Injection molding machine makers roll out new control technology, sizes, options
By Karen Hanna
Demand for easier-to-use, more feature-rich controls is a major driver in the evolution of injection molding machines (IMMs).
Featuring a mix of electro-mechanical and servo-hydraulic axes, the newest hybrid IMMs promise an array of benefits, including, in some cases, improved controls. OEMs with new offerings include Tederic, Arburg, Wilmington, Absolute Haitian and KraussMaffei.
“Though there is a continuing drive for more sophisticated solutions, which Tederic is able to meet, many molders realize that the current labor shortages are creating a skills gap that is often best served by ensuring that the control is both friendly and relatively simple to use,” said Tony Firth, the VP of sales and marketing for Tederic North America Machinery. “Controls will continue to evolve. Machine learning will become more important in a few years. But more advanced controls should not become more complex to use.”
Daniel Heinzelmann, application engineering consultant for Arburg, also stressed the importance of machine controls.
“Machine control must make even highly complex processes easy to handle and offer transparency. Assistance systems offer valuable help in daily work. The machine control system must be able to integrate peripherals,” he said.
Tederic introduces Neo family of machines
With no NPE show, and in the midst of a pandemic, IMM manufacturer Tederic has shown that business marches on, as it introduced the Neo family of six new machine lines.
While two of the lines — the Neo.E and Neo.Ec — are electric machine series, the other four are hybrids. They are the Neo.H, Neo.Ms, Neo.Mv and Neo.T machines.
The machines, which made their debut in April at Chinaplas, will be available in the U.S. later this year. They feature redesigned machine guarding and have been designed to be safe, practical and user-friendly. With clamping forces from about 99 to 4,400 tons, the new machines are equipped with a new generation of energy-efficient servo pumps that enable ultra-high response speeds. Compared with conventional hydraulic IMMs, they use 30 percent to 80 percent less energy.
“The Neo family of machines has been designed to offer a premium solution, with enhanced specifications, but still at a very attractiveThe new machines have advanced Keba controls and touch-screen control monitors available in a range of sizes, from 12 inches to 21 inches, depending on the model. The controllers offer support for OPC-UA and Modbus data protocols and feature free programming capabilities to accommodate a variety of process requirements.
All the machines have larger tie-bar spacing than previous Tederic models.
In addition to their shared features, machines boast features unique to each new line.
The two-platen servo-pump Neo.H machines can be used by custom molders and manufacturers of a variety of parts, including automotive and appliance parts, as well as trash cans and totes. They are available with clamping forces ranging from about 750 to nearly 3,000 tons; eventually, they’ll top out at about 4,400 tons. They offer more mold daylight, and a special clamp-braking system to improve mold-positioning accuracy. They use an electric screw drive, and the latest-generation motors and drives with DC bus technology. As an option, larger versions of the machine can be specified with tie-barThe Neo.Ms line is designed for multi-material molding, with clamping forces ranging from 970 to 2,116 tons. The machines have two opposing injection units as standard, and additional injection units can be added as required. The secondary unit rides behind the moving platen.
Designed to rotate the center section of a stack mold, the Neo.Ms machines’ Spinsure-H horizontal rotary table is positioned between the fixed and moving platens. Rotary table movement and positioning are independently controlled, allowing for a range of mold designs and complex applications.
According to Firth, they “feature a horizontal rotary table with an upright ‘tombstone’ platen that rides on a sled positioned between the fixed and moving platens.” A second injection unit injects through the moving platen.
“Two molds are mounted, one for the primary material and one for the secondary,” Firth explained. “The rotation of the center platen transfers the mold half with the primary material component to the secondary material position. The advantages are that long parts can be accommodated in a smaller machine. Because the injection units are completely independent, the machine can also be used to simultaneously mold parts on two conventional molds.”
Like the Neo.Ms line, the servo-pump-driven Neo.Mv machines feature a rotary table, the Spinsure-V vertical rotary platen, designed for multi-material molding.
