By Karen Hanna
A public health crisis might have delayed its coming-out party, but a new version of an injection molding machine (IMM) from Japan Steel Works (JSW) is now available for molding medical parts.
At recent trade shows, JSW showed its J100ADS IMM — a machine that has been on the market for a number of years — with special adaptations, including optional integrated magnetic platens and powder-coated surfaces, for medical molding. It is made from stainless steel.
“We’re very excited to showcase this system, which is ideal for medical, as well as other clean-room applications,” said Dale Bartholomew, national technical manager for JSW America.
“Our original plan was to introduce this machine at NPE, but that, unfortunately, did not happen. We had planned for a couple other shows, that did not work out with all of the COVID issues.”
A year since the cancellation of NPE2021, the medical-grade J100ADS now is available with clamping forces ranging from about 55 tons to 309 tons. During MD&M West in Anaheim, Calif., the all-electric IMM ran in concert with the iMFLUX system, which automatically adjusts to blocked cavities and material changes. The MD&M West model was equipped with a 110U injection unit, but other machines can be spec’d out according to users’ needs, including with 180U injection units, which are available in stock, Bartholomew said.
The medical-grade IMM is appropriate for making many medical-device components, including syringes, pipettes and hearing-aid components. It operates with accuracy and repeatability, he said.
“The medical market has always been very important to JSW, and now we have a product designed specifically for that market,” he said.
In particular, Bartholomew touted the IMM’s remote machine-monitoring system, called J-Wise, which offers the “capability of remote maintenance and traceability” and “remote access, where our engineers can remote into the control for troubleshooting, with enhanced product/part traceability and quality control.”
With J-Wise, technicians have information at their fingertips — from wherever they log in. Among other applications, they can identify and troubleshoot problems, trace part production and oversee quality control.
In addition to its other features, the J100ADS has bushing-free tie-bars, a purge cover hood vent, and a safety door rail and wheel.
“The design of the machine is for clean-room applications, which are very common in the medical market,” Bartholomew said.
JSW and iMFLUX announced their partnership last year. IMFLUX’s processing software integrates machine learning to allow equipment to run more reliably with fewer operator adjustments. Based on data collected by sensors, the system allows IMMs to mold quality parts with dramatically lower pressures and clamping forces.
Karen Hanna, senior staff reporter
Contact:
IMFLUX, Hamilton, Ohio, 513-488-1017, www.imflux.com
Japan Steel Works America Inc., New York, 630-716-3400, www.jswamerica.com
Vital Statistics
J100ADS-110U
Machine weight (tons) | 4.96 |
Machine dimensions (feet) | 15.2 by 4 by 5.5, 15.9 by 4 by 5.5 |
Ejector stroke (inches) | 3.9 |
Screw diameter (inches) | 0.98 | 1.1 | 1.26 | 1.38 | 1.57 |
Screw stroke (inches) | 3.94, 4.72 |
Heater wattage (kilowatts) | 6.7, 9.2 |
Injection capacity (ounces)* | 1.59 | 1.98 | 3.1 | 3.7 | 4.83 |
Karen Hanna | Senior Staff Reporter
Senior Staff Reporter Karen Hanna covers injection molding, molds and tooling, processors, workforce and other topics, and writes features including In Other Words and Problem Solved for Plastics Machinery & Manufacturing, Plastics Recycling and The Journal of Blow Molding. She has more than 15 years of experience in daily and magazine journalism.
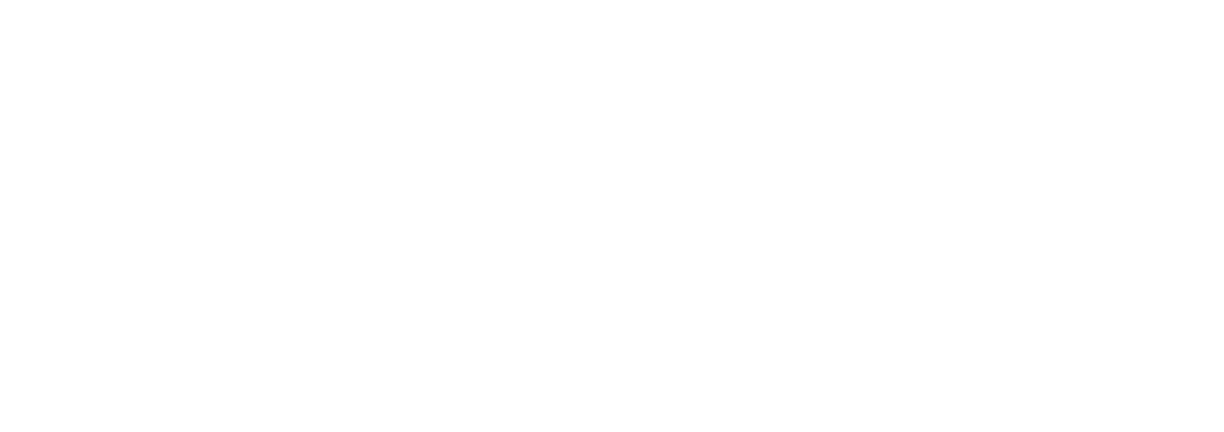