Electric injection molding machines provide efficiency, speed, precision
By Karen Hanna
Wittmann Battenfeld makes both hybrid and all-electric injection molding machines (IMMs), but Rainer Weingraber, CEO of Wittmann Battenfeld GmbH in Kottingbrunn, Austria, has seen a growing preference for the latter.
“What we see in the market is generally the efficiency of the machines is getting more and more important. Just after the [pandemic] crisis, everybody's thinking green and that's very positive, and we fully support that. And I have to say, this was always our strategy,” Weingraber said during Wittmann Interactive, an online event highlighting the company’s technologies and facilities.
Among companies with the newest offerings in electric IMMs are Tederic, Absolute Haitian, Arburg and Milacron.
Tederic introduces Neo family of machines
Chinaplas 2021, the only major trade show of the pandemic era, served as the launchpad and coming-out party for the Neo family of machines — six new lines from Tederic. Equipped with a new generation of energy-efficient servo pumps that enable ultra-high response speeds, machines in the six new series use 30 percent to 80 percent less energy than comparable hydraulic IMMs. They also have larger tie-bar spacing than previous models, said Tony Firth, VP of sales and marketing, Tederic North American Machinery.
Of the new lines, the Neo.E and Neo.Ec are electrics. The Neo.E line is all-electric with clamping forces ranging from about 60 tons to 507 tons, and pressure accuracy to within 1 bar. Featuring low-speed control, the series is suited for precision technical, medical and high-volume, thin-wall applications, as well as the production of packaging, electronics and high tolerance components. It features NSK linear bearings for platen guidance.
The Neo.E machines are “accurate, fast, rugged,” Firth said.
They boast injection speeds of up to 500mm, or 1.6 feet, per second.
“All-electric machines, with 500mm-per-second injection rates, are becoming more popular for thin-wall applications,” Firth said.
With clamping forces ranging from about 185 tons to about 1,200 tons, the Neo.Ec hybrid-electric machines are “for custom molders who want the added accuracy of an electric machine but with the convenience of hydraulic core pull, and more powerful ejection/nozzle force,” he said. With injection speeds of up to 9.8 inches per second, the machines would be appropriate for makers of packaging.
The machines’ injection, screw rotation and clamping unit are electro-mechanically driven, while an integrated power pack with servo-pump powers the ejectors, carriage and core pulls. The carriage has twin hydraulic pistons, and the moving platen features linear bearing guidance.
The Neo.E and Neo.Ec feature the latest-generation motors and drives with DC bus technology and have advanced Keba controls. The Neo.E comes with a choice of 12-inch, 15-inch and 21-inch touch-screen displays; the 15-inch console is standard with the Neo.Ec. The controls offer support for OPC-UA and Modbus data protocols and feature free programming capabilities to accommodate a variety of special process requirements.
Absolute Haitian showcases electric machines' capabilities
Absolute Haitian has had a busy year, despite the ongoing pandemic. With NPE 2021 canceled, it threw its own event — virtually, of course.
Among the innovations touted at its New Product Showcase, Absolute Haitian showed a couple models in its Zhafir lineup of electric IMMs, now in their third generation. The lineup includes: the fully electric Venus machines; electric Zeres machines, which have a hydraulic circuit used for core pull, ejectors, valve gates and injection carriage movement; and hybrid-electric, two-platen Jenius machines. All models within the Zhafir family of machines have a smaller footprint, increased mold capacity and improved part drop/robot removal. Dry cycle times for the machines have been reduced by 10 percent.
As part of the show, Absolute Haitian used its clean-room-ready VE 600 III-120, a 67-ton Zhafir Venus, to make a component for a surgical awl. It also showed off its new multicomponent-molding platform, the Multi — available as an option for the Zhafir family of machines. At the show, a 135-ton Zeres Multi, a ZE 1200M-160h/V80h, was configured with a pair of injection units, one horizontal and one vertical, to make medical syringe plungers.
According to the company, the Zhafir Venus work cell demonstrated the precision, energy-efficiency, fast acceleration and speed of the series, which includes machines with clamping forces ranging from 44 to 899 tons. Designed with mold protection in mind, the machines are quiet and require no oil, making them very clean to operate. The Zhafir Venus III machines come with 15-inch controllers from Sigmatek GmbH & Co KG, Lamprechtshausen, Austria.
Like the Zhafir Venus III machines, the Zeres Multis also provide precise, quiet, energy-efficient and maintenance-friendly operation.
According to the company, they are designed to make integration with upstream and downstream equipment easy. The machines’ second injection unit can be set up in a variety of configurations: horizontal “L”; vertical; piggyback, in which one injection unit is set on top of the other at an angle; parallel; and opposing, in which the injection units are placed at opposite ends of the machine.
According to the New Product Showcase, the Venuses and the Zeres Multi can be specified to handle stack-mold operations and injection speeds of up to 350mm per second. They are designed for quick screw swaps.
The Venuses have improved hold pressure response.
