Arburg traceability system provides benefits for part production, recycling
A recent Arburg injection molding machine (IMM) demonstration provides manufacturers with Industry 4.0 strategies for closing the loop, when it comes to producing — and eventually recycling — end products.
As part of a work cell set up for the virtual Hannover Messe, a networked turnkey system, anchored by an all-electric Allrounder 370 A with a clamping force of about 67 tons, pumped out decorated PP cups with a rippled surface every 40 seconds. It used the company's new Multilift V 20 vertical robotic system and a single hot-runner mold from Haidlmair, Nussbach, Austria.
The cell was equipped with intelligent assistance systems, including aXw Control FillAssist, which provides 3-D graphics showing the fill level of a part in relation to the current position of the screw.
The cell also employed a Supervisory Control and Data Acquisition (SCADA) system known as the Arburg Turnkey Control Module (ATCM), which displays graphics tracking process data and amalgamates it for each specific part.
Offering 100-percent traceability — an essential capability for demanding markets such as the automotive and medical industries — the ATCM can be used in sustainability efforts. At the Hannover Messe, the ATCM collected all data from equipment involved in the molding process, including theBy checking the codes on the cups at the end of their lifecycle, recyclers will be able to determine their material type.
In addition, the SCADA system can help users pinpoint and troubleshoot production problems, such as defective parts.
According to Arburg, using the ATCM, the operator could select any of three designs for each cup; downstream, a plasma treater prepared the cup surfaces for digital printing, and scanners ensured the cups’ codes were readable.
Contact:
Arburg Inc, Rocky Hill, Conn., 860-667-6500, www.arburg.com
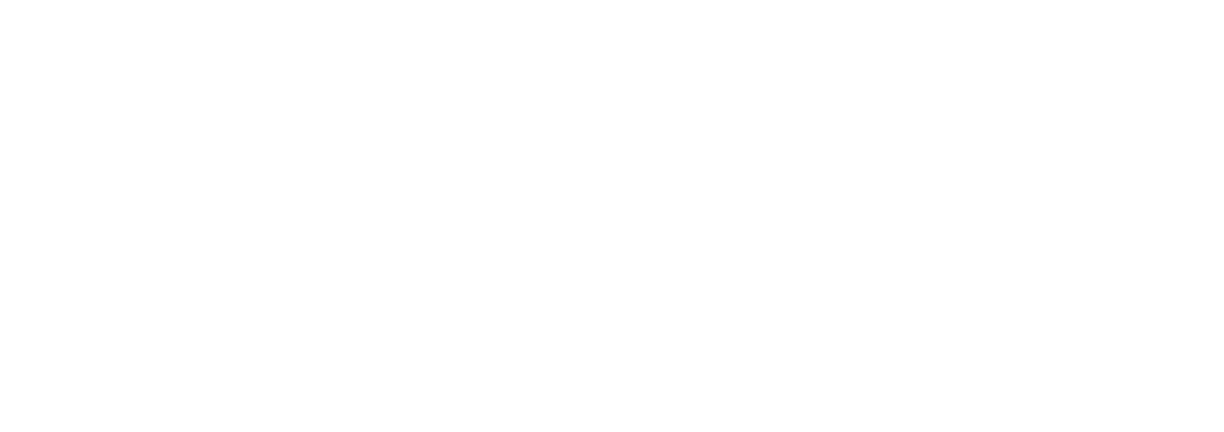