By Karen Hanna
A new cooling unit distinguishes Sacmi’s newest preform-manufacturing press.
The third model in the IPS injection molding machine (IMM) line, the IPS 300 is bookended by the IPS 220 and IPS 400, which Sacmi plans to upgrade by sometime next year. Released in November, the IPS 300 sports a new COOL+ post-mold cooling unit and can be equipped with an integrated PVS156 preform vision system. These innovations allow it to perform in the IoT era, said Moraldo Masi, PET preform division director for Sacmi Imola S.C., Imola, Italy.
“These solutions improve the performance of the system and guarantee an intensive quality control during the process,” Masi said. “The operators and the QC manager [have] a continuous reporting about the quality of the production, eliminating risks of having defective preforms into the boxes. The intensity of the control is about 10 times more [than] the standard of the industry and totally objective.”
The numbers in the IPS line’s machine names denote their clamping force.
Compared with other preform-manufacturing systems, the size and layout of the IPS 300 are among its biggest advantages, as the distance between its tie bars “offers the best composition platform/number of cavities,” Masi said. The machine can run a variety of molds, with 24 to 128 cavities. Depending on cavitation, the machine can produce preforms as long as about 7.7 inches, with weights ranging from about 1.6 ounces to 4.8 ounces; the machine’s biggest injector has a maximum shot weight of about 200 ounces.
According to Masi, the COOL+ system blows chilled air into the insides of the preforms; meanwhile, a tube cooled by water reduces the temperature of the preforms’ exteriors. According to Sacmi, unlike competitor systems, an independent drive moves the COOL+ plate, allowing it to drop the preforms in an area monitored by the PVS156 system.
Designed to continuously scan preforms without increasing cycle time, the PVS156 can detect any type of defect, Sacmi says. It runs comprehensive checks and reads both weight and cavity numbers to generate real-time statistical reports.
With it, manufacturers can avoid shipping out defective preforms.
According to the company, customers who run the IPS 400 will be able to retrofit the press with the new post-mold-cooling unit and new automation architecture and vision system starting this year; the option will become available for IPS 220 IMMs next year.
In addition to the COOL+ and PVS156, machines in the IPS can be outfitted with the FLOW+ hot runner. It, too, offers benefits over older technologies, Masi said.
“The advantages compared to the previous generation are: less dust, less acetaldehyde, better nozzle control,” he said.
Like the other machines in the IPS line, the IPS 300 has a kinetic energy-recovery system, keeping consumption down to 0.09 kilowatts per pound. It can process powder mixes incorporating as much as 100 percent recycled PET and flake mixes with up to 50 percent.
Karen Hanna, senior staff reporter
Contact:
Sacmi USA, Des Moines, Iowa, 515-276-2052, https://sacmiusa.com
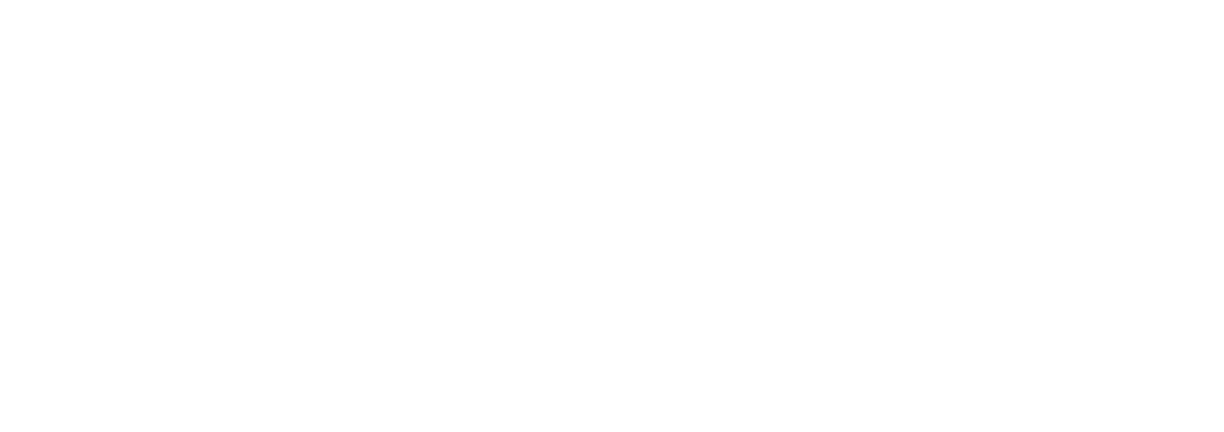