower their production of more than 49,000 tons of carbon and over 30,000 tons of solid waste.
Funded by a public-private partnership, the TMAC works within Texas and with partners in bordering states. It is part of the national Hollings Manufacturing Extension Partnership (MEP), based at the National Institute of Standards and Technology, with services available throughout the country.
Still room to improve
Eleven years after attending his first MAPP conference, Owen’s still looking at ways to get better — a mindset that he thinks benefits everyone.
“How do I put this? It benefits our customers, because we’re able to be more competitive. I don’t know that we necessarily make a lot more money. We’re never the cheapest, and we’re never going to be the cheapest, but we’re never the most expensive,” he said. “And when it comes to producing high-quality parts at a competitive price, we’re always competitive. We’re never not competitive. And I think it’s that whole dedication to lean that is enabling us to do that.”
For him and other lean advocates, sustainability is just a natural part of that success story.
Lean and green just go together.
“You do lean because you want to be more efficient in everything you do,” Owen said. “You want to eliminate waste in your business, so that’s one of the reasons why you do lean. I also do lean because it’s the right thing to do.”
Contact:
Kaizen Institute North America, Scottsdale Ariz., 888-464-3622, https://kaizen.com/us
Manufacturing Education Partnership, Gaithersburg, Md., 301-975-2000, www.nist.gov/mep/centers
Texas Manufactuing Assistance Center (TMAC), Fort Worth, Texas, 800-625-4876, https://tmac.org
U.S. Environmental Protection Agency, www.epa.gov/sustainability/lean-manufacturing-and-environment
Karen Hanna | Senior Staff Reporter
Senior Staff Reporter Karen Hanna covers injection molding, molds and tooling, processors, workforce and other topics, and writes features including In Other Words and Problem Solved for Plastics Machinery & Manufacturing, Plastics Recycling and The Journal of Blow Molding. She has more than 15 years of experience in daily and magazine journalism.
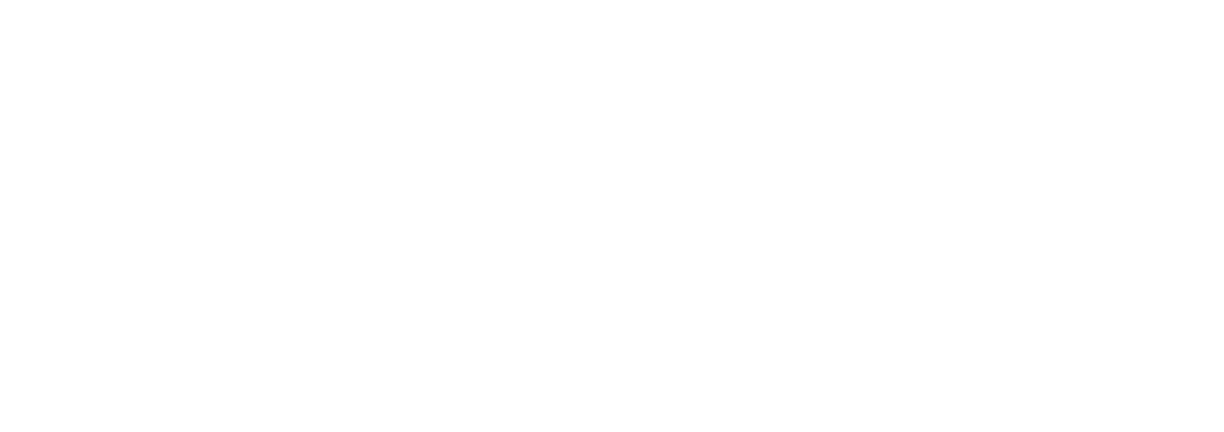