New M-Powered applications monitor signs of machine failure
Milacron has made three additions to its M-Powered suite of applications, designed to provide predictive maintenance capabilities to its users. The additions allow processors to use predictive models to evaluate wear and tear to achieve the optimum operation of M-Powered-equipped extruders and injection molding machines.
M-Powered is a networked IIoT suite of observational, analytical and support services tailored to individual users, including machine operators, managers and service technicians. The new applications go beyond focusing on point-of-failure predictions to using the next generation of machine learning algorithms to continuously quantify the impact of wear and tear, the company said. The three new applications became available for M-Powered users this summer with the assistance of ei3 Corp., Pearl River, N.Y., Milacron’s data science partner.
“Our data science team has crafted algorithms that give operators valuable insights into the inner workings of the Milacron machine; for the first time, it allows us to quantify the impact of wear and tear as it progresses,” said Stefan Hild, director of data science at ei3. “Operators can then make smart decisions by weighing that cost against the cost of maintenance.”
Predictive analytics leverage data science to track machine conditions and to advise operators on when machine maintenance should be performed or when parts should be replaced. The three new applications are designed to provide information that will allow processors to do more than simply wait for a component to break before replacing it. The applications give processors insight to be more proactive.
M-Powered applications are available on Milacron injection molding machines and extruders, and can be used with non-Milacron machines, the company said. Non-Milacron machines with control systems that are not compatible with the M-Powered applications might need additional hardware to connect.
“As manufacturers evaluate and reform their operations to reduce waste, efficiency can reach new heights,” said Edward Jump, M-Powered IIoT digital analytics leader. “In real-world applications, true maintenance requirements are based on many variables. Through the adoption of machine learning and advanced analytics and AI, M-Powered can now monitor signals of impending failure. When combined, these are key indicators that allow manufacturers to deploy maintenance resources.”
The three new M-Powered applications are screw efficiency analysis, fill case analysis and efficiency report.
Screw efficiency analysis
The plasticizing screw is a highly engineered component that often requires a long lead time to order and can be expensive to replace. As the screw wears through normal usage, its ability to efficiently convey material is reduced, which leads to increased recovery times, energy consumption and melt temperatures. This can increase cycle times and might hurt part quality, the company said.
In most cases, wear occurs slowly. As a result, the deterioration of the process also occurs over time, which makes it difficult to detect.
Milacron’s screw efficiency analysis application, which became available to M-Powered users in June, uses an energy-based assessment to determine the deterioration of the process. Its touch-free functions can provide insight into the screw’s health without adding sensors to the screw or barrel. Milacron does this by using data science to run a patent-pending machine-learning algorithm analysis on the machine’s energy use and other factors, Jump said.
This allows M-Powered users to order a new screw and replace it before it becomes so worn it hurts production.
Fill case analysis
The feed-screw tip is a key component that’s a link between the machine and the mold. It has a check ring or a non-return valve that’s critical to the process. The screw tip is a high-wear item, and the screw tip and check-ring portion of the tip assembly are exposed to great forces during molding. It’s challenging to understand and actively measure wear, the company said. As the feed-screw tip wears, it has a direct impact on process quality and repeatability. Due to a high level of wear, it needs to be replaced more often than other injection end components, the company said.
The fill case analysis application conducts a shot-by-shot, multi-variable analysis to understand the condition of the screw tip and to indicate the effect of wear and tear on part quality, cycle time and operating costs. This application displays an alert and alarm when issues impact repeatability.
“This alarm will be available from the injection molding machine controller, as well as the mobile dashboard from computers or smartphones,” Jump said. “It can also generate email alerts.”
Similar to the screw efficiency analysis application, this is an evolving machine learning process that accounts for distinct parts and operator adjustments.
The fill case analysis application became available to all M-Powered users in August.
Efficiency report
The efficiency report application monitors and presents the leading variables that increase the cost of production, including increased heating energy, energy used by the extruder or molding machine and cooling time.
Using the application, operators can view a summary of the efficiency of each machine or an entire fleet of machines in real time. This allows them to identify and correct costly causes of cycle deviations.
“Looking at a long-term view of the performance of the machine on a shot-by-shot basis, the algorithms will be able to determine the remaining useful life of critical components, based on the data from the specific machine, as well as the overall connected fleet of injection and extrusion machines in aggregate,” Jump said.
The company planned to make the efficiency report application available to all M-Powered users in September.
Milacron now offers 12 M-Powered applications. The other nine are connect portal (formerly remote portal), downtime tracking, production monitoring, technical support, predictive analytics, preventive maintenance, iMFLUX, recipe insight and quality management.
Milacron launched the M-Powered digital brand in 2018, which was part of a digital transformation partnership with ei3 that began in 2013. Ei3 has been partnering with machine builders to connect industrial equipment to the internet for more than 20 years.
Milacron LLC, Batavia, Ohio, 513-536-2000, www.milacron.com
Bruce Adams, senior staff reporter
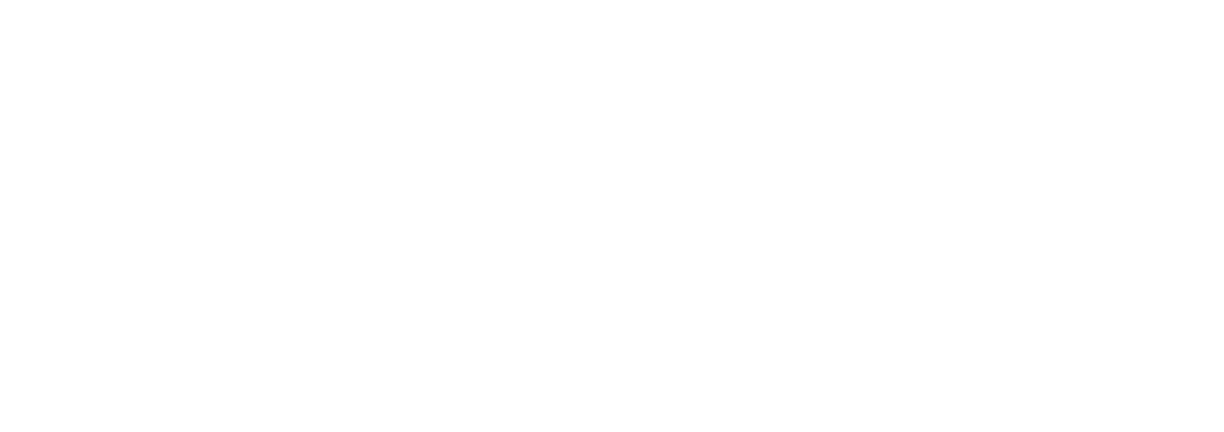