By Karen Hanna
Though the plastics industry hasn’t been immune to the supply-chain disruptions bedeviling the global economy, an Engel representative at the Fakuma show said the machinery supplier has performed well during the COVID-19 pandemic.
But Chief Sales Officer Christoph Steger warned that the ongoing challenges could pose risks for an outlook that’s otherwise optimistic.
“It's been a real jump out of the crisis. We were jolted out of the crisis you might say, and we have made use of the crisis to prepare for this situation, to be ready,” said Steger, who delivered a speech at a press conference Oct. 12, available in English through a translator. “Now, we are capable of dealing with a high demand, and we are also expecting that we will be able to have a growth of 30 percent compared to the previous year — at least 30 percent.”
The North American economy, in particular, had recovered especially quickly, he said.
Steger, who characterized some of the company’s growth as “catching up,” warned that the pandemic — along with supply-chain issues that it precipitated — still could restrict opportunities for the company, which registered revenues of about $1.3 billion during the last fiscal year. In his speech, he specifically broke down the opportunities and challenges facing makers of automotive parts, electronics, packaging and technical parts, as well as medical molders.
Volatility — a feature of the plastics industry over the last 10 years, Steger said — has only increased.
“It remains difficult to provide a reliable outlook,” Steger cautioned, “because there are several risk factors that make it very difficult to predict things reliably. Of course, there’s material bottlenecks, delivery bottlenecks, and then there have also been massive increases in the raw material costs, and the semi-finished products that we need to produce our machines and our tools, of course. And of course, the corona pandemic is not defeated yet.”
In the midst of its transformation to electro motors, the automotive industry has been especially hard-hit by shortages of computer chips and semi-finished components.
Continuing problems could force some plants to halt production, Steger said.
“Many plants … automotive manufacturers have had to stop their lines … until the end of the year, at least some plants in the U.S. Several automotive manufacturers have stopped their lines. … This will also mean that our customers will also start shutting down facilities because, if they don’t have consumers buying it, then they can’t store everything in the warehouse,” he said.
Meanwhile, 5G technology has driven demand for electronics.
Buoyed by interest from consumers stuck at home, both the packaging and technical molding markets also have performed well for Engel, Steger said.
Sporting goods, toys, and home-renovation and construction goods are among products that he cited when he said that the technical molding market has “really reached a level where we’ve never been before.”
For medical molders, demand is returning to more-normal levels.
But, as Steger noted, a return to normal hasn’t happened yet for the wider economy.
In addition to keeping a wary eye on the supply chain and pandemic, Engel also is focused on issues such as rising calls for sustainability. Dueling crises haven’t deterred the company from moving forward, said Steger, who explained that Engel has not drawn down its spending on R&D.
“We are also focusing on meeting the right answers to the challenges that arise from climate change, but also challenges like circular economy and digitalization, particularly in the automotive industry, of course; we have been able to see a real transformation with lots of dynamism,” he said.
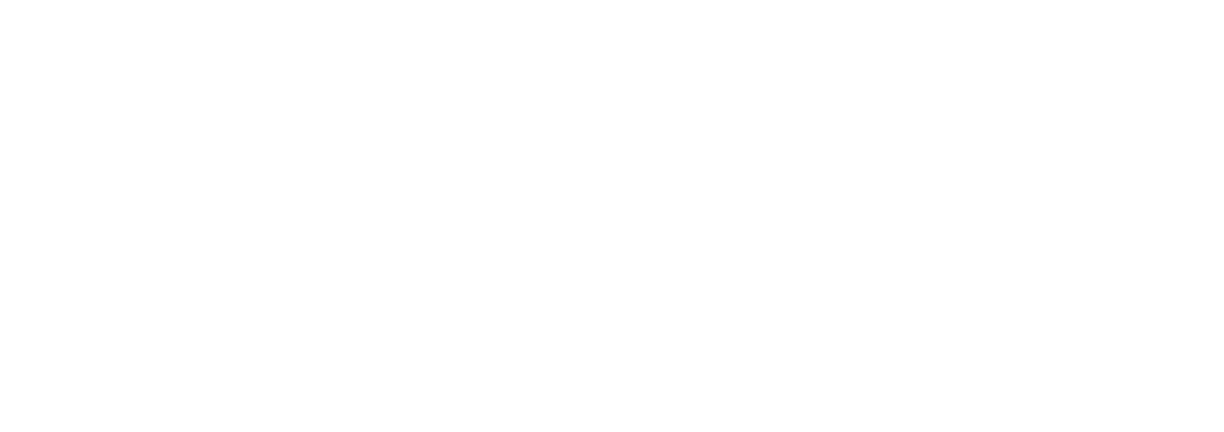