All third- generation models offer software improvements like Motion Plus, which optimizes drive control, and Connectivity Plus, which makes integrating robotics and automation easier. They also have increased tie-bar spacing, Industry 4.0 connectivity and a more compact footprint.
Use of standardized components for clamp and injection units improves part availability and lowers cost of ownership.
Absolute Haitian products are sold in more than 130 countries with machine sizes ranging from 44 to 7,425 tons of clamping force.
Arburg updates controls
Arburg has continued to update the software and control capabilities of its all-electric Allrounder Alldrive IMMs. All new Allrounder machines now come with an Industrial Internet of Things (IIoT) Gateway as a standard feature, allowing their users to connect to the company’s customer portal or remote service.
In addition, the company’s Gestica control now is available for machines with at least 280 tons of clamping force. Equipped with numerous assistance functions, the control makes communication with the machines easy and provides detailed 3-D views that can be rotated or enlarged, as needed. Users can operate it using the same swiping and zooming motions that work on smartphones.
According to Arburg, the presses are high precision, adaptable and cost-efficient.
Milacron/Fanuc introduce Roboshot Alpha-SiB
In partnership with Fanuc, Milacron was anticipating delivering the first of the companies’ newest all-electric injection molding machine series, the Roboshot Alpha-SiB series, in the second quarter of this year.
Based on the earlier Roboshot Alpha-SiA series, the new series includes machines with a range of injection-unit sizes and clamping forces of 55, 110, 140, 165 and 240 tons. They have increased standard injection pressures, faster injection velocities, expanded available screw diameters and new software; as an option, the smallest two models can be specified for high-speed ejection.
With the new series, Milacron expands the flexibility of the Roboshot line by providing models with smaller injection capacities in multiple sizes for high-precision molding applications.
The series offers as standard several features that previously were options. They include increased mold stack height and three-stage air ejection, and precise clamping force control for consistent venting and reduced mold wear.
They also have increased standard injection pressures, a high-performance control with higher resolution, custom lock-out capability for security and a longer tie bar on select models.
The machines have a higher-performance 21.5-inch Panel iH control that provides quick setup, improved graphics, multi-window navigation and better ergonomics. With the Windows 10-based software, users can view the entire molding network from any machine and more easily operate Fanuc robots. The operating system can store data for as many as 500 molds.
“Over the last two years, these systems have proven to be invaluable for the medical and packaging industries,” said Kent Royer, technical product manager for the Roboshot line.
Karen Hanna, senior staff reporter
Contact:
Absolute Haitian Corp., Worcester, Mass., 508-459-5372, www.absolutehaitian.com
Arburg Inc., Rocky Hill, Conn., 860-667-6500, www.arburg.com
Milacron LLC, Batavia, Ohio, 513-536-2000, www.milacron.com
Tederic North American Machinery Inc., Palmetto, Fla., 941-323-9081, www.tederic-na.com
Wittmann Battenfeld Inc., Torrington, Conn., 860-496-9603, www.wittmann-group.com
Karen Hanna | Senior Staff Reporter
Senior Staff Reporter Karen Hanna covers injection molding, molds and tooling, processors, workforce and other topics, and writes features including In Other Words and Problem Solved for Plastics Machinery & Manufacturing, Plastics Recycling and The Journal of Blow Molding. She has more than 15 years of experience in daily and magazine journalism.
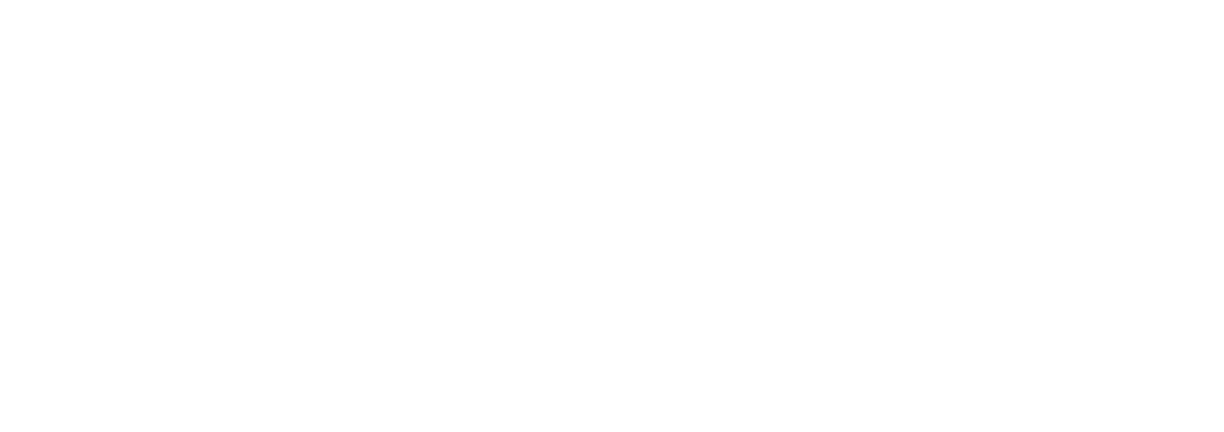