“Injection units can be both servo-hydraulic or electric, or even a mixture of both types. Up to five injection units can be accommodated, with vertical, perpendicular, parallel and piggyback arrangements,” Firth said. Both hydraulic and electric injection units are available for the Neo.Mv machines.
The Neo.Mv line includes wide-platen toggle machines with clamping forces ranging from about 187 to 892 tons and two-platen presses ranging from 970 to 2,116 tons. Both servo-hydraulic and electric injection units are available.
Finally, the Neo.T machines have clamping forces ranging from 99 to about 4,400 tons. New features include a special clamp-braking system to improve mold positioning accuracy. Also, compared with comparably sized presses, the Neo.T machines can accommodate molds with greater stack heights.
Vital Statistics
Tederic model | Clamping-force range |
Neo.H | 750 to about 3,000 tons |
Neo.Mv | 187 to 2,116 tons |
Neo.Ms | 970 to 2,116 tons |
Neo.T | 99 to about 4,400 tons |
Arburg adds model, updates controls
Designed for running cube molds, the 200-ton Allrounder Cube 1800, the latest in the machine series, can be equipped with horizontal injection units in sizes from 400 to 1300 and moving injection units in sizes from 70 to 800. It has tie-bar spacing of 22 inches by 22 inches.
In a recent demonstration cell, a machine equipped with a four-cavity cube mold and Size 400 and 170 injection units churned out four two-color PP caps every 8.7 seconds. The caps were molded at Station 1 of the cube mold. After the mold rotated 90 degrees to Station 2, the molded parts cooled down. The mold then rotated again, and the machine overmolded the caps with a second color at Station 3. At Station 4, a six-axis robot removed the caps.
Besides the 400 and 170 injection units, the Allrounder Cube 1800 is compatible with other sizes of injection units. It can be outfitted with Size 400, 800,or 1300 horizontal units and moving units sized 70, 170, 290, 400 or 800.
According to the company, the Allrounder Cube series brings cube technology to industries beyond packaging; makers of technical and medical products, as well as personal-care goods, all can benefit from the technology.
Compared with conventional molds, cube molds can reduce cycle times by 40 percent, according to Arburg, as well as significantly cut down on the need for floor space. Fitted with an eight-plus-eight-cavity mold, the Allrounder Cube 1800 is capable of more than twice the output of a conventionally sized 570 Allrounder with a four-plus-four-cavity rotary tool using the same mold-mounting surface. Alternatively, the cube would have the same output as at least two Allrounders with comparable tie-bar spacing or a single press three times larger.
As an additional advantage, the Allrounder Cube needs significantly less energy than conventional cube machines, resulting in savings of up to 45 percent.
In addition to its new Cube machine, Arburg has continued to improve the software and control capabilities of its hybrid Allrounder Hidrive IMMs, which now feature the company’s Gestica control, rather than its older Selogica controls. Equipped with numerous assistance functions, the control makes communication with the machines easy and provides detailed 3-D views that can be rotated or enlarged, as needed. Users can operate it using the same swiping and zooming motions that work on smartphones.
With the controls, which have been designed for ease of use, security and ergonomics, operators can save time. According to Heinzelmann, the Gestica controls can be fully integrated with robotic systems and other technologies. The controls allow process simulations to be run directly on the machine and guarantee even more stable processes.
“Thanks to continuous further development, Gestica’s range of functions is now greater than that of the Selogica control system,” Heinzelmann said.
Wilmington adds new sizes for presses for pallets, foam-molding
Designed for efficiency, both new machines can handle 100 percent recycled plastics even in flake form.
Wilmington’s newest machine, the dual-mold Lumina PM-3C, is part of its Pallateer series. Though the standard clamping force for the machine is 675 tons, the company aims to provide machinery that fits the requirements of its customers, and other specs are possible.
