A new series of twin-tower (also known as twin-bed) desiccant dryers increases energy efficiency and decreases desiccant regeneration times without affecting drying performance, according to manufacturer AEC.
The company’s NGX series has a single blower. While traditional dual-blower, twin-tower dryers use one blower for drying resin and a second blower for regeneration air, single-blower designs use one blower and divert a percentage of the process air for desiccant regeneration and cooling. During regeneration, desiccant is dried so it can be used again. Single-blower dryers are more compact than dual-blower units.
Tony Johnson, senior materials-handling product manager for ACS Group, the parent company of AEC, said engineers set out to design the most energy-efficient twin-tower dryer they could with a single blower. They wanted to maintain a dew point of minus 40 degrees Fahrenheit or lower at all times.
“We’ve taken the things we have learned over 60 years of dryer experience and bumped it up to the next level in terms of performance and energy efficiency,” Johnson said. “We have really fine-tuned this, and we’ve got it to the point we think we are pretty much on the leading edge of what physics allows us to do with a single blower.”
The NGX dryers reduce electrical energy consumption by more than 25 percent, compared with competitors’ wheel-drying technologies, he said.
“We have done apples-to-apples comparisons of comparably sized dryers and found in every controlled test we did, the wheel dryers (from multiple competitors) consumed more energy than our NGX dryer achieving the same or better dew point,” Johnson said.
Wheel dryers have smaller heaters, prompting some companies to claim that they are more energy-efficient than twin-tower units, but AEC believes its technology, which does not involve constant regeneration of the desiccant, is more efficient, Johnson said.
NGX dryers are available in six sizes, ranging from 25 pounds per hour to 300 pounds per hour of processing capacity. The models are the NGX-25, NGX-50, NGX-100, NGX-150, NGX-200 and NGX-300, with the numbers designating the maximum number of pounds per hour of resin they can process.
The dryers are available in several configurations:
• as stand-alone units;
• as portable units, with a dryer and hopper on a cart;
• on a Nomad Cart that takes the portable dryer/hopper combination and adds integrated conveying for beside-the-press use;
• and as part of a small, central dryer system that can feed multiple drying hoppers and multiple processing machines.
A unique feature available on the NGX series is the “switch on dew point” option, Johnson said. It takes advantage of dry ambient conditions to reduce energy consumption even further while maintaining a low dew point.
“This option is ideal for customers that see less-humid ambient conditions in winter or customers who run during early-morning or later-evening hours when ambient dew point often drops substantially lower than daytime highs,” Johnson said.
When turned on, the feature monitors multiple conditions — including dryer dew point, hopper-supply temperature versus return-air temperature, regeneration-bed temperatures, regeneration-exhaust temperatures and regeneration times — to determine the maximum cycle time for each bed.
In ideal conditions, such as when humidity is exceptionally low, a bed could be used for up to 90 minutes longer than usual without needing regeneration. Reduced regeneration times can result in significant energy savings, the company said.
The NGX series has a control platform anchored by an Allen-Bradley PLC and a 7-inch high-resolution color touch screen. The interface gives processors easy access to significant data, including trend charts for critical conditions that help customers analyze dryer performance and monitor the dryer for specific maintenance needs.
Using a server in the dryer, the controls also offer the ability to remotely monitor and control the dryer from any phone, tablet or computer. Managers can monitor dryer performance with a simple click of a button.
Bruce Geiselman, senior staff reporter
Contact:
AEC New Berlin, Wis., 262-641-8600,
Bruce Geiselman | Senior Staff Reporter
Senior Staff Reporter Bruce Geiselman covers extrusion, blow molding, additive manufacturing, automation and end markets including automotive and packaging. He also writes features, including In Other Words and Problem Solved, for Plastics Machinery & Manufacturing, Plastics Recycling and The Journal of Blow Molding. He has extensive experience in daily and magazine journalism.
Request More Information
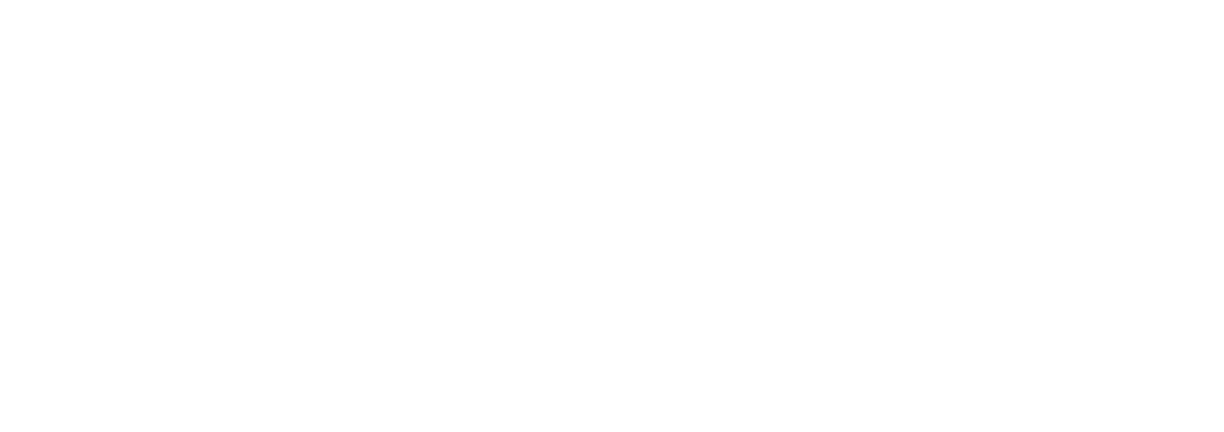