By Sean Silvey
Fluke Corp.
One-hundred-percent run time is always the goal in plastics manufacturing, which is why so much goes into maintaining the equipment and infrastructure of the plant. When so many things can go wrong, it’s important maintenance technicians have the essentials down to pursue operational excellence. Here are eight essential electrical measurements to keep in your tool kit.
Your first and last thought should always be safety. Before starting work on an electrical circuit, follow lockout-tagout procedures and use the three-point-test method to ensure your tool is working properly before and after the test. This method checks for the absence of voltage at 50 volts or more.
- Verify the tool is working correctly by testing on a known energized source or on an electronic proving unit.
- De-energize the circuit to be verified. The tool should indicate zero energy.
- Check your tool again using the known energized source or electronic proving unit.
Current
The right tool, like a clamp meter, can help determine balanced and unbalanced loads throughout your plastics facility. A current measurement will help raise a red flag, if necessary, letting you know if you need to come back with a power-quality tool to determine the unbalance.
Catching harmonic current flowing through a system before an issue arises can help save time and money later. Non-linear loads or devices that conduct current for less than a full sine wave cause harmonics that generate voltage distortion. In severe cases, these harmonic currents can cause thermal trips or logic faults.
As the voltage distortion caused by current increases, linear loads begin to draw harmonic current. This distortion can cause counter-torque which, in turn, increases current, which can cause the motor to overheat. This situation also can cause a host of other problems, including increased heating, decreased motor efficiency and a reduction in motor life.
Voltage
Taking a measurement of either AC or DC voltage is another first step in motor inspections. A meter can begin to tell you if there is a power-supply issue you need to further troubleshoot. A clamp meter or multimeter can let you know if equipment is working smoothly or if something is off, which might require grabbing a more powerful meter.
If a measurement isn’t what it should be, grab a power-quality meter to investigate further. Look for harmonic distortion, swells or sags that might be present in the motor. If the cause is internal, these can be a sign of increases in voltage requirements throughout your facility. If it’s external, it can be caused by nature, like trees or foliage affecting power lines. If a motor is experiencing sags or swells in power, both possibilities are worth taking the time to investigate and correct.
Resistance
Control circuits, like switches and relay contacts, can wear down over time. Checking the resistance as part of your regular measurements can reveal the condition of the components. The higher the resistance measurement, the lower the current flow through and to the motor at the end. It’s usual for resistance to start out very high and decrease over time. The increase is caused by dirt buildup, more wear and tear on the components, insulation breakdown or moisture buildup.
Finding and fixing these kinds of issues early can prevent a lot of damage down the line. It can even save you from expensive repairs or full asset replacement.
Continuity
Testing a circuit for continuity tells you if two points are electrically connected. These checks verify proper connections and let you know if there’s a break that could be causing power-quality issues anywhere in the electrical path.
Using a clamp meter or multimeter to look for these kinds of issues is a great use of the tool. Along with the measurements mentioned above, you can gather trend data during your regular preventive maintenance, making it easy to see when a measurement is abnormal. Use that information when you come back later with a more powerful power-quality tool to determine the origin of the issue.
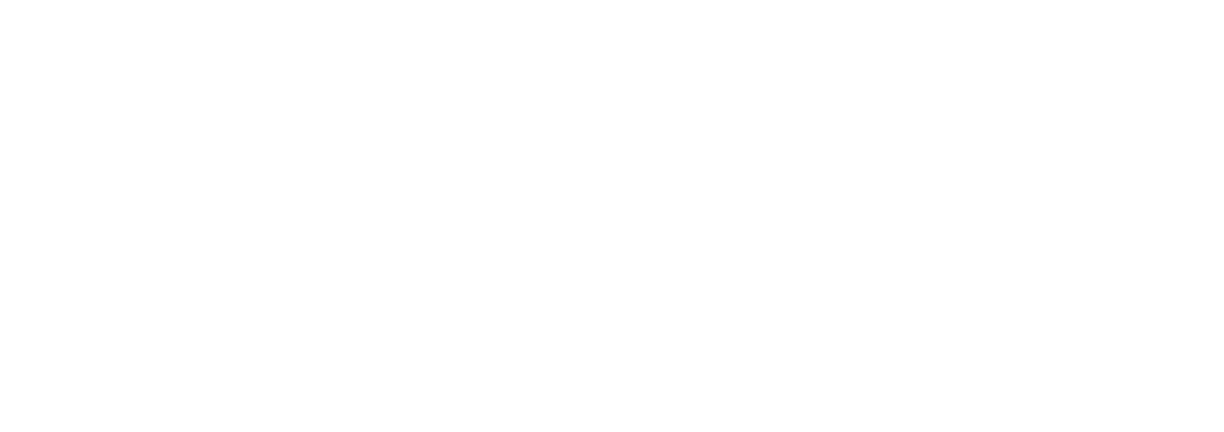