The standard Lumina PM-3C can hold twin molds and produce pallets weighing as much as 40 pounds each and as big as 4 feet by 4.3 feet. With an HDPE melting capacity of 2,400 pounds per hour, the machine can produce as many as 80 pallets per hour and more than 600,000 pallets per year. It can produce pallets at a cost of about 40 percent less than a single-mold machine.
According to Wilmington, the Lumina PM-3C is well-built and energy-efficient, with a small footprint. Controlled by either an Allen-Bradley or a Beckhoff PLC, the machine features Bosch Rexroth hydraulic components and an electrically powered extruder. The machine has a two-stage injection unit; bimetallic barrels and long-life feed screws are standard.
While the Lumina PM-3C is designed for molding pallets, Lumina foam-molding machines are more versatile, designed for foaming parts for many markets, including the automotive and materials-handling industries.
The first medium-pressure entrant in Wilmington’s line of foam molders, the 500-ton Lumina MP500 has many of the characteristics of classic structural foam machines, the company said.
Like the smaller, low-pressure machines in the series, the Lumina MP500 has a 30:1 L:D extrusion unit capable of compounding additives, as well as a port for direct gas injection for the lowest-cost foam parts.
The injection unit of the MP500 is a reciprocating type with a unique and proprietary inline first-in, first-out accumulator, President Russ La Belle said.
Thanks to its large L:D ratio and wide melt passageways, the Lumina presses provide superior melting and compounding of mixed recycled materials and recycled-content flake.
“We pride ourselves on sustainable solutions for plastic. All of our injection molding machines are designed to use 100-percent recycled plastics,” he said.
Vital Statistics
Wilmington Lumina MP500 |
Shot size for foam | 480 cubic inches/about 15 pounds for HDPE |
Shot size for molding materials | 240 cubic inches/about 7.5 pounds for HDPE |
Tie-bar clearance | 42 inches by 42 inches |
Usable mold space | 60 inches by 42 inches |
Absolute Haitian launches third-generation presses
As part of its virtual New Product Showcase, Absolute Haitian touted the third-generation upgrades to its Zhafir family of IMMs, including the Jenius hybrid machines, which have an electric screw drive and servo-hydraulic clamp. It also announced a new option for its machines that allows for multi-component molding.
All third-generation models offer software improvements like Motion Plus, which optimizes drive control, and Connectivity Plus, which makes integrating robots and automation easier. They also have increased tie-bar spacing, Industry 4.0 connectivity and a smaller footprint.
The two-platen Jenius machines come in clamping forces ranging from 404 to 3,709 tons. According to Absolute Haitian, they are precise and have a small footprint and quick injection rates. They can accommodate an extended mold movement stroke and ejector stroke.
Featuring controls from Sigmatek GmbH & Co. KG, Lamprechtshausen, Austria, that boast an optimized layout and faster signal processing speed, the machines can be seamlessly connected with automation equipment. With a more-user-friendly interface, they are easier to operate than previous versions.
According to Absolute Haitian, compared with a hydraulic injection unit, the machines’ servo motor and ball-screw driven injection unit provide much more precise injection speed, pressure and position repeatability. Meanwhile, the machines’ parallel lock nut operation ensures fast and accurate response, while their large moving platen ensures platen rigidity during movement.
Use of standardized components for the clamp and injection units improves part availability and lowers cost of ownership, Absolute Haitian said.
In addition to the third-generation Zhafir lines, Absolute Haitian also showed off its new multicomponent-molding platform, the Multi. This series is available across the Zhafir family of machines, including as a special order for the Jenius presses.
Vital Statistics
Absolute Haitian series | Jenius |
Range of clamping forces | 404 to 3,709 tons |
Maximum tie-bar distance | 89.4 inches by 71.7 inches |
Range of possible shot volumes | 26.8 to 406.3 ounces |
Injection speed | 6.3 inches per second |
KraussMaffei increases size range of Netstal Elios presses
The machines feature a five-point, dual-toggle lever and clamping unit that has been modified from previous models to create more space. The Netstal Elios 10000, for example, has a disproportionately large opening stroke of about 4.4 feet, allowing it to produce tall packaging products that can be demolded with in-mold-labeling automation.
