PMM staff report
Automation specialist Sepro says its robots are supporting the front lines of the fight against COVID-19, even as the company continues to cope with the need for physical distancing among its employees at plants around the globe.
The need for robotics and automation is growing, said Xavier Lucas, chief sales officer for Sepro Group, based in France. “Sepro sold as many robots in June as we did in a much easier context last year,” he said. “In a context where the economy is almost at a standstill, this suggests that the crisis is driving the adoption of automation in plants. We believe that the need for social distancing is just accelerating a natural trend: In the industry, much work can be largely handed over to a combination of software and robotics.”
Like the companies that depend on it, Sepro has followed government guidelines to protect the health and safety of its employees, customers and partners.
To help customers still wary of travel, Sepro has suspended its in-person training classes and is offering webinars covering a range of basic and intermediate topics via online meeting systems.
The company limited its operations in the spring at its headquarters in La Roche-sur-Yon but has since returned to normal production levels there.
At Sepro America’s headquarters in Pennsylvania, where a stay-at-home order went into effect in late March, most employees worked from home, with a few on site staffing the company's service hotline and spare parts operations. All workers returned in early June when the order lifted. According to Jim Healy, VP of sales and marketing, the company installed plastic shields to screen work areas off from one another. Sales managers and service technicians also have been vigilant while on the road.
“Our world was disrupted completely, and we recognize that our robots often play an important role in supporting companies providing critical equipment and materials [for] those on the front lines fighting the virus,” said Raul Scheller, managing director for North American operations. “We have an incredible team — sales, service, engineering, operations and administrative staff — who have stayed optimistic from the beginning and shown fantastic creativity in maintaining a high level of service to customers, while also acting responsibly during the pandemic.”
Sepro has prioritized the needs of the health and medical sectors, along with the food industry, Lucas said. “For instance,” he said, “in the U.S. and several locations in Europe, we helped customers quickly develop capabilities they needed to keep up with demand caused by the pandemic.”
Some changes wrought by the pandemic might prove permanent, as companies have been forced to evolve quickly to cope.
Lucas pointed out that demand for automation tends to rise when technologies come of age at a time of economic difficulty. That’s what happened in the early 2000s, when Asia faced a crisis from another disease caused by a coronavirus, known as Severe Acute Respiratory Syndrome, or SARS. “With the rise of big data, cobotics and other high technologies and associated services, we believe we are entering a new accelerating era for automation,” he said.
Contact:
Sepro America, Warrendale, Pa., 412-459-0450, www.sepro-group.com
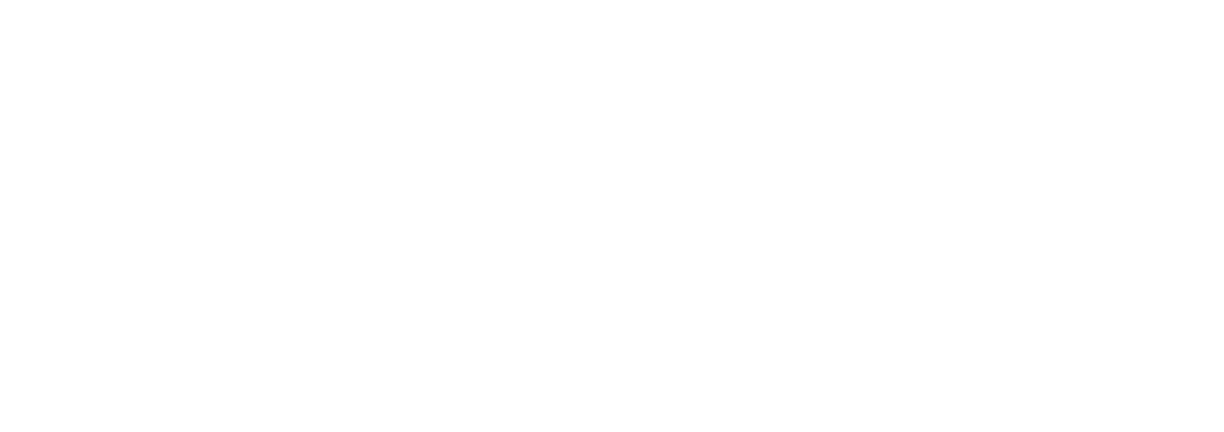