GMP dehumidified drying systems from Universal Dynamics, a subsidiary of Italy’s Piovan, can be used either as single-hopper dryers or as part of a central drying system when configured with Una-Dyn’s Modula central drying technology. U.S. production of the GMP dryers began earlier this year.
The GMP dryers are part of the Genesys drying line and are appropriate for drying a wide range of resins.
“Minimum and maximum hopper drying conditions are continually checked and monitored for material conditioning safety as well as to provide the optimal setting,” said William Goldfarb, president of Una-Dyn. “The hopper conditions are constantly compared with data collected by the hopper’s instrumentation and, using a patented measuring unit located in the air-supply line at each hopper, it adjusts and controls the airflow instantaneously and independently, achieving the exact requirements versus wasteful over-usage.”
Modula’s operation with a GMP dryer with auto-adaptation of the variable process blower is new, Goldfarb said.
“We have industrialized the lower size range of the GMP dryer for U.S. production,” he said.
GMP dryers can be supplied as a single hopper version, or can be used with PTU central drying hopper modules without a process heater. Each module includes one drying hopper, support stand, heater, localized control, and main process lines and automated branch valving. Modula central drying technology then coordinates the operation of the dryers and hoppers.
The overall drying system process airflow is auto-adaptive. The dual-tower desiccant drying unit optimizes the main process airflow via inverter-controlled IE3-class (premium efficiency) process blowers to correspond to the aggregate requirements for the drying hoppers. Furthermore, the drying system design takes into consideration the ambient temperature as well as the drying requirements by examining initial and final material moisture content. A regeneration heat-recovery system further reduces the GMP dryer’s energy usage by recovering the dry regeneration exhaust in the cooling phase to reduce the process heat requirement, also eliminating cooling water requirements for regeneration cooling.
GMP dryers are available with capacities ranging from 147 to 2,060 cubic feet per minute. The dryers include a new 8-inch color touch-screen controller that is available with three different levels of automation and optimization.
Bruce Geiselman, senior staff reporter
Contact:
Universal Dynamics Inc. Fredericksburg, Va., 703-490-7000,
Bruce Geiselman
Senior Staff Reporter Bruce Geiselman covers extrusion, blow molding, additive manufacturing, automation and end markets including automotive and packaging. He also writes features, including In Other Words and Problem Solved, for Plastics Machinery & Manufacturing, Plastics Recycling and The Journal of Blow Molding. He has extensive experience in daily and magazine journalism.
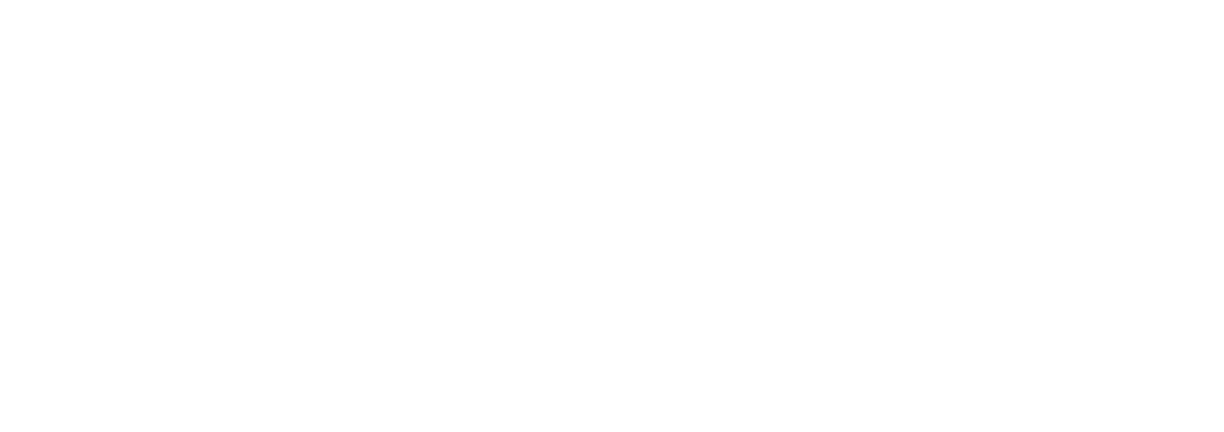