KraussMaffei has expanded its GX series of hydraulic injection molding machines with the addition of the GX 1100, which offers 1,240 tons of clamping force. Prior to the machine’s launch at K 2019, GX series machines had clamping forces ranging from about 450 to 1,000 tons.
“We are expanding the range of our successful GX series with a specific target,” said Hans Ulrich Golz, president of the injection molding machinery segment of KraussMaffei. “We see great opportunities particularly in the areas of packaging and logistics.”
In addition to large packages, the machine can manufacture medical devices and automotive parts, the company said.
GX machines feature a space-saving, two-platen design, a modular configuration and a wide variety of equipment options, including energy-saving servo drives.
At K 2019, KraussMaffei exhibited a GX 1100 producing 20-liter buckets from PP in a mold with two cavities. It decorated them via in-mold labeling. The shot weight for the buckets was about 3.3 pounds and the cycle time was 14 seconds, KraussMaffei said.
The GX 1100 came with the company’s Smart Operation software feature made by Netstal, a KraussMaffei brand. The optional feature allows the machine operator to run the machine by pressing only four buttons.
An optional speed package, displayed on the demonstration machine, allowed for increased injection speeds by up to 2.3 feet per second and faster clamping speeds. The option is especially useful for presses molding large packaging components with mold opening widths of more than 1.1 feet, Golz said. The speed option shortens the dry-cycle time by almost half a second, compared with the dry-cycle times of machines in the company’s MX 1000 series.
In addition, an HPS barrier screw for polyolefins allows faster melting and larger shot weights. It improves plasticizing performance by up to 40 percent, compared with conventional high-
performance screws from KraussMaffei, Gotz said.
The GX 1100 also demonstrated the benefits of APC (Adaptive Process Control) Plus software. It automatically controlled and monitored both the molding of the buckets and the in-mold labeling process. The software compensates for external influences on part quality, Golz said, such as fluctuating resin quality, changing environmental conditions and the effects of machine wear. It automatically adjusts the changeover point from injection pressure to holding pressure, as well as the holding pressure level from shot to shot. It also compensates for deviations in the closing of the non-return valve and in resin viscosity.
Integrated in the control cabinet of the GX 1100, KraussMaffei also featured the DataXplorer, a preconfigured data storage device for the automatic recording of sensor and control data.
“It provides a detailed view of the depth of the process by storing up to 500 signals every 5 milliseconds as continuous graphs — for instance, signals from the machine itself or special signals such as the mold cavity pressure,” Golz said. “The digital information from the injection molding process and the information from the automation and peripherals flows [into] a new data collection point, which enables the customer to control and monitor its production flow.”
Benefits of this are a high level of process transparency and traceability; easier troubleshooting and machine diagnostics; and the uninterrupted monitoring and documentation of processes, Golz said. The DataXplorer can be connected to an MES.
Bruce Adams, senior reporter
Contact:
Krauss-Maffei Corp., Florence, Ky., 859-283-0200, www.kraussmaffeigroup.us
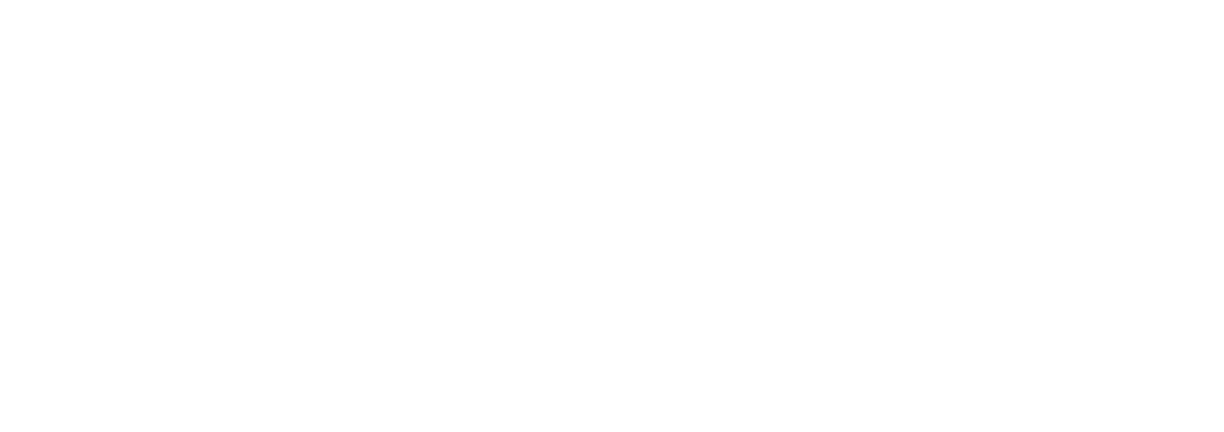