End-market diversity helps Venture Plastics thrive: On the Factory Floor
By Ron Shinn
Custom molders like to say that spreading their business across multiple end markets is the best strategy, but too often they get lured into more and more big projects in a single industry and quickly suffer when that segment slows down.
Not so with Venture Plastics Inc., which has plants in Newton Falls, Ohio, and El Paso, Texas.
Just a few years ago, Venture Plastics had about 30 percent of its total business in the automotive market. When COVID-19 and supply chain shortages slowed U.S. automotive production, that segment dropped to just 18 percent of total business.
Venture Plastics is forecasting overall record sales of about $46 million in 2023 because the automotive business it lost is being more than replaced with products for the fast-growing energy storage and standby battery market (now 38 percent of total business) and solar market (9 percent).
Alan Schultice, VP of sales and marketing, said he expects some of the automotive business to return in 2024 as automakers ramp up electric vehicle (EV) production.
“Right now, they are not redeveloping the internal combustion [cars],” Schultice said. Automakers are extending the platforms of current models while they get more EVs to production. “So now, we are in the bubble,” he said. “When it bursts, we are going to see all those new electric vehicles and those components have to be molded somewhere.”
Venture Plastics has 20 injection molding machines in Ohio and 16 in Texas. All are equipped with an integrated eDart process control system from RJG Inc.
“We practice scientific molding,” said Jim Smith, VP of operations and engineering, during a recent visit to the Ohio plant. “We segregate good and bad parts based on what we get out of the RJG system. That’s developed upfront with our process engineer.”
There also is an RJG-certified Master Molder supervisor on each of Venture Plastics’ three shifts.
“Everyone is focused on ‘this is how we need to mold,’ ” said Smith, referring to scientific molding practices and locked process.
The company applies a stringent automotive industry quality-verification program to everything it manufactures. It is called PPAP, which stands for production part-approval process. It verifies that the manufacturer has a repeatable process. “We do it as a regular way of doing business,” Schultice said. “That’s just our process. We PPAP every part.”
Venture Plastics has standardized on three molding machine brands — Nissei, Arburg and Milacron. Smith said Venture Plastics’ general practice is to get quotes from all three manufacturers when it needs a new machine. He said the company generally retires molding machines when they reach 10 years old.
Machine sizes in the Ohio plant range from 55 tons to 1,450 tons of clamping force. Presses in Texas range from 55 tons to 950 tons of clamping force.
Venture Plastics uses Yushin Cartesian robots and Nachi six-axis robots heavily throughout the plant. Temperature control units are primarily from AEC and Advantage Engineering.
A goal is to add vision products that can take more human decision-making out of the molding process.
To continue improving, Schultice said Venture Plastics management has determined it needs to add key staff. A new plant manager was hired in Texas. An automation expert recently was hired for each plant. “He is responsible for improving our current automation and moving us forward into more vision-type systems.
“Automation is where the future is going to be,” Schultice said.
A new quality manager was hired in Texas about a year ago, and a new quality manager was hired in January in Ohio.
Even with more automation and vision systems, Schultice said Venture Plastics recognizes the need for talented staff. “You still need good people in addition to deploying the right processes. You have to make sure the processes are being followed and managed,” he said. “But with today’s evolving world, I think we need to hire more people and better people.”
The Ohio plant is 62,000 square feet, and an addition of nearly 30,000 square feet is scheduled to be built this year. The addition will allow Venture Plastics to move out of a leased building next door that it uses for finished goods storage and bring everything under one roof.
The Texas plant is 61,000 square feet.
Another goal of the current staff expansion is to shift more engineering functions currently performed in Newton Falls to the El Paso staff. “We’ve added two engineers in El Paso over the past year,” Schultice said. “We are trying to have an El Paso facility that is self-sufficient.”
He said in the past, much of the engineering work has been performed in Ohio and passed to the Texas staff. “It is going to work much better if we have a self-sufficient facility down there. We are already seeing signs of improvement,” he said.
Venture Plastics managed the build of about 50 molds last year and all run internally. It does not build molds for outside customers.
Designs for tools are sent to Beaumont Technologies in Erie, Pa., for mold flow analysis, cooling analysis, gate location, warpage and molding simulation analysis. Venture Plastics also has two engineers who have completed training at Beaumont’s American Injection Molding Institute and a third engineer is scheduled to start the program this year.
A unique feature at the Ohio facility is a 110-ton tower dry cooler that was built by a local plumbing contractor. The hybrid cooling system uses dry cooling during the cooler seasons and a small wet cooling system during the warmer months when the dry system is not as effective.
For the dry cooler, heat is extracted from water in a closed system when the water passes through a plate frame heat exchanger. The cool, ambient airflow cools the water in the system. No external water is used and the water in the closed system stays clean.
