By Karen Hanna
With just days to go till the holidays, Michael Durina was looking forward to receiving an item that wouldn’t fit in any stocking or sleigh: a new 70-ton press incorporating his vision for injection molding.
“It’s sort of like ‘Field of Dreams’ where you build something, and then maybe they’ll come,” said Durina, owner of Md Plastics.
But the star of this “Field of Dreams” isn’t Kevin Costner — it’s a plasticizing system designed by Durina to ensure, he said, that “it doesn’t matter what the shot size is, every pellet sees the same shear heat [and] residence time.” Offered for years as a retrofittable system on presses available from other suppliers, the technology now has been incorporated for the first time in a purpose-built machine bearing the same name — Inject-EX.
Once Md Plastics has received and tested the machine, constructed by partner EdeX Technology Co. Ltd., New Taipei City, Taiwan, the company plans to make the presses available in a variety of sizes to molders interested in the new spin Inject-Ex puts on reciprocating-screw technology.
“The Inject-EX is basically a plunger technology, but it’s all on one axis, so we have an inner barrel and outer barrel, screw assemblies inside the inner barrels, direct connection to the screw-drive motor,” Durina said. “And on the end of that assembly is our plunger head, and the plunger head is a key to this technology because that provides instantaneous shutoff. A poppet inside the plunger head opens on flow and shuts instantaneously.”
The system takes advantage of Md Plastics’ proprietary shut-off nozzles. It has a stationary extruder screw, appropriate for handling a wide range of shot sizes.
According to the company: “The plunger head [acts] as a piston for precise mass displacement into the pressure vessel and subsequent distribution into the mold ... eliminating the dead spots or temperature issues that are prevalent in the state-of-the-art two-component plunger systems.”
The plunger technology ensures shot-to-shot consistency — a quality that can be hard to achieve with conventional injection molding machines (IMMs), Durina said.
Precision is its calling card.
“It’s like a syringe,” Durina said of the machine’s action. “You know when you push a syringe in, if you know how much fluid is in there, and you can determine that, and then you push the syringe in, it displaces the volume that’s inside there. You get a pretty accurate number.”
The compact technology offers numerous other advantages, too, he said.
“It’s green, it’s powerful, it works really well,” he said.
He attributes the system’s environmentally friendly attributes to its streamlined design that eliminates the need for a feed housing or casting. An option for handling liquid silicone rubber (LSR) “does not require a screw for conveying the material, which makes it very green,” Durina said.
In late winter, Durina’s dream will go on display, with Md Plastics planning to play host to an open house showcasing its first Inject-EX IMM. The servo-hydraulic press has a 15mm-diameter screw, 32mm-diameter plunger and air-cooled hydraulic fan.
But other configurations — including all-electrics, bigger-size machines and presses for LSR — are possible, depending on molders’ needs, Durina said.
No matter the products they make, molders bedeviled by some of the shortcomings of reciprocating-screw technologies could find the Inject-EX alternative appealing, he said.
“You can never be sure of what the melt density is with a reciprocating screw, because there’s always pressure changes,” he said. “With our model, you’ll be able to analyze the melt pool in a whole different fashion than what you can do with the reciprocating screw.”
Karen Hanna, senior staff reporter
Contact:
Md Plastics Inc., Columbiana, Ohio, 330-482-5100, www.mdplastics.com
Karen Hanna | Senior Staff Reporter
Senior Staff Reporter Karen Hanna covers injection molding, molds and tooling, processors, workforce and other topics, and writes features including In Other Words and Problem Solved for Plastics Machinery & Manufacturing, Plastics Recycling and The Journal of Blow Molding. She has more than 15 years of experience in daily and magazine journalism.
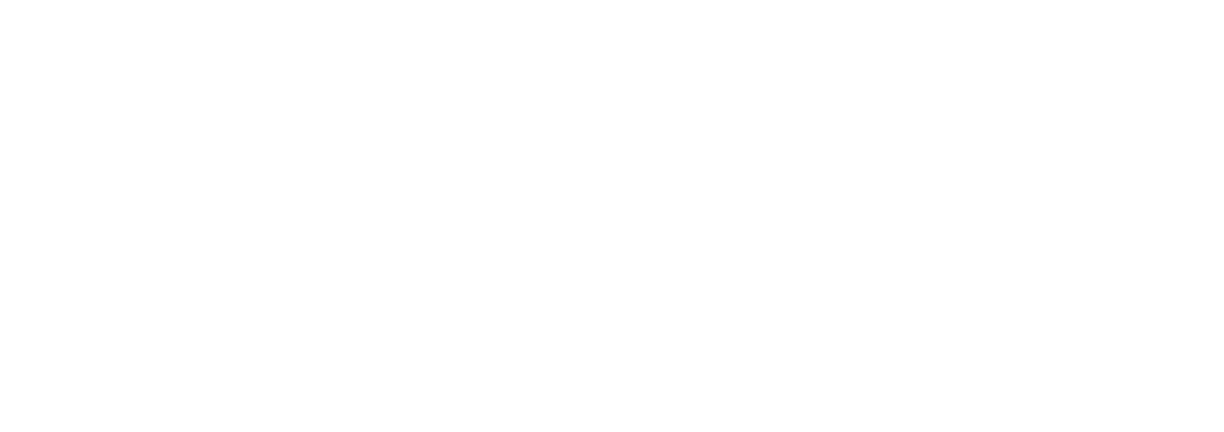