Arburg shows how digital watermarks improve the quality of recycled plastics
By Bruce Geiselman
German injection molding machine (IMM) maker Arburg demonstrated at the recent Plastec West show in Anaheim, Calif., how digital watermarking can improve the quality of plastic recycling streams.
HolyGrail 2.0 is a digital watermark pilot program adopted in the European Union by more than 160 companies and organizations involved in the packaging value chain. The goal is to determine whether digital technology can enable better sorting and higher recycling rates for packaging.
Digital watermarking has not been adopted in the U.S., but some companies and recycling advocates have expressed interest in the technology.
“It’s a development through the community in Europe, and it’s being adopted by some of the major recyclers,” said Trevor Pruden, technical engineering manager at Arburg. “They’re looking at this technology here in the U.S.”
At its booth at Plastec West, Arburg demonstrated how digital watermarks can be printed on plastic bottle caps using an Arburg Allrounder 470 A IMM with 110 tons of clamping force and an injection unit capable of producing 6.1-ounce shots. Barnes Molding Solutions provided the six-cavity hot-runner mold. The closure caps were made of K-Resin KR01 from Ineos Styrolution, a material with 70 percent recycled content.
The postage-stamp-sized watermarks were applied directly via the mold cavity surface to the molded parts.
“There is a watermark in the mold. So, the part is actually getting molded with the watermark on it,” said Juergen Giesow, VP of technology and after-sales service for Arburg. “Then, when it goes into the recycling cycle, they would be able to pick up the watermark with cameras to sort the parts for the correct materials.”
Nearly invisible to the naked eye, the watermarks appear as a fine peppering of dots. They function like a QR code or bar code and identify to the recycler what type of plastic the part consists of to allow for more accurate sorting of plastics. The goal is to recycle plastics that previously ended up in a landfill or contaminated plastic recycling streams.
“You cannot at the moment get a true, clean polypropylene, for example,” Giesow said. “When you go through the recycling cycle, you will always have some type of contamination from other plastics. This will allow you to really sort the materials into their own little families of polypropylene or polystyrene, or whatever it may be to have a clean recycled material.”
The Arburg demonstration setup also included a Priamus-brand control system from the Barnes Group that adjusted the temperature of the hot runners to compensate for variations in the properties of the pellets fed into the IMM.
“The technology we’re showing is a highly precise injection molding machine that is compensating for, shall we say, viscosity changes within the material itself,” Pruden said. “That’s the nature of what you have when you’re dealing with recyclates. You’ll have different grades of a given family, and that changes the viscosity shot to shot or across lots, and we can accommodate for that.”
Arburg’s recent adoption of a new OPC-UA Ethernet protocol allows for integration of the Priamus control system so that it can make very small changes to the temperatures inside the hot runners, Pruden said.
Precise hot-runner temperatures are particularly important when molding medical devices “where we have to have very precise and accurate control,” Pruden said.
The Priamus control system, integrated with the Arburg IMM and temperature sensors inside the molds, allowed for an extremely consistent, balanced fill across all six cavities, Pruden said.
Contact:
Arburg Inc., Rocky Hill, Conn., 860-667-6500, www.arburg.com/en
Barnes Group Inc., Bristol, Conn., 860-583-7070, www.onebarnes.com
Bruce Geiselman | Senior Staff Reporter
Senior Staff Reporter Bruce Geiselman covers extrusion, blow molding, additive manufacturing, automation and end markets including automotive and packaging. He also writes features, including In Other Words and Problem Solved, for Plastics Machinery & Manufacturing, Plastics Recycling and The Journal of Blow Molding. He has extensive experience in daily and magazine journalism.
Request More Information
PCS adds Goodway descaling systems
Husky names Balaji Suresh as COO
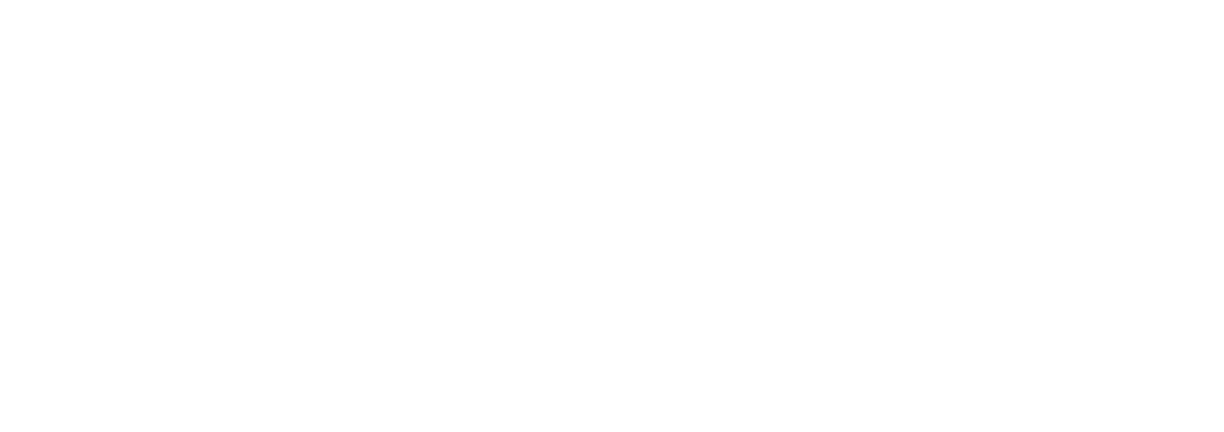