A 50-ton, air-cooled chiller runs in the summer. Venture Plastics is working on an upgrade that will monitor the temperature and automatically switch the system from dry cooling to wet cooling depending on the outside temperature. Energy costs can be reduced when the dry cooler is running and the wet cooler is turned off.
The system currently must be switched manually. “We have done the studies, and it pays back pretty quickly,” Smith said.
Before the new cooling system replaced a traditional evaporative cooling system in 2013, Smith said the plant used about 1 million gallons of water each year. Now, it uses about 20,000 gallons a year.
“We were faced with replacing our chiller system back in 2012,” Smith said. “We are blessed with having plenty of water here, but I was always in the back of my mind concerned about EPA coming along and saying we were using too much water and needed to do something to reduce it.”
A central drying system is from Novatec. Material handling is via a Una-Dyn vacuum system.
The company runs an IQMS (now DelmiaWorks) ERP system.
Venture Plastics can provide overmolding, insert molding, complex part molding, decorating, plating, component assembly and welding services. It can work with most resins. The company is IATF 16949 certified. IATF 16949 is an international automotive industry standard that emphasizes the development of a process-oriented quality management system for continual improvement, defect prevention and reduction of variation and waste.
Typical parts for the standby power market are battery jars with PVC lids that are insert-molded with lead contacts. The battery containers are used in numerous applications such as solar microgrids.
Venture Plastics’ entry into the solar industry is a good example of how a mid-size or small custom molder can stick with a client until the client’s project succeeds or fails. Schultice started talking with a young entrepreneur in 2009 who designed a roof mounting rack for solar panels. The entrepreneur initially produced the racks with vacuum forming. At the time, most racks in the solar industry were metal.
By 2012, Schultice had convinced him that the racks could be injection molded, and Venture Plastics started manufacturing them. The entrepreneur eventually sold his business to Unirac Inc. in Albuquerque, N.M., and now Venture makes three different models of the rack for Unirac.
Venture Plastics’ work included helping develop a new resin grade to meet the UL 2703 requirements for solar mounting systems.
“We had enough patience with him [the entrepreneur],” Schultice said. “He pushed us to the limit a time or two, but we managed the program. There were a lot of bumps and bruises along the way, but it is now one of the most successful programs we have today. We love it.”
In addition to the standby power, automotive and solar markets, Venture Plastics makes parts for the major appliance, industrial, consumer, truck, rail,
agriculture,
fuel-delivery, food-processing and communications markets. Schultice said a goal this year is to find customers in the outdoor lighting market.
Ron Shinn, editor
rshinn@endeavorb2b.com
Just the Facts: | |
Company: | Venture Plastics Inc. |
Established: | 1969 |
Headquarters: | Newton Falls, Ohio |
Plants: | 2 |
Ownership: | Ken Groff |
Top official: | John Zelina, president and CEO |
Process: | Injection molding |
Employees: | 200 |
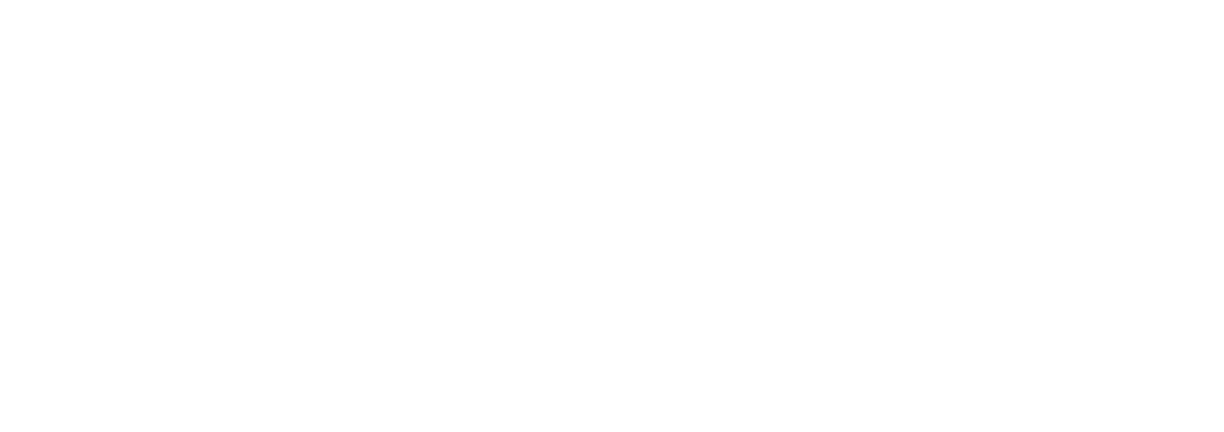