By Karen Hanna
With its development of a new cloud technology for its additive feeders, Ampacet continues to make progress toward giving plastics processors the freedom of lights-out operation.
Liad SmartCloud, which will be available via subscription beginning in early 2022, gives manufacturers access to Industry 4.0 capabilities, such as data monitoring. It could have special appeal for manufacturers that might not have the resources for a sophisticated ERP system, said Doug Brownfield, commercial director for Ampacet.
“We’ve flipped a switch. You’re now able to utilize the cloud,” he said. “I think it is a good first step for a lot of companies. … Especially small companies, small custom shops that don’t have the money or the technology to incorporate into their computer systems, this will make it much easier for them to join the ranks of automation.”
Slated for launch early next year, Liad SmartCloud will be available with all new ColorSave 1000 gravimetric feeders; a retrofit, which would include the replacement of existing feeders’ PLCs and software, also will be available, and the capabilities eventually will be extended to Ampacet’s other feeders, the DualSave and ColorSave-Micro technologies.
It allows users to track alarms, and monitor and adjust production parameters, such as part weight, color, additive percentages, dosing time, shot weight or hourly rate, letdown rate and recipes. With it, users can access live data and display usage and performance reports, or download the data to their own devices.
“If the machine cycle time was disrupted, and it calls for the feeder to adjust incorrectly, you would get a text message that would say, ‘Hey, machine No. 2 feeder is off its desired input.’ This alarm system and systems like that, where you can basically get emails, text messages anytime there’s an issue, beyond just a red light on a machine that would merely tell the operator that something’s wrong, now a manager would also get a notification,” Brownfield said.
If necessary, the service can provide access to Ampacet support.
Brownfield said the need to distance people because of the pandemic, along with companies’ ongoing challenges finding employees, have created a sense of urgency among manufacturers looking to stay competitive in a difficult environment.
“I think the timing of this cloud version is critical because people are working off-site. … So, this cloud technology will allow a manager to monitor all their feeders off-site, offline, even make adjustments to the feeder,” he said. “... That’s kind of the beauty of this system, especially in today’s world where there’s less eyes on the machine on the floor. This now can be managed offline.”
As part of the system, each connected feeder has its own SIM card, giving it access to the cellular network, meaning users can communicate with it even if their plant’s WiFi is spotty.
Liad SmartCloud can be integrated with ERP and MES software. To protect data, the system includes encryption, Brownfield said.
The data-logging capabilities can help manufacturers meet their customers’ expectations for tracking and tracing of parts and issues.
“This kind of programming will give a molder the historical data that they can now basically email to their customers,” Brownfield said. “So, if P&G is demanding, ‘Hey, I want to see, you know, Lot 105K. I want to see how that lot ran, how did the bottles run. Show me the performance metrics of that run.’ … We can now go back, access that data and simply email it to a P&G, for example.”
That could have relevance for manufacturers and customers across many industries, including medical and automotive, as well as among consumer-goods brands, such as Procter & Gamble.
The ColorSave 1000 comes with a choice of hoppers with capacities of 3, 5 or 10 liters, and can store as many as 1,000 recipes. Depending on the hopper size, it can handle up to about 220 pounds per hour.
Brownfield emphasized the ColorSave 1000’s patented self-cleaning capabilities.
“If you’re doing a lot of color changes — let’s say your injection molding machine is doing five color changes per shift — that’s a lot of downtime, cleaning out that feeder that’s running that blue, or blue or red or green. So, the employee has to get on top of the machine, empty out the feeder, spray it out, make sure there’s no red pellets still stuck in there. This new technology that comes standard with our ColorSave 1000, at the push of a button, it will clean out that feeder within 10 seconds,” he said.
Together with Liad SmartCloud, the ColorSave 1000 provides an edge at a time when manufacturers are dealing with extreme volatility in the economy and labor market, Brownfield said.
“People are looking at, ‘How do we operate with less employees?’ Because they know that at some time in the future, a more lights-out automation will have to occur, where you have less people required to work in a plant. Just like McDonald’s is using more kiosks; they have less people taking your orders now,” he said.
Liad SmartCloud delivers the same kind of advantage, he said.
“The smart companies are looking at five years out, 10 years out, and saying, ‘Wow, for me to compete, I need to have the most automated operation possible,’ ” he said.
Karen Hanna, senior staff reporter
Contact:
Ampacet Corp., Tarrytown, N.Y., 914-631-6600, www.ampacet.com
Karen Hanna | Senior Staff Reporter
Senior Staff Reporter Karen Hanna covers injection molding, molds and tooling, processors, workforce and other topics, and writes features including In Other Words and Problem Solved for Plastics Machinery & Manufacturing, Plastics Recycling and The Journal of Blow Molding. She has more than 15 years of experience in daily and magazine journalism.
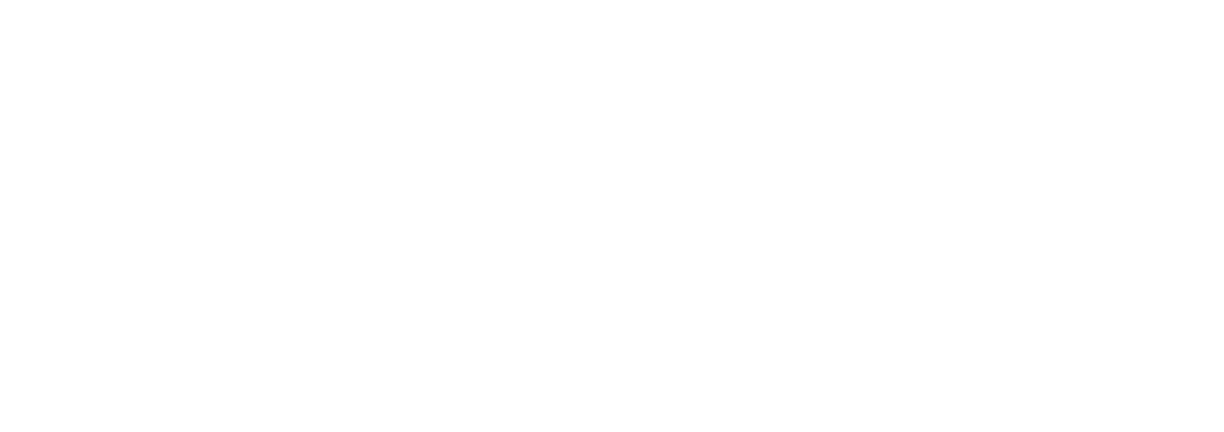