By Ron Shinn
Austrian manufacturer Engel has added another machine series to its duo product line with the duo tech series, available in 35 sizes with clamping forces from about 393 tons to 6,182 tons.
The large-tonnage, dual-platen machines, shown at K 2022, are designed to accommodate larger molds with the same footprint as comparable duo presses. Engel said the duo tech presses achieve greater productivity thanks to a shorter dry cycle time and improved power.
Extra space for bigger molds comes from a newly developed clamping unit, according to Engel CTO Gerhard Dimmler.
All supply connections are attached on a media panel close to the mold and are easily accessible. This improves mold set-up time, Engel said.
The injection and plasticizing capacities have been increased by about 25 percent on the duo tech line. Dimmler said this means that longer flow paths can be achieved with relatively small duo tech models.
Depending on the size, the dry cycle time can be reduced by another one-tenth to four-tenths of a second compared with duo machines. This reduces electricity consumption and production costs.
Engel’s large-tonnage duo series also includes:
- duo combi injection molding machines for multi-component molding;
- duo speed machines for high-speed packaging applications;
- e-duo machines with electric injection units;
- vertical v-duo machines for the composites industry;
- t-win large machines by Engel’s Wintec brand for standard, single-component injection molding.
Engel also introduced iQ motion control, a smart system that automatically optimizes the acceleration phase of injection to support faster movement.
iQ motion control was originally developed for Engel’s Viper linear robots and has now been adapted to injection molding machines. Engel said that in high-performance applications, iQ motion control can significantly shorten cycle times.
The amount of time the press takes to open and close the mold makes up a large portion of the cycle time. The moving mold mounting platen follows individual motion points that split the movement into phases. For each individual phase, iQ motion control software computes the optimum acceleration for the matching machine setting.
The calculations are based on the mold weight, configured mold stroke and clamp force. By optimizing acceleration, the platen speed is increased, and the part can be removed faster.
Engel said the injection molding machine does not need additional energy to operate iQ motion control.
Starting in 2023, iQ motion control will be standard equipment on all new electric toggle-lever molding machines in Engel’s e-cap and e-speed series and can be retrofitted to older machines. The company said these high-performance machines will achieve a dry cycle time that is about 10 percent shorter with iQ motion control.
In addition, Engel has upgraded its 7-year-old customer portal called e-connect to accommodate injection molding machines from other manufacturers. The system can monitor all machines in a plant, automatically calculate overall equipment effectiveness and identify potential improvements. The system can notify an operator when a machine drifts out of tolerances.
The e-connect system comes in a free basic version, as well as several subscription versions.
During a press conference at K 2022, Engel CEO Stefan Engleder said sales in the 2022-2023 fiscal year ending March 2023 will be minimally higher than the $1.5 billion recorded in 2021-2022. Engel’s sales record was $1.6 billion in 2018-2019.
Ron Shinn, editor
Contact:
Engel Machinery Inc., York, Pa., 717-764-6818, www.engelglobal.com
Ron Shinn | Editor
Editor Ron Shinn is a co-founder of Plastics Machinery & Manufacturing and has been covering the plastics industry for more than 35 years. He leads the editorial team, directs coverage and sets the editorial calendar. He also writes features, including the Talking Points column and On the Factory Floor, and covers recycling and sustainability for PMM and Plastics Recycling.
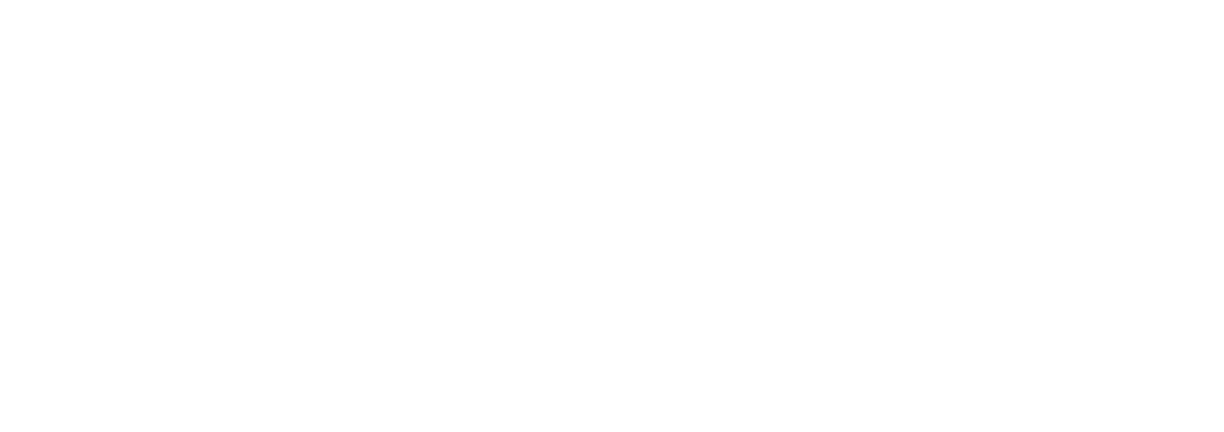