The patented injection unit technology facilitates a high ratio of flow path to wall thickness, for the thinnest walls, even for large parts.
The machines are capable of short cycle times, high output and efficiency. The combination of state-of-the-art hybrid technology and the recuperation of braking energy makes the machines very energy efficient. Also, their ability to make very thin-walled parts saves on material costs.
Both the Netstal Elios 8800 and 10000 can be combined with Size 4200 and 6000 injection units. Both 80mm and 90mm screws are available for use with the Size 4200 injection units; the 6000 injection units can be paired with screws with diameters of either 90mm or 100mm.
Depending on customer requirements, additional configurations are also available, according to the company.
Vital Statistics
KraussMaffei’s Netstal Elios 8800 and 10000 |
Clamping forces | 888 tons and 1,003 tons |
Tie-bar clearance | 4.1 feet by 4.1 feet (4.4 feet by 4.4 feet, available as an option) |
Maximum installation height | 4.9 feet |
Opening stroke | 4.4 feet |
Dry-cycle time | 2.2 seconds |
Dynamic injection speed | 7.2 feet per second |
Contact:
Absolute Haitian Corp., Worcester, Mass., 508-459-5372, www.absolutehaitian.com
Arburg Inc, Rocky Hill, Conn., 860-667-6500, www.arburg.com
KraussMaffei Corp., Florence, Ky., 859-283-0200, www.kraussmaffei.com
Tederic North American Machinery Inc., Palmetto, Fla., 941-323-9081, www.tederic-na.com
Wilmington Machinery, Wilmington, N.C., 910-452-5090, www.wilmingtonmachinery.com
Karen Hanna | Senior Staff Reporter
Senior Staff Reporter Karen Hanna covers injection molding, molds and tooling, processors, workforce and other topics, and writes features including In Other Words and Problem Solved for Plastics Machinery & Manufacturing, Plastics Recycling and The Journal of Blow Molding. She has more than 15 years of experience in daily and magazine journalism.
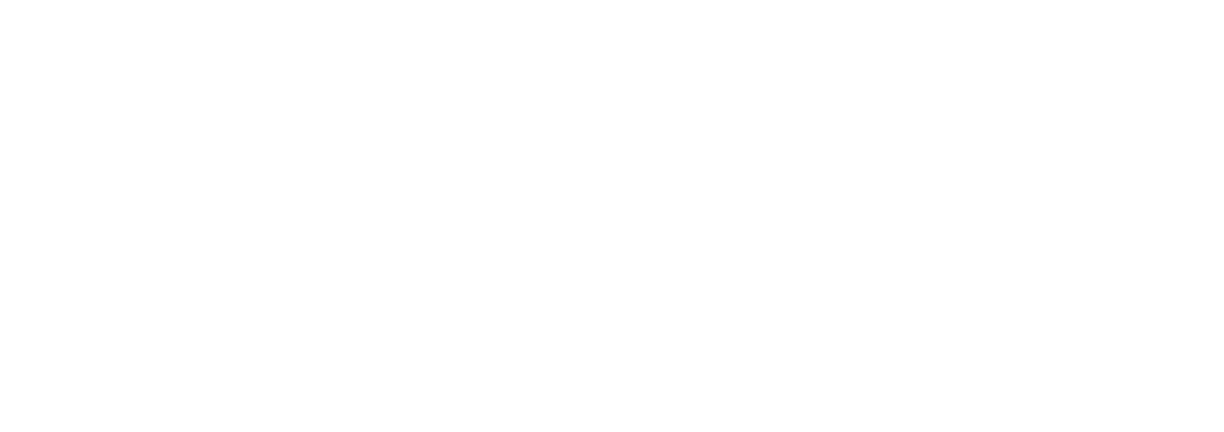