By Karen Hanna
Liquid silicone rubber (LSR) parts that weigh less than a pinch of salt are at the center of a new Engel injection molding machine (IMM) demonstration.
In a technical paper about the exhibit — which was on display at Plastec West — Engel said it’s interested in finding “the limits of what’s feasible” in micromolding.
Designed for use during eye surgery, the 0.001-gram tear duct plugs in the demonstration measure 0.9mm by 1.7mm — roughly the same length as a printed “l” in 5-point font. The company cites a new ACH plunger and injection unit for its e-motion TL-series for making the super-small size possible.
“If you have 32 cavities, the shot weight is then 0.125 grams. This is the equivalent of about 125 grains of sugar. For comparison's sake, a sugar cube contains about 20,000 to 30,000 grains,” the technical paper states.
Engel planned to demonstrate the line again at Plastics Technology Expo at the end of March, as well as at NPE 2024 next year. From May 2023 to May 2024, the cell will be available for demonstrations at the Sarasota, Fla., technical center of Engel partner ACH Solution USA, which designs and manufactures tooling and equipment for processing LSR and high-temperature vulcanized silicone rubber.
The cell’s machine employs a 6mm plunger — supplied with an injection unit from ACH Solution — that is one of the smallest on the market. It’s more robust than a comparably sized zero-compression reciprocating screw, said Chad Zediker, account manager for LSR and elastomers for Engel.
The setup relies on precise control over the metering and refilling of the plunger, said Steve Broadbent, GM of ACH Solution.
The plunger incorporates both a shut-off nozzle, which has a pressure transducer that can be monitored during refilling and injection, and a metering valve.
“This along with Engel IQ weight control [system] offers the most control for micro-injection molding on the market. The advantage over the standard reciprocating screw machine is simply the diameter; it is impossible to have [a] 6mm screw diameter and maintain the structural integrity required for an injection molding process,” Broadbent said.
Engel’s software system compares the injection pressure curve of each cycle with a previously defined reference curve. If it detects deviations, it can correct for them on the same shot by changing the switch-over point, injection profile, holding pressure profile or time, or the opening and closing of shut-off nozzles in the hot runners. Using the system reduces variances of molded part weight by up to 85 percent, Zediker said.
According to an Engel LinkedIn post, the plunger produces a maximum injection volume of 2.3 cubic centimeters — or a little less than a half a teaspoon.
At such small volumes, special care is required to ensure that the melt is uniformly and repeatably distributed over the cavities, Engel said. “The micro-injection unit, the sprue channel and thermal management are enormously important here in terms of quality, precision and repeatability,” the technical paper states.
Scaling up production of such small parts presents its own challenges, as Lilliputian deviations quickly compound.
In its technical paper, Engel says its all-electric, tie-bar-less e-motion TL series machines, such as the 35-tonner in the exhibit, offer flexibility — not only for small runs, but large runs, and for thermoplastics, as well as LSR. It boasts precision, accuracy and repeatability.
“The special features of the tie-bar-less machine solution have a positive effect in the injection molding of micro-parts. Due to their design, tie-bar-less machines in particular inherently ensure great platen parallelism and uniform clamping force distribution,” the technical paper states.
Broadbent emphasized the cell’s control and precision.
“The pressure of the A and B component are monitored independently prior to entering the mix block and static mixer, and pressure and temperature of the fully mixed compound [are] monitored in the injection unit to precisely control the back pressure applied to the plunger during metering. This means that we are not only filling to a precise position but also at a precise pressure,” he said.
Zediker said the cell represents just one of the ever-increasing number of applications for LSR micromolding.
The tear duct plugs it produces can be used to keep tears from entering the eye during surgery. Other possible parts include ear tubes for children, wearable diabetes devices and consumer electronics, including cell phone components and seals for watches.
“LSR is a material that has a number of uses and benefits based on its material properties. With the wide range of benefits of this material, there is no limit to its potential or market needs. As industry professionals continue to push the boundaries of part design, there is a growing number of applications for LSR micromolding, and with this cell we are ready for any challenge,” Zediker said.
But the cell has benefits beyond LSR, according to Broadbent and Engel.
Equipped with a quick coupling system, machines in the e-motion TL series can be converted from LSR to thermoplastic in less than 30 minutes.
“Even switching over from micro-injection molding to the production of small components with a size 15 or 18 barrel in the injection unit and a new mold is possible on one and the same machine,” the Engel technical paper states.
The flexibility sets it apart, said Broadbent, who described it as “not just a micromolding machine as offered by some of our competitors, but a complete molding machine.”
Karen Hanna, senior staff reporter
Contact:
ACH Solution USA Inc., Sarasota, Fla. 941-355-9488, www.ach-solution.at
Engel Machinery Inc., 717-764-6818, York, Pa., www.engelglobal.com
Karen Hanna | Senior Staff Reporter
Senior Staff Reporter Karen Hanna covers injection molding, molds and tooling, processors, workforce and other topics, and writes features including In Other Words and Problem Solved for Plastics Machinery & Manufacturing, Plastics Recycling and The Journal of Blow Molding. She has more than 15 years of experience in daily and magazine journalism.
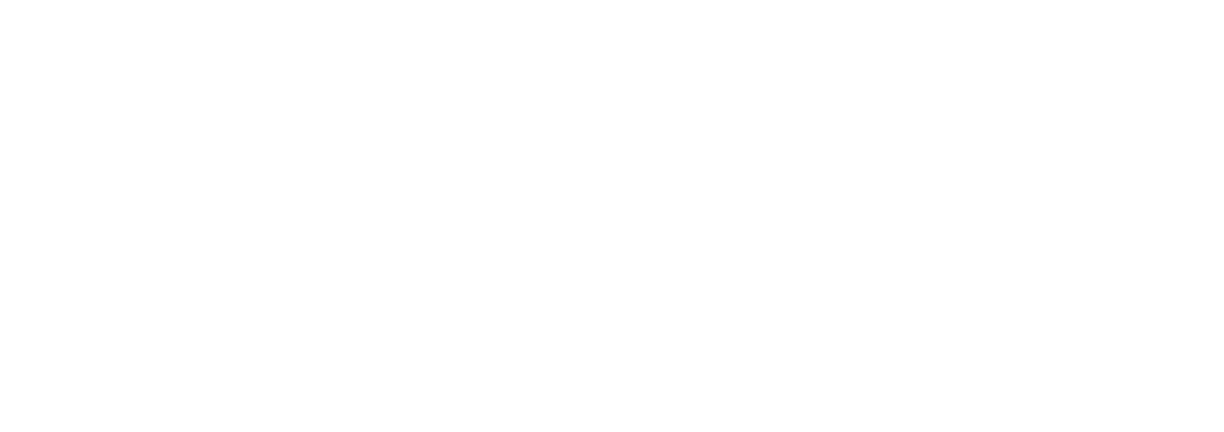