including power consumption. The software, which can be paired with Wittmann’s TEMI+ manufacturing execution system (MES), can help molders optimize their energy costs. The full version of the system, IMAGOxt, can be connected to auxiliary equipment, including chillers, compressors and dryers, to collect data from a wide range of sensors and analyze factors such as temperature, pressure, humidity, gas consumption, water consumption, distance and air quality.
What’s new? Imago Peak, described by Wittmann as a “lite” version of the company’s Imago system, which was first shown at K 2022. Designed to help users optimize their energy consumption, it reads energy-consumption data from users’ electrical meters.
Benefits More-efficient energy use. The Imago Peak system warns users when they’re approaching peak periods of energy consumption. With the system, users can make informed decisions about energy consumption, so they can better balance energy needs and loads. According to Wittmann, some manufacturers can achieve energy savings of 15-20 percent, by leveraging their Imago Peak data.
Wittmann USA Inc., Torrington, Conn., 860-496-9603, www.wittmann-group.com
Karen Hanna | Senior Staff Reporter
Senior Staff Reporter Karen Hanna covers injection molding, molds and tooling, processors, workforce and other topics, and writes features including In Other Words and Problem Solved for Plastics Machinery & Manufacturing, Plastics Recycling and The Journal of Blow Molding. She has more than 15 years of experience in daily and magazine journalism.
Request More Information
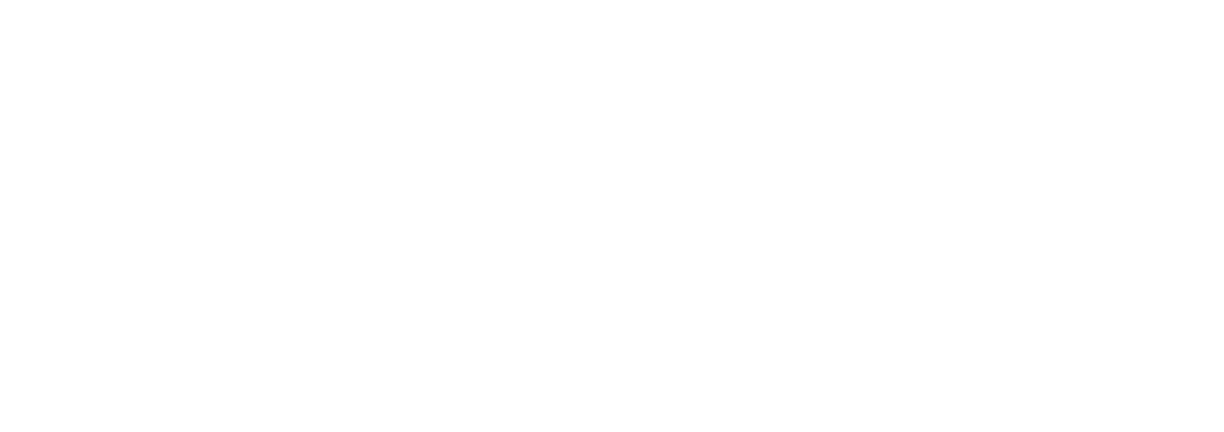